Implemented in the three main factories of Prime Polymer to achieve standardization of production planning operations.
Introduced based on the evaluation of results at Mitsui Chemicals and Mitsui-DuPont Polychemical.
Prime Polymer Co., Ltd. Chemistry
- Produced in March 2018
- Download PDF for Display
- Download PDF for Printing
Prime Polymer, leading the domestic polyolefin business, was born as part of a comprehensive alliance between Mitsui Chemicals and Idemitsu Kosan. The company has introduced FLEXSCHE as a production scheduler to promote the standardization of production planning operations in factories of different origins and improve productivity.
The company introduced it to the Anesaki factory in 2008, evaluated the results, and expanded it to the Ichihara and Osaka factories, and further introduced it to Mitsui Chemicals and Mitsui-DuPont Polychemical, which handle similar products. The reason for expanding the adoption of FLEXSCHE is due to its highly regarded flexibility. While achieving standardization centered on FLEXSCHE, they continue to evolve the system to be more user-friendly by leveraging FLEXSCHE's flexibility.
Improve overall factory productivity through the standardization of production planning operations.
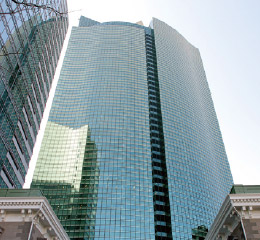
Prime Polymer Co., Ltd.
In 2005, Prime Polymer Co., Ltd. was established as part of a comprehensive alliance between Mitsui Chemicals, Inc. and Idemitsu Kosan Co., Ltd. to enhance the international competitiveness of their polyolefin business in the increasingly competitive global chemical industry. The company integrates production, sales, and research in the polyolefin business that both Mitsui and Idemitsu have developed globally, aiming to expand business scale and maximize business value. The core of the company's business is two synthetic resins: polyethylene, widely used in bags and containers, and polypropylene, a lightweight and heat-resistant material used in a wide range of fields such as automotive parts and home appliances. The company, boasting one of the largest production scales in Japan for these two synthetic resins, aims to become the most trusted partner, "Prime Solution Partner," by providing stable and sustainable products, technologies, and services to customers.
The company's domestic factories are located in Kanto, Kinki, and China, ensuring inventory at stock points nationwide to achieve stable supply to customers.
At the time of the company's establishment, improving productivity was a crucial point to enhance the synergy effects of the integration.
Mr. Shotaro Matsuda from the Business Support Group, System Department, Mitsui Chemicals, Inc. (who was with Prime Polymer Co., Ltd. until March 2015) talks about the productivity challenges at that time.
"Since the factories of companies with different backgrounds came together, the Ichihara factory used an existing third-party production scheduler, the Osaka factory had a manually developed system, and the Anesaki factory used Excel for manual production planning, with different methods and tools for production planning. The differences in production planning methods and the personalization of operations became challenges in achieving the integration of business processes and operations and improving productivity."
The company decided to introduce a new production scheduler to improve the overall productivity of the factories and standardize operations. The project to introduce the new production scheduler started in 2007. "The first factory to consider the introduction was the Anesaki factory. Since the factory created production plans using Excel, the workload during plan changes was high, which also led to a standardized operation of reducing the frequency of production plan revisions, resulting in lost sales opportunities and high inventory levels. Introducing a production scheduler was urgent to quickly escape from this situation."
* Polyolefin is a general term for olefin-based polymers.
Selected FLEXSCHE as a production scheduler applicable to multi-variety continuous production processes
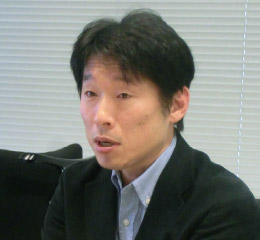
Mitsui Chemicals, Inc.
System Department, Business Support Group
Manager Shotaro Matsuda
(With Prime Polymer Co., Ltd. until March 2015)
Prime Polymer Co., Ltd.
The company's manufacturing is characterized by a multi-variety continuous production process. In the production of polypropylene and polyethylene, raw materials are continuously fed into large reactors, producing dozens of different products continuously in a single plant.
To minimize losses, production is carried out by sequentially changing to similar properties. "Under complex conditions such as approximately 700 brands and over 1,000 customers, production planning that utilizes human know-how has become established as a 'culture,' and aiming for fully automated scheduling did not fit our corporate culture," says Mr. Matsuda.
