Seizing the opportunity of shorter delivery times, the increasing complexity of customer demands, and the impending retirement of veteran planners, we are systematizing accumulated know-how and making changes to existing operations.
- Produced in July 2022
- Download PDF for Display
- Download PDF for Printing
Marine Equipment
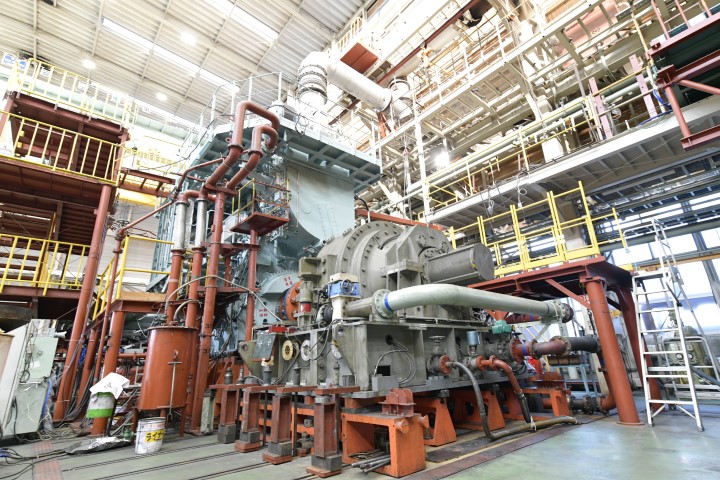
Large Marine Engine Model: 6UEC35LSE-Eco-B2
Akasa Iron Works Co., Ltd., a manufacturer of marine diesel engines that develops, manufactures, and sells large marine engines. The company adopts a make-to-order production style, handling all processes from order receipt, design, casting, machining, assembly, to after-sales support in-house. The planning of such a company's long-term and complex production plans has been considered a "special task" relying on the accumulated know-how of veteran employees. In response to shorter delivery times, product lineup complexity, and the retirement of veteran planners, the introduction of a production scheduler was considered, and FLEXSCHE, which was felt to be promising, was adopted. Not only the effects of introducing FLEXSCHE but also the insights gained during the introduction process have been used to carefully work on improving existing operations, steadily achieving results. From consideration to introduction, and future prospects, Yasuhiro from FLEXSCHE Corporation spoke with the core members of the FLEXSCHE introduction.
To address challenges such as shorter delivery times and product specification complexity
Consideration of Production Scheduler
Yasuhiro (hereafter referred to as Yas) First, could you please tell us about the overview of Akasa Iron Works Co., Ltd.?
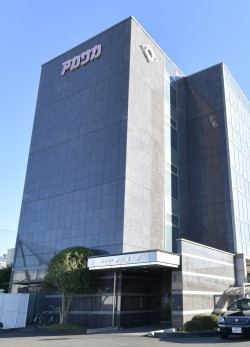
Akasa Iron Works Co., Ltd. Center Building
Nishikawa (hereafter referred to as Nishi) Our company is a manufacturer that develops and manufactures engines for ships. Founded in 1910, we celebrated our 110th anniversary last year. Originally, the company started in Yaizu, Shizuoka Prefecture, a fishing town, with an engine repair business. Later, we began manufacturing hot bulb engines, which were used as power engines for ships called "ponpon ships" in the past. As the fishing industry and fishing boats developed, we expanded our business and transitioned to manufacturing diesel engines in 1937. Furthermore, we entered the field of merchant ships carrying cargo and oil. We have been challenging issues such as increasing engine output, miniaturization, and fuel efficiency, producing products that meet the demands of the times. Under the founder Otoshichi Akasa's philosophy of "never creating machines that inconvenience shipowners or crew," we adhere to a 'customer-first principle,' providing engines and related products that delight our customers with thorough quality control and speedy service.
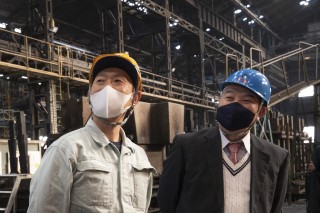
With Mr. Nishikawa (left), Manager of the Engineering and Process Section
Yasuhiro from FLEXSCHE Corporation (right)
Yas Thank you for allowing us to tour the factory earlier. I was amazed by the power of those large engines. There are various sizes and types of engines, aren't there?
