Achieving seamless integration with the production management system,
Clearing a 1.5 times increase in production volume through a significant increase in equipment operation rate
Toyo Gosei Co., Ltd. Chemistry
- Created in September 2005
- Download PDF for Display
- Download PDF for Printing
Photosensitive materials for photoresists used in the manufacturing of semiconductors and LCDs, which are essential core components of digital home appliances. The production volume has been increasing annually due to the growing demand for digital home appliances. Toyo Gosei Co., Ltd. was also pressed to respond to the ever-increasing manufacturing demand, making an increase in operation rate an urgent task.
Another major challenge was performance collection. Every time a problem occurred, managers had to visit the site, and real-time progress tracking through performance collection was indispensable. Why was FLEXSCHE, a scheduler, chosen for performance collection? We asked Mr. Yoshiaki Sato of Toyo Gosei Co., Ltd. and Mr. Masuhiro Ishitobi of Mitsubishi Materials, the system provider.
Managers reached the limit of management due to the ever-increasing demand
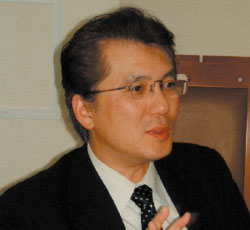
Mitsubishi Materials Corporation
Strategic Business Development Office
Solution Business Group
Industrial System Business Unit
Mr. Masuhiro Ishitobi
Toyo Gosei Co., Ltd. was established in 1954 and has a history of over half a century. Its business consists of three segments: the photosensitive materials business, which produces photosensitive materials used in semiconductor and LCD manufacturing; the chemical products business, which produces fragrance materials using advanced synthesis and separation purification technology; and the logistics business, which handles the receipt, storage, and transportation of various petrochemical products.
The introduction of FLEXSCHE this time was at the Photosensitive Materials Business Division located in the Chiba Plant. This Chiba Plant is situated in Tōnoshō, Katori District, Chiba Prefecture, and its site area is 1.2 times the size of the Tokyo Dome. The plant employs approximately 150 people, with an additional 30 workers from affiliated companies regularly engaged. The plant primarily manufactures photosensitive materials for photoresists.
Photosensitive materials for photoresists are photosensitive resins that harden or dissolve when exposed to light or radiation. They are used in the manufacturing processes of semiconductors such as ICs (integrated circuits) and LSIs (large-scale integrated circuits), making them indispensable products in the information and communication and electronics-related industries.
In the Chiba Plant, traditional production management relied heavily on manual processes, such as work instructions on paper. As a result, a significant amount of time was spent on planning. "While the time spent on planning was considerable, the greater burden was management. Since the work areas are distributed across different floors due to piping, we often had to call out to the person in charge via the factory's public address system or go directly to the site to check progress. Consequently, there were frequent delays in responding to issues when they arose."
The situation was exacerbated by the increase in product demand. With the rise in demand for digital home appliances, production volume increased significantly, by as much as 1.5 times compared to before. Although production numbers were temporarily increased, the time spent on management also increased, leading to a vicious cycle where production numbers could not be raised as desired. Time was consumed by on-site management, and at the same time, they had to cope with a 1.5-fold increase in production volume. For managers, it was truly beyond the limits of management.
"To reduce the time spent on on-site management, it is essential to be able to grasp the progress status without having to visit the site. The idea was to collect actual performance data. If the progress of work can be grasped in real-time by collecting actual performance data, there would be no need to go to the site for confirmation, and problems could be detected early. This would naturally improve equipment operation rates. Furthermore, if efficient planning becomes possible, the operation rate can be further improved. Therefore, it was decided to build a production management system, including a production scheduler."
