Transfer of planning operations from the field department to the management department through standardization
Expand overseas bases utilizing the know-how of FLEXSCHE cultivated domestically
PIOLAX, Inc. Automotive Parts
- Produced in May 2015
- Download PDF for Display
- Download PDF for Printing
Pioneer Corporation, a global developer and manufacturer of automotive-related parts, started a project to implement SAP and FLEXSCHE in 2002 to build an integrated system from production planning to logistics. At that time, production planning operations relied on the experience and know-how of the person in charge, and handling during their absence was a major issue. In selecting a production scheduler aimed at standardizing production planning operations, the ease of integration with SAP and user-friendliness were highly evaluated, leading to the adoption of FLEXSCHE.
Eight years have passed since its operation, and FLEXSCHE has become an indispensable presence in production planning operations.
A major change was the transfer of production planning operations from the field department to the management department through standardization. In addition to realizing a system where production planning operations can be seamlessly inherited even when personnel change, field managers who previously spent time creating production plans can now focus on their primary duties.
Furthermore, to standardize production planning operations at overseas bases by utilizing the know-how of FLEXSCHE cultivated domestically, the introduction of ERP and FLEXSCHE is underway at the Thai base. The system built at this Thai base is planned to be expanded to other overseas bases.
System development to support a global supply system
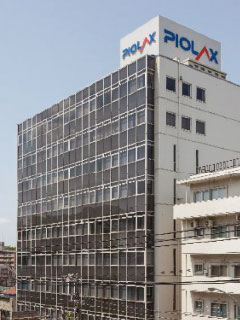
Pioneer Corporation
Founded in 1933, Pioneer Corporation, with over 80 years of history, is a leading developer and manufacturer of automotive-related parts in Japan. More than 1,500 of its products are used in a single car for applications such as fuel systems, drive systems, and fasteners.
For example, there are numerous springs used in transmissions, snap rings for assembling parts, various plastic fasteners, and metal fasteners for securing automotive interior and exterior parts and piping to the vehicle body. The company, which has established a high reputation in the automotive industry, is a pioneer in "elasticity" technology.
Elasticity refers to the property of an object to rebound against applied force, and the company's strength lies in handling both metal and synthetic resin. The company's excellent elasticity technology is attracting attention from global automobile manufacturers, and air dampers used to softly open and close glove boxes are installed in major car models worldwide.
In recent years, the automotive industry has been rapidly expanding globally. The company is proactively responding to this trend by establishing nine bases in eight countries across the United States, Asia, and Europe, and developing a global supply system. As part of this, the introduction of ERP and the production scheduler FLEXSCHE is underway to improve productivity and centralize information management at overseas bases. The information system supporting the company's global business expansion leverages the know-how cultivated in Japan.
Adopted FLEXSCHE for its ease of integration with SAP and user-friendliness
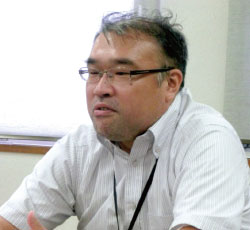
ERP Promotion Department, System Group
Manager Yasuhiko Togashi
In 2002, the company's core system used a host computer for logistics and accounting operations, but with increasing competition, it was decided to renew the core system with a view to the future. To build an integrated core business system including production planning, the company decided to implement SAP. As customer needs shifted from single-item delivery to module delivery combining multiple parts, operations became more complex, and systematizing production planning operations became urgent.
"At that time, production planners at each production site were creating monthly production plans using Microsoft Excel, but since production planning relied on the experience and know-how of the person in charge, handling during their absence was a major issue. Also, the planning methods varied by site, so the 'quality' was not unified. The created production plans were also difficult to understand at a glance," says Yasuhiko Togashi, Manager of the ERP Promotion Department, System Group at Pioneer Corporation.
The basic policy for systematizing production planning operations was to divide the monthly production plan, which was manually done, into two buckets using SAP's MPS (Master Production Schedule). However, the problem was how to translate the production plan drafted in one bucket per half-month into a detailed plan. "Our factories produce as many as 100 million units per month, with a large number of machines and lines. Under these conditions, a production scheduler was indispensable to systematize planning operations in detail," says Togashi.
After thoroughly examining multiple products as production schedulers to systematize complex production planning operations in conjunction with SAP, the company chose FLEXSCHE. Regarding the reasons, Togashi explains as follows.
"Having the functionality to realize what we wanted to do was a mandatory requirement. Also, we didn't want to spend money on the interface between SAP and the production scheduler, so flexibility to develop it within our system department was necessary. FLEXSCHE was highly evaluated for its ease of integration with SAP through file exchanges. Additionally, the simplicity of the operation screen made it easy to see what was being produced where at a glance. FLEXSCHE, along with other scheduler products, was demonstrated using sample data, but it received the highest evaluation among the actual users. Of course, it also excelled in cost performance."
In 2003, the adoption of FLEXSCHE was decided, but due to delays in the construction of SAP, it became fully operational in 2006. In 2007, FLEXSCHE was upgraded to achieve dynamic changeover and automatic order pegging.
Display items on the FLEXSCHE screen according to the color of the parts.