Nakata (hereafter referred to as Naka) Recently, there has been a growing demand for environmentally friendly engines, and our company is also working on developing zero-emission engines and autonomous navigation technologies aimed at creating a future that is kind to both people and the planet.
Yas Could you tell us about the background of your company's consideration of a production scheduler?
Nishi The trigger was the introduction of a production scheduler at a seminar held by the Mechanical Society about three years ago. The overlap of shorter delivery times for orders, product specification complexity due to environmental compliance, and the prolonged trial runs due to the introduction of new models led to a significant amount of time being spent on scheduling. We thought a production scheduler would be an effective solution to these issues. Additionally, the impending retirement of veteran employees who had been planning production was also a push towards introducing a production scheduler.
Yas Was the production planning something only veteran employees could do?
Nishi Yes, everyone recognized it as a "job that only dedicated personnel could do."
Yas The "personalization of production planning tasks" is indeed something that happens in many workplaces, isn't it?
The realization of "this is promising" was the deciding factor for the introduction
Yas Did you consider multiple production schedulers?
Nishi Initially, we considered the product introduced at that seminar, and later, we also considered FLEXSCHE, which we found in a specialized book. We provided each with sample data of our planning information and had them create prototypes.
Yas What was the reason for choosing FLEXSCHE?
Nishi When operating the prototype, other products had many highly specialized terms and felt difficult, giving a sense of "maybe we can manage." However, FLEXSCHE was easy to understand and had excellent operability, giving us the realization of "this is promising," which was the deciding factor for its introduction. Of course, we also judged that the following four points, which our company emphasized for introduction, could be realized.
1. The ability to plan considering our company's constraints
2. The ability to flexibly respond to changes in constraints
3. The ability to easily adjust scheduling manually
4. Flexibility in setting master data
Furthermore, the ability to flexibly link data with external systems, operate intuitively with a sense close to the familiar Microsoft Excel®, and realize data input and management on the system with less effort compared to other products led to the comprehensive decision to adopt FLEXSCHE. The quick response from FLEXSCHE Corporation from inquiry to proposal and the support in providing information for internal consideration were very helpful.
FLEXSCHE Introduction Project Spanning About One Year
Yas Could you tell us about the FLEXSCHE introduction schedule?
Nishi The project kickoff and overall schedule formulation were in October 2020, and the collection of master data was from October to around December. In parallel, the setting of FLEXSCHE was carried out from October to May of the following year. A test period of about four months was set, and it actually went live in October 2021. Initially, we aimed for operation around April, but after repeated parallel run tests, we decided it would be better to operate after consultation within the company, and changed the schedule to go live in October.
Four Goals of FLEXSCHE Introduction
Nishi We set four goals for the introduction.
1. To achieve company-wide cross-sectional process management that transcends the boundaries of multiple departments with different characteristics and concepts
2. To "visualize" and improve the flow of processes and the operating status of equipment
3. To automate the scheduling of occupancy and operation of the "engine test stand" for testing manufactured engines
4. To output forms in the same format as those previously used from FLEXSCHE

"Engine Test Stand" for testing manufactured engines
Yas How to operate the engine stand is a crucial factor that significantly affects productivity, isn't it?
Nishi Exactly. Once all the engine parts are completed, assembly begins, followed by test runs on the engine stand. After completion, some parts are removed for shipment. The number of engine stands is limited, and each can operate different types of engines. The longer an engine stand is occupied, the fewer units can be produced annually, reducing the overall productivity and profit of the factory. Therefore, it is essential to determine an efficient schedule for the engine stands according to the order status.