FLEXSCHE was chosen for its ease of integration with the system
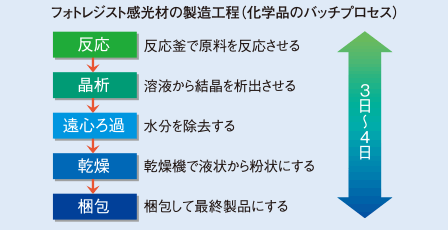
In the spring of 2004, the construction of the production management system began, but a major issue arose. It was the method of collecting actual performance data. It was found that if the method of collecting actual performance data was incorrect, it would place a significant burden on the on-site workers instead.
"If the purpose of reducing the burden on managers becomes a burden on on-site workers, it is counterproductive. Initially, we considered inputting data from computers or PDAs. However, since the factory is an explosion-proof area where fire sources and static electricity are strictly prohibited, it was necessary to leave the explosion-proof area to input data on computers, and re-entry required passing through a cleanroom. Considering this burden, it was not very realistic."
Therefore, the use of IC tags for collecting actual performance data was considered. This involved pairing IC tags with work instructions to create an "electronic kanban," which would be circulated in the production site to automatically collect actual performance data. The solution adopted was the production management system "M2SdataTube" provided by Mitsubishi Materials, which served as the base for developing explosion-proof control panels and information collection hardware, leading to the creation of the unique system Tgames (Toyo Gosei Advanced Manufacturing Excusion System).
"How to collect actual performance data for the scheduler. The solution is M2SdataTube, which uses IC tags to automatically collect actual performance data. Seamless integration with the scheduler is essential to achieve this. General package software is complete as package software, and integrating it into other systems requires significant effort. However, creating it from scratch would incur enormous costs. It was necessary to have a scheduler that, while being package software, could integrate with the production management system."
Information was gathered through the internet and exhibitions, and among the multiple candidates, FLEXSCHE was selected. The main reasons for selection were its high operability as a scheduler, the low concern of burdening workers, and its high flexibility, allowing for quick adaptation to additional functions. However, the decisive factor was its ease of integration with the production management system.
"The goal of this system was for all stakeholders to be able to grasp the information collected. Therefore, it was necessary to synchronize the computer creating the production plan with the computers displaying the planned and actual results in real-time to stakeholders. Although FLEXSCHE is a package product, it uses programming languages such as VisualBasic and VisualC++, making it easy to add functions and integrate with other systems. When considering a scheduler that could achieve what we wanted, FLEXSCHE was the last one standing." Thus, FLEXSCHE was introduced.
Equipment operation rates have significantly improved, leading to increased profits
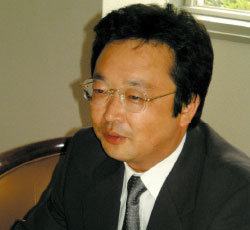
Toyo Gosei Co., Ltd.
Photosensitive Materials Business Division, Plant Management Group Leader
Mr. Yoshiaki Sato
The introduction was carried out by three parties: the integrator, the system provider, and Toyo Gosei Co., Ltd., and it took only three months from introduction to operation. The main reasons were the rapid preparation of master data by Toyo Gosei's on-site personnel and the smooth adaptation to the IC tag-based performance solution by the system provider, Mitsubishi Materials. Another significant factor was the characteristics of the FLEXSCHE scheduler.
"When introducing FLEXSCHE, we added and customized several functions. For example, a mechanism to reflect production plans created irregularly on display computers and a function to display plans and actual results that change over time in real-time. With general package software, it would be difficult to introduce such features, but FLEXSCHE's high flexibility allows for the easy incorporation of functions that seem challenging. The fact that it took only three months from introduction to operation is also due to the ease of handling FLEXSCHE."
Although training on operation and usage was received before introduction, there was some confusion immediately after introduction, and there were many inquiries to the integrator. However, due to prompt and courteous responses, issues were quickly resolved, and within a month of introduction, there were no more significant questions. Nearly a year has passed since the production management system incorporating FLEXSCHE has been in operation, and it is already achieving the intended results.
