- Excess Inventory
- Frequent Delays
- Inability to Notice Delays
- Discrepancy Between Reality and Plans on the Ground
- Difficulty in Passing Down Planning Skills
- Mysterious Inventory Items Keep Increasing
- Too Much Idle Waiting
- Inability to Properly Respond to Sudden Troubles or Absences
- Time-Consuming to Respond to Delivery Dates
- Invisibility of Upstream Process Status
- The Production Scheduler Tried Out is Unusable
- Plans are Ignored Despite Careful Planning
- Inability to Grasp the Overall Situation of the Manufacturing Site
- Uncertainty About the Impact of Increasing Personnel or Equipment
- Struggle Between Sales and Manufacturing Sites
- Inability to Properly Allocate Personnel to the Right Places
- Inability to Collaborate Well with Other Planning Personnel
- Inability to Start as Planned Due to Unavailable Work Locations
- Too Many Items and Insufficient Workspaces
- Unreliable Work Instructions from the Production Management System
- Solving One Issue Causes Another
- No Time to Communicate with Relevant Departments
- Frequent Material Shortages Cause Delays
- Planning on Holidays
- Difficulty in Responding to Sudden Orders, Delivery Date, or Quantity Changes
- Inability to Increase Productivity and Generate Profit
- Forced to Rely on On-Site Judgments
- Unable to Resist Production Demands Exceeding Factory Capacity
- Items Not Available When Needed
- Production Can't Keep Up Without Overtime
- Equipment Constraints are Too Complex to Understand
Explanation: Untangling Manufacturing Industry Problems
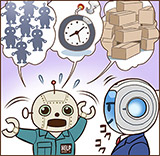
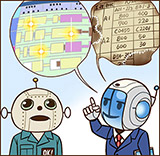
Countless Problems Erupt in the Manufacturing Site, but Like a Whack-a-Mole Game, There is No End to Being Tossed Around by Each One. In Fact, When These Problems Are Organized, It Becomes Clear That They Essentially Converge into a Few Issues.
- Updating Plans is Too Time-Consuming
- Plans Based on Actual Working TimesIt is not accurate, and the precision is low.
- The know-how and information for planning are not documentedand rely on specific individuals.
- The operation results from the manufacturing siteare not fed back into the plan.
- The plan and progress are not shared at the manufacturing site.
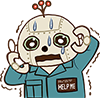
Even if you make an effort to create a plan, if changes are required, you must update it. As long as it is done manually, mistakes will occur, and the effort required for verification cannot be ignored. The more detailed the plan, the more enormous the workload becomes. Conversely, if the impact of changes is minimal and the update work is kept to a minimum, it may indicate that the plan is rough or unnecessarily secured with leeway, potentially preventing the factory from fully utilizing its capabilities.
There are countless factors for plan changes, such as sudden orders, changes in quantity or delivery dates, sudden absences of workers, or machine maintenance, and they occur frequently. If these are not addressed and left unattended, the reliability of the plan will continue to decline. However, if the person in charge of planning is engaged in the mechanical task of updating the plan each time, more important tasks, such as coordination with various departments and information gathering, which should be prioritized, will be neglected.
If such routine tasks can be entrusted to a computer, it is a natural decision to do so. Utilizing a computer can also avoid unnecessary human errors.
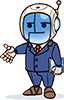
The production scheduler FLEXSCHE is package software that performs detailed and accurate planning processes at high speed. If the necessary master data is prepared in advance, you can reschedule by simply providing conditions such as orders and inventory, allowing you to update the plan as many times as needed without much effort. The time that planners spent on updating plans can be redirected to more meaningful tasks.
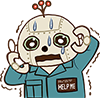
and the precision is low.
Many traditional manufacturing planning methods rely on rough "standard lead times" rather than the actual net time required for each process's work and transportation. This includes cases where planning is based on MRP in production management systems. This method estimates production quantities and resource loads in time frames (time buckets) such as weeks or days and roughly decides how much work can be packed into that period. While this method may work for mass production, it significantly impairs the accuracy of plans in complex, multi-variety, small-lot production. Additionally, as the number of processes increases, the production lead time from starting manufacturing to product completion can expand to many times the original net time, resulting in immeasurable losses.
When the conditions for changeovers (preparation and cleanup for each task) are complex, it is challenging to reasonably estimate the total working time. Additionally, if there are constraints on sub-resources (people engaged in work, tools, electricity, etc.) used during work, it may not be possible to appropriately plan an executable plan in the first place. The rough idea of pushing in a rough plan and having the manufacturing site somehow cope (such as with overtime) is no longer acceptable in today's era. However, giving a large margin to ensure feasibility and reducing throughput (factory productivity) would be counterproductive.
To create a plan that is both waste-free and feasible, it is necessary to calculate reasonable working times based on the processing capacity for each combination of resources (equipment, machines, people involved in manufacturing) and items, and to determine the start and end times of each task in detail based on various constraints. This is the production scheduling method.
In traditional methods, since it is not determined at the planning stage where the work planned within a time bucket will actually be executed within that period, the next process work would be carried out in the next time bucket (the following week or day), causing a significant extension of the production lead time. However, by determining detailed dates and times, if the work is completed in the morning, the next process can be started in the afternoon of the same day. This method can theoretically significantly shorten the production lead time, allowing for shorter delivery times. By accurately estimating each process to meet delivery deadlines, unexpected delivery delays can also be prevented. Factory operations will change dramatically.