Challenges faced and unexpected outcomes from the implementation
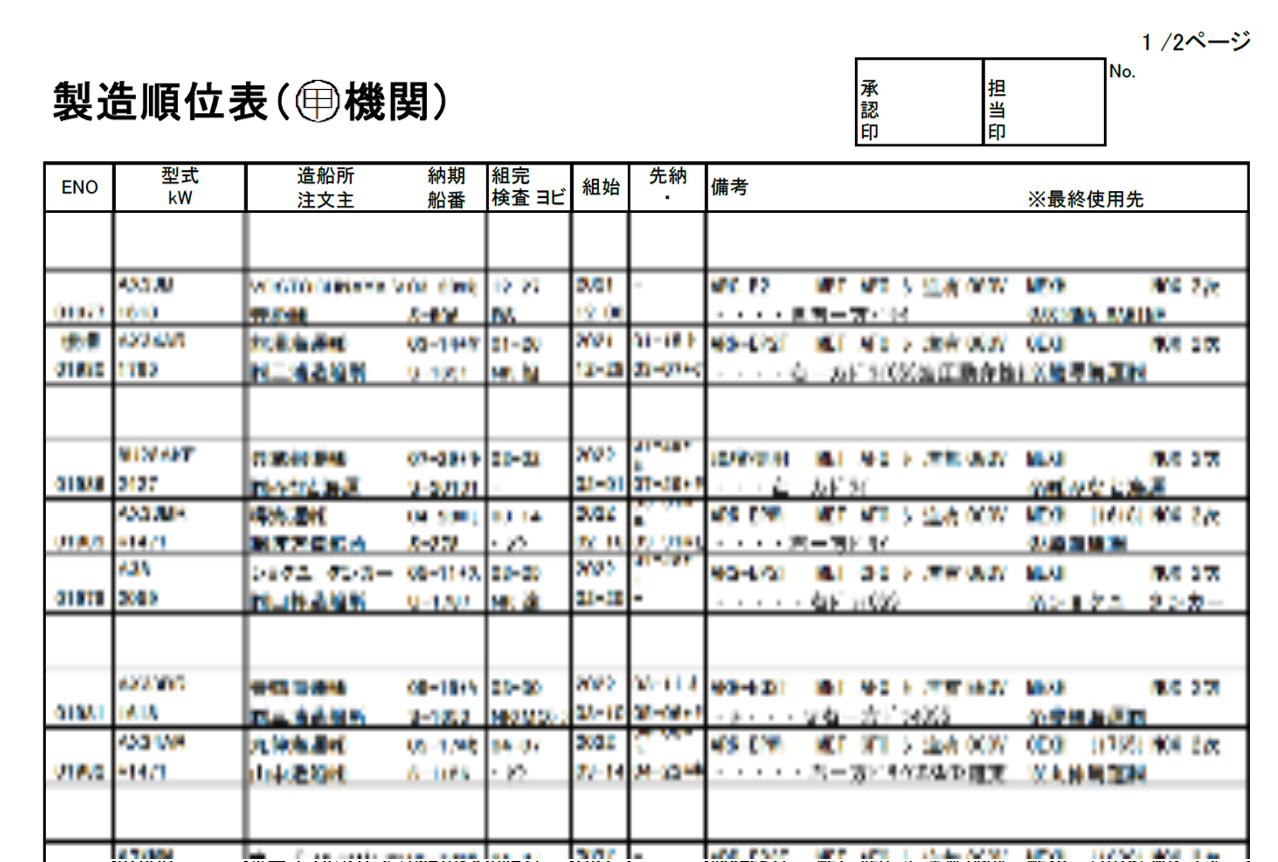
Reports (Production Order List) output from FLEXSCHE
Yas What challenges did you face during the implementation?
Nishi It was definitely the creation of master data.
Suzumoto (hereafter referred to as Suzu) We started by understanding the details of the processes. The detailed processes until each part is completed were only known by each department, so we conducted interviews at the manufacturing site to gather information on the process content and the time required for tasks.
Nishi There were several cases where different departments used different terms to refer to the same thing, and it was challenging to standardize these terms to connect them as data.
Yas Is it because the history has led to different standards being established at each site? Sometimes nuances can be conveyed between humans, right?
Nishi Being able to organize and standardize that was one of the unexpected outcomes of implementing FLEXSCHE. Not only were we able to grasp detailed information about each process, but the creation of master data itself contributed to "visualization." By reorganizing the planning method for the engine stands, which had been the center of planning until now, we realized there was a discrepancy in the company's understanding, leading us to review the conventional scheduling method. The process of creating master data highlighted the discrepancies in understanding that each department had accepted without question, providing a great opportunity to address the traditional methods.
Yas I'm glad to hear that it also contributed to business improvement. Were there any challenges on the system side?
Iketani Previously, we output the scheduling results from our proprietary core system and reflected them in reports, but we changed this to output from FLEXSCHE. This core system was an old one that had been used for about 30 years with repeated function additions, so some specification information was missing... It was a painstaking task to trace and decipher unknown specifications from the program.