"The most significant change is that we can now collect actual performance data, allowing us to grasp progress in real-time. If there is a delay in the plan, it can be fed back to the workers as needed, enabling quick responses to issues. As a result, there is no longer a need to visit the site to check progress or call out to the person in charge via the factory's public address system, as was done before. This has significantly reduced the management burden, and even with increased production numbers, there is no confusion, and the initial goal of significantly improving equipment operation rates has been achieved. We can now stably increase production from 30 batches to 50 batches."
Another emphasized effect is that there is no burden on the on-site workers. Since automatic collection is possible by simply moving the electronic kanban with IC tags to the designated location, it does not bother the workers at all.
"While IC tags contribute to the early 'detection' of troubles, it is FLEXSCHE that aids in the early 'resolution' of troubles. Even if a delay occurs in the plan due to a problem, rescheduling allows for the immediate reorganization of the schedule, preventing significant delays from occurring even when troubles arise."
The improvement in equipment operation rate resulted in a significant increase in profits. In the fiscal year 2004, the photosensitive materials business increased by 17% to 7.942 billion yen, and the company as a whole saw a 15% increase to 11.76 billion yen. Operating profit reached a record high of 1.545 billion yen, a 94% increase compared to the previous year.
"Currently, projects are underway to integrate data with DCS (Distributed Control System), improve the material handling efficiency of automated warehouses, and horizontally deploy systems to both existing and new raw material and intermediate product factories. We aim to achieve 'visualization' of major factories and supply chain management (SCM) that controls everything from raw materials to product materials. The seamless integration with production management systems is unique to FLEXSCHE. I believe the use of FLEXSCHE will further expand in the future to realize SCM."
Voices of Integrators
Among the requests from Toyo Gosei Co., Ltd. for this system, the most important were a method of collecting results that does not burden the workers and the selection of a scheduler with good operability that also does not burden the workers.
Of course, there were areas that needed customization, but we determined that the ease of operation and the ease of integration with other systems that FLEXSCHE offers were optimal for the requirements this time.
Additionally, in this project, we were able to achieve implementation from introduction to operation in a short period of three months. Particularly, the rapid preparation of master data by the on-site personnel of Toyo Gosei Co., Ltd., the result collection solution using IC tags from Mitsubishi Materials, and the high flexibility of FLEXSCHE contributed to shortening the development period, which was effective for introducing the entire system in a short delivery time.
Currently, projects such as data integration with DCS, improving the material handling efficiency of automated warehouses, and horizontal deployment to existing and new raw material and intermediate product factories are starting. We also want to respond flexibly to various requests from our customers.
Overview of the implementing company
Toyo Gosei Co., Ltd.
Head Office | 1603 Kamimyojin, Ichikawa City, Chiba Prefecture |
---|---|
Chiba Factory | 1-51 Miyanodai, Tono-cho, Katori-gun, Chiba Prefecture |
URL | http://www.toyogosei.co.jp/ |
Established | 1954 (Showa 29) |
Business Description |
Manufacture of photosensitive materials used in semiconductors and liquid crystal panels. Manufacture of chemical products that serve as intermediates for pharmaceuticals, paints, fragrances, etc. Receiving, storage, and transportation of a wide variety of petrochemical products. |
Sales | 11.76 billion yen (Fiscal Year ending March 2005) |
Listed | JASDAQ |
Number of Employees | 313 employees |
System Provider Information
Mitsubishi Materials Corporation
Head Office | 1-5-1 Otemachi, Chiyoda-ku, Tokyo |
---|---|
URL | http://www.mmc.co.jp/ |
Established | 1950 (Showa 25) |
Business Description | From basic materials such as non-ferrous metals and cement to metal processing, aluminum can manufacturing, semiconductor-related and electronic products, energy, and environmental business |
Sales | Consolidated 984.7 billion yen, standalone 531.2 billion yen (Fiscal Year ending March 2005) |
Listed | TSE First Section |
Number of Employees | Consolidated 18,477 people, standalone 4,904 people |