By upgrading FLEXSCHE, it became easier to plan by automatically arranging operations prioritizing arbitrary items such as plate thickness, temperature, and color, thereby reducing changeover times and improving productivity. "There are many parts with the same shape but different colors. When producing items of the same color consecutively, we have devised a way to display items on the FLEXSCHE screen according to the color of the parts, allowing for intuitive arrangement by appearance," says Mr. Togashi.
The integration of SAP and FLEXSCHE involves transferring master information and instruction information from SAP to FLEXSCHE, creating process plans based on that in FLEXSCHE, and then reflecting the results back to SAP. Data exchange is conducted through a master developed as an add-on for FLEXSCHE in SAP.
"The master for FLEXSCHE was designed by Ines, and I developed it. Ines provided support to ensure it could be truly used on-site, including revamping the SAP implementation, developing add-ons for the FLEXSCHE implementation, and conducting training at the factory. I believe we succeeded thanks to Ines' full cooperation," says Mr. Togashi. Ines, boasting extensive experience in SAP implementation, is also a partner company of FLEXSCHE with excellent technical capabilities.
The master for FLEXSCHE is updated every morning through nighttime batch processing. Whether or not to actually send it to FLEXSCHE is left to the discretion of the user, considering the handling of emergency orders, but the basic operation is to avoid major changes to the plan.
"To achieve efficient production with FLEXSCHE, we initially standardized on confirming up to three days ahead, but now we are flexibly allowing confirmations one day in advance," says Mr. Togashi.
Transfer of production planning operations from the field department to the management department through standardization.
Since becoming fully operational in 2006, eight years have passed, and FLEXSCHE has become an indispensable presence in the company's production site. The first benefit Mr. Togashi mentioned from the introduction of FLEXSCHE is that "even if the person in charge changes, planning operations can continue."
"By standardizing planning operations, it has become possible for people who have moved to the workplace or those without manufacturing experience to create production plans without relying on experience or know-how, and the planning operations that were conducted on-site have been transferred to the management department. Previously, production plans were often created by the site manager, taking up half of the month for planning. However, now the site manager is freed from planning operations and can focus on their original duties. Additionally, systematization has significantly reduced the man-hours required for planning operations," says Mr. Togashi.
In terms of efficiency, by printing and posting the FLEXSCHE screen or displaying it on a monitor, each operator can understand "what to produce today" for each piece of equipment, allowing them to perform tasks anticipating the next changeover.
A system has been established domestically to create production plans without relying on individuals. The next step was the standardization of planning operations at overseas bases, which became a challenge. In overseas locations where personnel movement is frequent, the standardization of planning operations is even more necessary.
In 2013, the construction of a system for the introduction of ERP and FLEXSCHE at the Thai base began. From a cost perspective, an ERP other than SAP was selected. Since the production scheduler is directly linked to production efficiency and quality, FLEXSCHE, which has accumulated know-how, was adopted in the same way as domestically. Support was also a key point in the adoption of FLEXSCHE. "Having introduced FLEXSCHE domestically for eight years, I am very satisfied with the speed of response when in trouble. I believe that in the global deployment of systems, the speed of response and support capabilities will become even more important," says Mr. Togashi.
The plan is to standardize the system currently being constructed at the Thai base and expand it to other overseas bases. Regarding future prospects, "The global deployment of a system that integrates ERP and FLEXSCHE, which supports our production, is an important theme.
Regarding domestic matters, upgrading FLEXSCHE is also a consideration. By utilizing FLEXSCHE EDIF (External Data InterFace), integration with SAP can be made easier, and we aim to fully utilize FLEXSCHE's functions to further improve the efficiency of production planning operations," says Mr. Togashi.
Paiolax, based on advanced elastic technology, is expanding its business fields beyond the automotive industry to medical and lifestyle sectors. FLEXSCHE will continue to support the company's global advancement.
Partner's Voice
In the introduction of SAP and FLEXSCHE for Paiolax, we supported from requirements definition to full operation. Initially, Ines participated in the project as a sub-consulting company, but during the SAP restart, we received an evaluation from Paiolax that "they understand the business content best," and since then, we have been active as the main contact.
What we value in our consulting activities is understanding the true intentions of our customers. Initially, SAP was proceeding with a big bang implementation, but we sensed that Paiolax was worried about the significant impact on management if the accounting system did not go well, and proposed the prior introduction of the production management system to the factory. In the SAP implementation, we also developed a "master maintenance tool" that allows anyone to easily input and replace master data for each product without errors. The "master maintenance tool" is based on our product AerpsMASTER. In the introduction of FLEXSCHE, we believe that the results were achieved by working together with Paiolax on various themes, such as add-on development for the FLEXSCHE master and training at the factory.
We will continue to support Paiolax in effectively utilizing SAP and FLEXSCHE to further improve productivity and operational efficiency.
Overview of the implementing company
Pioneer Corporation
Established | September 1939 (Showa 14) |
---|---|
Capital | 2,960,970,000 yen (as of March 31, 2014) |
Sales | 33.3 billion yen (standalone) / 54.7 billion yen (consolidated) (as of March 31, 2014) |
Business Overview | Manufacture and sale of coil springs, thin plate springs, wire forms, metal and synthetic resin fasteners, and unit mechanism parts. |
URL | http://www.piolax.co.jp/ |