A scheduler that fits the complex manufacturing style
Significant reduction in planning time and lead time
Hamamatsu Photonics K.K. Electronic equipment
- Created in June 2005
- Download PDF for Display
- Download PDF for Printing
"How can we shorten the scheduling time?"
The System Manufacturing Department of the System Division at Hamamatsu Photonics K.K. has long faced this issue. They repeatedly tried various approaches every year, but did not achieve the desired results. Two years ago, they finally decided to introduce FLEXSCHE, realizing that "something must be done to improve this situation."
"We are not yet fully proficient in using it, but we are already seeing results," says Takuya Machida of the First Manufacturing Group. How has the introduction of FLEXSCHE changed the manufacturing site? We asked Takuya Machida and Motofumi Yamada, also from the First Manufacturing Group.
Longer scheduling time due to complex processes and high-mix low-volume production

System Manufacturing Department, System Division
First Manufacturing Group
Takuya Machida
Hamamatsu Photonics K.K. was founded in 1953 and boasts a history of over half a century. They mainly manufacture photomultiplier tubes, image devices and light sources, optical semiconductor devices, and image processing and measurement equipment. The 20-inch photomultiplier tubes used in the "Super-Kamiokande," led by Masatoshi Koshiba, Director of the Heisei Foundation for Basic Science, who won the Nobel Prize in Physics, were also made by Hamamatsu Photonics.
The System Manufacturing Department's First Manufacturing Group, which introduced FLEXSCHE, is located in the Tsudacho Factory and Joko Factory in Hamamatsu City, with about 50 employees. Here, various digital cameras for detection, mainly for universities and research institutions, and image processing and measurement equipment are manufactured.
The digital camera process is broadly divided into three parts. The first is the "substrate process," mainly manufactured with a mounter, and this work is done at the Joko Factory. The second is the "wiring process," which involves wiring that connects the camera and controller, handled by outsourcing. The third is "assembly and adjustment," where the completed substrates and wiring are assembled and inspected for entry, handled by the Tsudacho Factory.
"In broad terms, there are these three processes, but when you include the finer processes, there are as many as 40, making the process very complex compared to other industries. Furthermore, since assembly and adjustment are all done manually, it cannot simply be a flow operation. Therefore, planning inevitably takes time."
The trend of "high-mix low-volume production" further exacerbated the issues of complex processes and manual work. As small-lot production progressed, the types of cameras, such as high-sensitivity cameras, near-infrared cameras, and ultraviolet cameras, increased significantly to meet client demands.
"In the past, all planning was done by hand, but that took too much time, so we started using Microsoft's scheduling management software, Microsoft Project. Although it became visually easier to understand, it was not automatic scheduling, so ultimately, people had to create the schedules, and we did not achieve the desired effects, especially in terms of scheduling."
In the First Manufacturing Group's planning, Machida first created the large schedule, Miyazaki from the Joko Factory handled the substrate process, Yamada handled the outsourced process, and Machida handled the assembly and adjustment, but it took an enormous amount of time, especially at the Joko Factory, where it took 10 hours to plan a week's schedule.
There was also another major issue: inventory. To reduce inventory, they responded with forecast production for items expected to be ordered and made-to-order production for those not expected, but they still ended up with inventory. They concluded that "to reduce inventory, we must shorten lead times and increase turnover rates."
To overcome these two challenges of shortening scheduling time and lead time, they finally decided to introduce a scheduler and began reforms. This was in the spring of 2003.
The high level of flexibility was the deciding factor for introducing FLEXSCHE
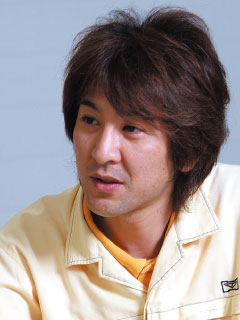
System Manufacturing Department, System Division
First Manufacturing Group
Motofumi Yamada
The project team consisted of Machida, Yamada, and Miyazaki from the Joko Factory. The three of them struggled with the question of "which scheduler should we introduce?"
"The most important factor was whether the scheduler could accommodate our manufacturing style. The processes for digital cameras and measuring instruments are very complex, and the work is mainly manual rather than machine-based. Additionally, there are many changes in materials, so we thought there would be no point in introducing a scheduler that could not handle such special conditions in our manufacturing style."
They gathered information through the internet and exhibitions. Among them, four or five schedulers remained as candidates. Based on standard features such as the ability to handle Microsoft Excel CSV data, create summary plans, split tasks, and set work constraints like employee holidays, they narrowed it down to two schedulers.
"The other scheduler had many standard features, but it lacked all the features we really wanted. In fact, that scheduler was used by another division, and when I talked to the person in charge, they said, 'It's suitable for industries with few processes, but not for complex processes.' Even when we asked the manufacturer, 'Can you implement this feature?' they said, 'It's difficult.' But FLEXSCHE said, 'We can do that.' It has very high flexibility. Since it also seemed to fit within our budget, we ultimately decided on FLEXSCHE."
The introduction of FLEXSCHE was handled by a project team of three people for functions and specifications, while a female employee was responsible for registering the master data. The presence of the integrator was a significant force in the implementation.
"Since it was our first time, we didn't know where to start, but the integrator showed us the path to implementation, which made the subsequent work smoother."
With the help of the integrator, the project team worked on examining how to use the standard features and identifying what needed to be customized.
"The requests extended to very detailed parts, so I thought everything would need to be customized, but upon inquiry, we found that many things could be used with the standard features, and with the support from FLEXSCHE, we were able to use them. We supplemented the missing parts with paid support, allowing us to incorporate most of the requested features."