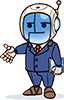
The production scheduler FLEXSCHE expresses each actual working time in seconds and directly simulates the flow of processes within the factory. If transportation is carried out after a certain process is completed within a specified time, the next process can be started immediately. Once you start using FLEXSCHE, you will realize how unreasonable planning based on standard lead times and time buckets was, causing significant losses both in terms of time and cost. A dramatic reduction in manufacturing lead time can be expected, and it will become more resilient to fluctuations due to changes in order volume.
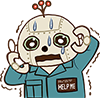
It relies on specific individuals.
In factories, there are often "planning masters" who can manage the manufacturing site even with complex constraints and special circumstances if entrusted to them, but it is often difficult for others to do the same. The know-how accumulated by the master over many years is often not documented or data-driven, making it difficult to pass on to successors. Additionally, it is not uncommon for the plans devised by the master to lack verification by a third party to determine if they are truly excellent.
The biggest problem with this "individual dependency" is the risk of the master's sick leave or retirement. There are likely many manufacturing companies that are aware of such risks but have not found a fundamental solution. To break away from this state,
it is necessary to objectively dataize
various constraints and resource capabilities,
the factory's special circumstances,
and the know-how for creating good plans, and establish a standardized planning process.
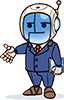
The individual dependency of planning skills is a major concern for any factory. However, the burden of manualizing or objectively dataizing those skills is significant, and appropriate methods have not been established, making it understandable to hesitate. The introduction of the production scheduler FLEXSCHE will provide an important opportunity. By describing the knowledge and know-how of the "master" in the form of FLEXSCHE's data model and scheduling rules, the inheritance to the next generation will make significant progress. By simply executing the scheduling process, most of the master's planning can be reproduced. Furthermore, the scheduling results are instantly visualized and can be objectively evaluated from various perspectives, allowing anyone to verify their validity.
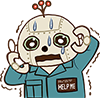
are not fed back into the plan.
Even if you take the trouble to plan and send work instructions to the manufacturing site, if the actual work results are not reflected in the next planning, the gap between the plan and reality will only widen. In reality, it is almost impossible to work exactly as planned, so feeding back the operation results is very important for making accurate plans. If neglected, the new plan may not be executed because the previously instructed work is still pending, resulting in unnecessary idle time or inefficient work instructions.
Many manufacturing companies collect operation results in some form, but many of them only use it for business analysis or cost calculation, and not many factories are fully utilizing it to improve the quality of planning. Sharing operation results in real-time across the entire manufacturing site also contributes to smooth plan execution (as described later).
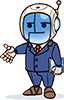
By importing operation result information into the production scheduler FLEXSCHE, synchronization between the plan (i.e., the virtual factory) and the manufacturing site (i.e., the real factory) can be achieved, preventing discrepancies. Adding operation result information as a constraint condition improves the accuracy of the next planning session.
Operation result information can vary in precision from very detailed to quite general. It may involve accurately capturing the start and end times of each operation, or simply listing the operations performed on a given day. The precision of the results is reflected in the precision of the plan, but the important thing is to feedback any level of result information into FLEXSCHE to prevent discrepancies between the plan and the site.
Furthermore, in the later mentioned FLEXSCHE CarryOut, sharing high-precision result information at the manufacturing site not only improves planning accuracy but also ensures smooth execution of the plan.
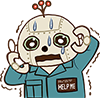
Simply sending work instructions to the manufacturing site does not guarantee smooth execution of the plan. The manufacturing site is subject to fluctuations in work time, various troubles, and sudden interruptions. When fluctuations occur, appropriate real-time responses are required. Executing the plan is as challenging and complex as planning itself.
In a manufacturing site consisting of multiple processes, the progress of the preceding process greatly affects subsequent processes. Unless sufficient buffer time is provided between processes at the cost of increased work-in-process inventory and lead time, the impact will cascade, requiring appropriate measures. For example, if you only learn about delays in the preceding process when items are not transported, the response will be delayed, resulting in significant waste. If it is possible to notify the subsequent process with an alarm when it is known that the preceding process is delayed or the work pace is slower than planned, there will be a better opportunity to respond appropriately.
Depending on the position, such as a team leader, it may be necessary to make decisions while grasping the overall progress and trouble situations. The decided intentions must be shared as a new plan throughout the manufacturing site.
In each process, progress should be input at appropriate times, and this should not only be shared in real-time but also used as operation result information for feedback into the next planning session.
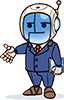
By using the system FLEXSCHE CarryOut, which supports plan execution, plans for each process and resource are distributed from a server that holds a copy of the day's plan to terminals (iPad/Android/Windows) at the manufacturing site. The status of the entered operations (such as start and completion) is shared throughout the manufacturing site, allowing affected individuals to respond appropriately. By scheduling locally on the server, plans can be updated according to the current situation. The results of fluctuations at the manufacturing site are merged as result information into the planner's schedule at a certain timing (such as the end of the day), allowing for the issuance of highly accurate plans the next day.