Yas It seems you had various challenges.
Resolving issues such as dependency on individuals
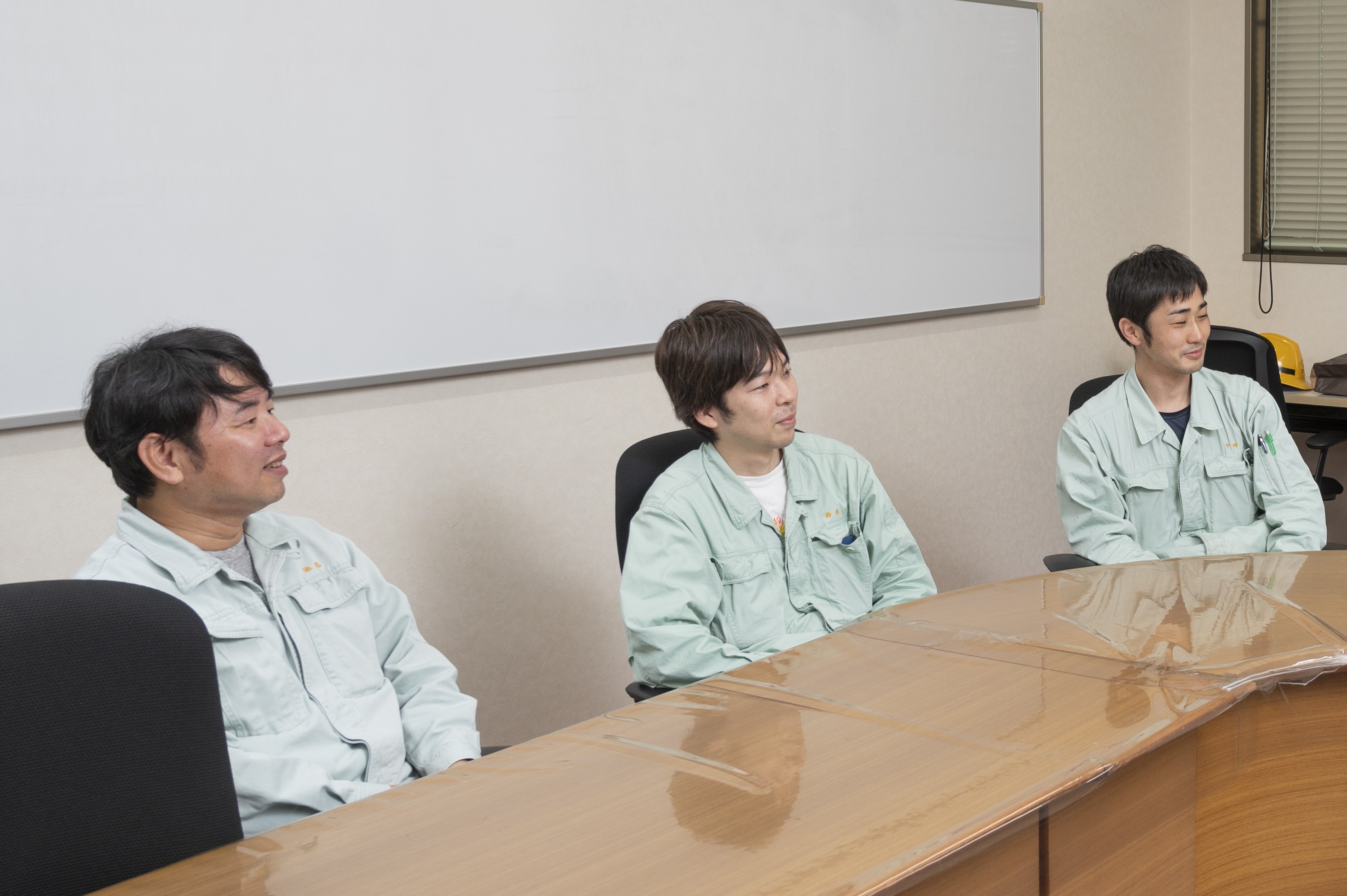
System Promotion Office, Section Chief Iketani (left)
Engineering and Process Section, Mr. Suzumoto (center)
Engineering and Process Section, Deputy Chief Mr. Nakata (right)
Yas Since the operation of FLEXSCHE, how have you felt its effects?