Among them, the 'Official Name Search Function' was particularly helpful.
"There were two names for the orders, a provisional order name and an official name, but we only knew about the provisional orders and were struggling to retrieve the official name orders. It became easy to search for them. This convenience left a particularly deep impression."
When introducing FLEXSCHE, the project team was careful not to "cause confusion on the shop floor." Since the work schedule was previously managed using Microsoft Project, they judged that showing the FLEXSCHE data directly would cause confusion. Therefore, they extracted the necessary CSV data from FLEXSCHE and imported it into Microsoft Project, allowing them to provide a work schedule that looked unchanged from before.
In March 2005, FLEXSCHE was trialed, and it has been fully operational since April.
Immediately after implementation, the lead time was reduced from 10 working days to 8 working days.
The master data registered in FLEXSCHE covers almost all products, and the registration of resources extends to all workers and subcontractors at Joko Manufacturing, as well as the mounters. They also set work constraints such as each employee's capability values and holidays, and managed multiplex resources. As a result, there was a significant change: the number of planners was reduced to one.
"Previously, Machida would create the main schedule, and then three people would divide the detailed schedules for the boards, subcontracting, assembly, and adjustment. However, with FLEXSCHE, once the main schedule is created, it is directly reflected in the medium and small schedules, making it possible to just check them."
FLEXSCHE has shown particularly significant results at Joko Manufacturing. The planning time has been significantly reduced from the previous 10 hours per week to 6 hours per week, allowing them to use the freed-up time to tackle the next improvement theme.
"At Joko Manufacturing, there are requests without data, which we call 'business requests,' and adjustments are necessary to incorporate them, but everything else can be handled by FLEXSCHE, resulting in the expected effects. The work instructions have changed to detailed instructions like 'from what time to what time,' but since the schedule is feasible, there have been no complaints from the shop floor so far."
Additionally, the challenge of reducing lead time has been addressed, with the lead time from assembly to storage reduced from 10 working days to 8 working days. "Honestly, I'm not entirely sure why it led to a reduction. However, at least I can say that as soon as we introduced FLEXSCHE, the lead time shortened. Previously, the schedule was somewhat relaxed, but now that we can schedule in detail by the hour, the 'margin' has been compressed, leading to the reduction. Although it's still early days since the introduction, and we haven't reached inventory reduction yet, if the lead time continues to shorten, clear effects should emerge."
Overcoming challenges and aiming for further improvement
It's only been a few months since the introduction of FLEXSCHE, but they are looking to step up further, saying, "We want to clear each challenge one by one in the future." "Joko Manufacturing went well, but there is still room for improvement in the time spent on planning at Mikata Manufacturing. One of the causes is our internal company rules. When we have other divisions process materials, there are detailed rules like having to deliver materials by a certain day of the week, so negotiations with other divisions on how to incorporate them are necessary. Also, special materials have fixed delivery dates, so we need to think about how to adjust and meet the deadlines. By gradually clearing these issues, we want to further enhance the effects of introducing FLEXSCHE."
Handling MRP data during outsourcing was also a major challenge. We provide MRP data to subcontractors, but since it slightly differs from FLEXSCHE data, Mr. Yamada acted as an interface, identifying the differences and replacing them with MRP. "Overall, I am very satisfied. What helped the most was the follow-up system after the introduction. Since it was our first experience using a scheduler, there were inevitably things we didn't understand. It was a pressing issue for the shop floor, and the integrator responded quickly, which was very helpful. With accurate instructions through email and phone, we were able to resolve issues immediately."
Seeing the effects of introducing FLEXSCHE and the quick response of the integrator, Hamamatsu Photonics is currently positively considering the introduction of FLEXSCHE in the Electron Tube Division, and the same is being considered in the Second Manufacturing Group of the System Manufacturing Department of the System Division.
"The immediate goal is to enable multiple employees to handle scheduling, which is currently done by one person, and to learn the unused functions. FLEXSCHE has already become integrated into our daily operations. We want to make the most of it and work on further improvements."
Voices of Integrators
Due to the high flexibility of FLEXSCHE, there are various cases of implementation, but in this case, the extensive customization requests were characteristic. Since we had been in contact since the consideration stage, I thought that directly communicating with FLEXSCHE might not always be effective, so I acted as an interface, skillfully translating the indescribable parts to convey them to FLEXSCHE, ensuring that the desired features were accurately incorporated.
Even after the introduction, there were many inquiries, but to minimize the issue of physical distance, we addressed problem-solving by sending images and viewing the same screen together. I am very pleased that they seem satisfied. We will continue to respond promptly to questions and provide support as much as possible.
Customer Information
Hamamatsu Photonics K.K.
Head Office | 325-6 Sunayama-cho, Hamamatsu City, Shizuoka Prefecture, Nippon Life Hamamatsu Ekimae Building |
---|---|
Mikata Manufacturing | 1-8-3 Shintoda, Hamamatsu City, Shizuoka Prefecture |
Joko Manufacturing | 812 Joko-cho, Hamamatsu City, Shizuoka Prefecture |
URL | |
Established | Showa 28 (1953) |
Business Description | Manufacturing of photomultiplier tubes, image tubes, light sources, optical semiconductors, image processing and measurement equipment, etc. |
Sales | 70,466 million yen (Fiscal Year ending September 2004) consolidated |
Listed | TSE First Section |
Number of Employees | 2,249 employees (excluding part-timers, overseas assignees, etc.) |
Features | Boasts a 60% global market share in photomultiplier tubes. The photomultiplier tubes for "Super-Kamiokande" are famous. |