The concept of the production scheduler sought by the company is "to thoroughly automate areas where human thinking is meaningless and efficiently utilize information in scenes requiring human judgment, allowing experience-based decision-making to be fed back into the plan" (Mr. Matsuda). The production scheduler to realize this concept required excellent flexibility.
They also emphasized integration with surrounding systems. "It was important not just to introduce a production scheduler but to incorporate it into our business system. By linking with the master and data managed by our unique internal system STAFF (S-Navi)* and other business systems, we aim to enhance the speed and quality of operations.
It was also necessary to respond to the needs of our production planning cycle, such as linking the results to core systems (SAP) and SCP (Supply Chain Planning) systems." How to realize a production scheduler that can leverage the corporate culture in the company's manufacturing. The company chose FLEXSCHE as the production scheduler to solve this challenge.
Regarding the reason for choosing FLEXSCHE, Mr. Matsuda says, "Existing third-party production schedulers had issues with flexibility and required a lot of time and cost for customization.
On the other hand, FLEXSCHE had flexibility that made customization easy and had an advantage in terms of cost performance. In addition to the reassurance of the developer being based in Japan, the fact that Yokogawa Solution Service, which supports the construction and operation of our system, was a partner of FLEXSCHE was also a point."
In terms of integration with surrounding systems, they also evaluated the point that it can flexibly and easily achieve integration with other systems via CSV files, rather than tightly coupling systems.
* "S-Navi" is a web portal that centrally manages the master and data necessary for production management.
* "STAFF" is a general term for a business portal site with various functions such as sales planning, sales management, and inventory management.
Introduced to the three main factories of Prime Polymer
Also introduced at Mitsui Chemicals and Mitsui-DuPont Polychemical
In the summer of 2008, the company decided to adopt FLEXSCHE, conducted a fit & gap analysis, and began design. The focus in design was the operational perspective of "easy to use in actual business." For example, in customizing the calculation logic for rearranging production order, they incorporated what humans had been thinking in their minds into the calculation logic.
"In our company, when deciding the quantity and timing of product production, it is necessary to predict the inventory of that product at the next production timing. In the past, adjustments to the plan when changes occurred were done manually by comparing the supply-demand balance sheet and the production plan sheet, but now, when the planner inputs the desired production order, the production scheduler calculates how much should be produced in that order. By changing the production order master and production cycle, simulation is also possible."
Started using FLEXSCHE for monthly planning from the end of 2009. Began using FLEXSCHE for annual planning (budget) from the 2010 fiscal year. "When creating a monthly plan with Excel, everything had to be transcribed, but that hassle is no longer necessary. Also, the annual plan (budget) was previously all manually input, so it was difficult when changes occurred. Now, by utilizing calculation logic, we have automated the process, completing work that used to take a week in a few hours," says Mr. Matsuda.
The company evaluated the performance of FLEXSCHE at the Anesaki factory and expanded it to the Ichihara and Osaka factories, and also introduced it at the factories of Mitsui Chemicals and Mitsui-DuPont Polychemical, which handle similar products (Figure 1). They have developed the system by enhancing usability and utilizing new features of FLEXSCHE.
For example, in the 2011 expansion to the Ichihara factory, they enhanced the planning editing functions based on FLEXSCHE's operation sequence chart, which adjusts the work order on each resource.
"In our company, the creation of production plans is not about recreating future plans each time, but rather evaluating and reviewing existing plans based on the latest inventory information and market trends. The ability to quickly output reports such as supply-demand balance sheets and easily make corrections on the editing screen directly contributes to the acceleration of planning tasks."
The challenge in horizontally deploying the production scheduler was how to respond to the demands of each factory without changing the basic framework. "Advancing standardization with FLEXSCHE as the axis was understood by the personnel at each factory," says Mr. Matsuda. The key point in this system is the integration between the company's internal system "STAFF" and FLEXSCHE (Figure 2). The existing production scheduler was not linked with "STAFF," so manual input was required every time the master was changed. Now, when a new item is added to the core system SAP, the master is automatically updated, allowing the use of new items in FLEXSCHE.
It is also characteristic that from the S-Navi screen, which serves as the portal for the company's business system, the master of FLEXSCHE can be managed, and the latest CSV files can be output immediately. Downloading data such as the latest monthly production plans can also be easily done through S-Navi.