Nishi There are mainly four points to mention.
1. Elimination of dependency on individuals in planning
Previously, production plans were formulated based on the information held by a single planner and the person in charge of each process, but we were able to condense that know-how into FLEXSCHE. As a result, even those not familiar with the processes can now formulate plans.
2. Improvement in planning speed
Since there was only one planner, it inevitably took time to revise plans and run simulations, but after implementing FLEXSCHE, the planning speed improved, and we could respond to delivery inquiries more quickly.
3. Scheduling considering load
Previously, we only considered the overlap of engine stand occupancy and testing, and a rough estimate of man-hours for assembly and operation processes. Now, we can schedule considering the load on resources from the machining process to the shipping process.
4. Visualization of load status
Previously, the load could only be understood in each process, but now the load status of the entire factory can be visualized.
Yas Have you been able to contribute to improving productivity?
Nishi Currently, the overall order status of the factory is not yet concentrated, so verification is still to come, but we feel it is promising.
Yas Mr. Nakata, did you have any difficulties getting used to operating FLEXSCHE?
Nakata At first, I struggled a lot, but I started by understanding the meaning of each button one by one. Through the test period, I got used to it, and now I can operate it without much difficulty. I want to learn by trying various things, not just limiting myself to the way I was initially taught, and make better use of FLEXSCHE.
Aiming for further productivity improvement through simulation utilization and expansion of scope
Yas Please tell us about your future prospects.
Nishi First, we want to utilize FLEXSCHE for simulations to improve productivity. Simulating the case of increasing the compatible models of the engine stand is also easy with FLEXSCHE, so we will use FLEXSCHE to clarify the necessary equipment modifications to achieve the company's mid-term goals and plan and execute effective modification plans.
Yas So, you are looking to improve not only for the current orders but also for future order plans using FLEXSCHE.
Nishi Additionally, currently, only new orders for engines are subject to scheduling, but we also want to include spare parts for engines produced in the past. We need to discuss how far to extend the scope of FLEXSCHE, but we want to expand the scope as much as possible and make better use of it.
Yas Thank you. I'm relieved to hear that FLEXSCHE seems to continue contributing to your company's business improvement. We hope you will continue to use FLEXSCHE for a long time.
Overview of the implementing company
Akazaka Iron Works Co., Ltd.
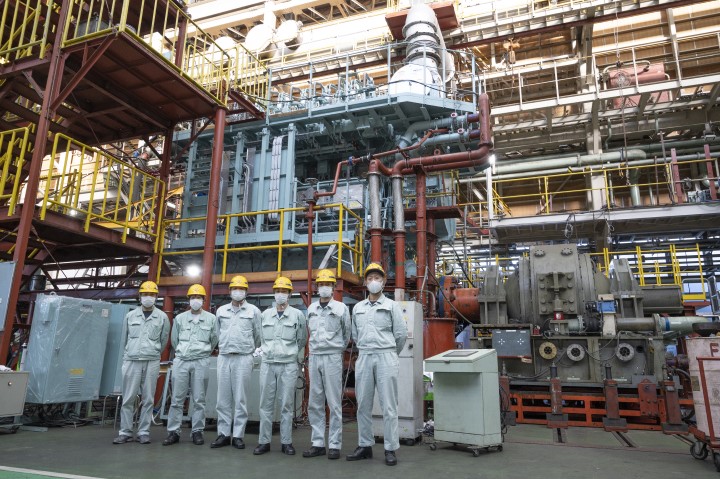
Photographed in front of the large marine engine model: 6UEC35LSE-Eco-B2
Everyone from Akazaka Iron Works Co., Ltd. (from left: Mr. Mukojima, Mr. Suzumoto, Mr. Iketani, Mr. Nakata, Mr. Kuwabara, Mr. Nishikawa)
Location | 4th Floor, Shin-Kokusai Building, 3-4-1 Marunouchi, Chiyoda-ku, Tokyo 100-0005 |
---|---|
Established | 1934 (Founded in 1910) |
Capital | 1.51 billion yen |
Number of Employees | 282 employees |
Business Overview | Manufacture and sale of marine diesel engines, manufacture and sale of various machinery and equipment |
URL | https://www.akasaka-diesel.jp/ |