"Because FLEXSCHE allows for flexible model construction, it is easy to foresee that maintaining the accuracy of the master becomes difficult when creating complex multi-item models with only the standard master maintenance functions. By designing and constructing with the premise of integration with S-Navi from the beginning, we were able to compensate for this weakness, improve user convenience, and ensure smooth system operation. Additionally, since sales plans, orders, and inventory data are held in the same database as the master, it is possible to notify users via alert emails when sales or inventory not registered in the master occur," says Mr. Matsuda.
The S-Navi system is also adopted and utilized by Mitsui Chemicals and Mitsui-DuPont Polychemical, which have introduced FLEXSCHE.
Standardization of production planning operations achieved; information sharing using SNS also started
Regarding the effects of introducing FLEXSCHE, Mr. Matsuda says, "The realization of company-wide integration of production planning operations and their tools, which previously differed for each factory, has enabled standardization of operations and sharing of know-how. The efficiency of the production management department at the headquarters, which manages the production of the entire factory, has also improved. Additionally, the personalization of operations has been eliminated, and the rotation of personnel is smooth."
Not only the factories but also the production management department at the headquarters is utilizing FLEXSCHE. To respond to the ever-changing market, various packaging plans from flexible containers to 25kg bags are automatically calculated using the latest sales forecast data provided by S-Navi.
With the introduction of FLEXSCHE to the main factories completed, the company is now listening to user feedback again and working on system and operational improvements. As part of this effort, they are using groupware to share information among users, system administrators, and Yokogawa Solution Service. "Inquiries and sharing of know-how have been sped up. Additionally, since past experiences can be accumulated, effective use of information is possible. Since production planners work within the factory, we will continue to actively expand horizontal connections with users who are far away."
Regarding future prospects, "We are currently using FLEXSCHE as a platform, but optimizing the division between the package's standard functions and customization functions to enhance consistency as a single tool is considered a future challenge. Although Yokogawa Solution Service has helped us develop the production scheduling system with FLEXSCHE, it is still in the process of evolution. We ask for your continued cooperation to further grow the system together with our company," says Mr. Matsuda.
As a "Prime Solution Partner," Prime Polymer contributes to the development of customers' businesses. As a key part of production planning operations that provide products to customers stably and sustainably, FLEXSCHE will continue to support the company's business and trust.
Figure 1 Introduction of the Production Scheduling System
Figure 2 Overview of the Production Scheduling System at Prime Polymer
Partner's VoiceYokogawa Solution Service Corporation
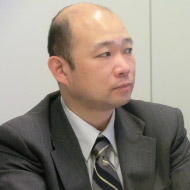
ERP Business Division
Solution 2 Department 3Gr Chief
Mr. Kenji Hayakawa
Since Prime Polymer began considering the standardization of production planning operations in 2007, the production scheduler has been adopted at the Anegasaki Plant, Ichihara Plant, Osaka Plant, and even at the factories of Mitsui Chemicals and Mitsui-DuPont Polychemical. Our company has been involved in the process of system growth over many years.
Under the leadership of Mr. Matsuda, the project leader, the valuable experience of growing the system has also contributed to the growth of our engineers. One of the things we learned from this project is the importance of always considering "how should the system used in business be" while working.
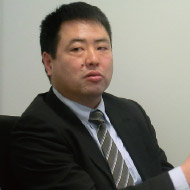
ERP Business Division
Solution 2 Department 3Gr
Mr. Yu Nozawa
It was very meaningful to be able to hear the voices of the users. At that time, we initially had difficulty understanding the unique terms of the field, but with the help of the company's information systems department, we were able to grasp the needs of the field.
The production scheduler is indispensable not only for the company but also for the development of the businesses of the customers to whom the company provides products.
We will continue to make efforts to further grow the system together with the company as its partner.
Overview of the implementing company
Prime Polymer Co., Ltd.
Head Office | 1-5-2 Higashi-Shimbashi, Minato-ku, Tokyo, Shiodome City Center |
---|---|
Established | April 1, 2005 |
Capital | 20 billion yen (Mitsui Chemicals 65%, Idemitsu Kosan 35%) |
Number of Employees | 712 employees (as of the end of March) |
Factory and Research Institute | Ichihara Plant, Anegasaki Plant, Osaka Plant, Packaging Material Research Institute, Automotive Material Research Institute |
Business Overview | Manufacturing, processing, and sales of polypropylene resin and polyethylene resin |
URL | http://www.primepolymer.co.jp/ |