Realized leveling of workload through the introduction of FLEXSCHE
Reduced lead time by approximately 40 days, and reduced the volume of early delivered materials to one-sixth
Kawasaki Heavy Industries, Ltd. Vehicles
- Produced in April 2012
- Download PDF for Display
- Download PDF for Printing
Kawasaki Heavy Industries, Ltd. (hereinafter referred to as Kawasaki Heavy Industries), a world-leading comprehensive engineering manufacturer that operates businesses worldwide from land, sea, air, and even space to the deep sea. The company is also a top manufacturer of railway vehicles in Japan, producing various vehicles such as Shinkansen, conventional lines, express trains, subway trains, locomotives, and monorails for both domestic and international markets.
The railway vehicle business, which has a wealth of achievements and advanced technological capabilities, faces important challenges of production efficiency and cost reduction amid increasing competition in recent years. The Bogie Section of the Production Headquarters of the Vehicle Company responds to overlapping orders due to timetable revisions by pre-manufacturing. However, in reality, it is difficult to determine the timing to start manufacturing, leading to unnecessarily extended manufacturing lead times and earlier material procurement. To level the workload and make appropriate planning, the production scheduler FLEXSCHE was introduced.
By focusing on bottleneck processes in work planning, the manufacturing lead time was reduced by approximately 40 days, and the inventory level of materials was reduced to one-sixth. By integrating FLEXSCHE into the newly constructed production system, improvements are being made to receive purchased items such as motors at the appropriate timing.
Railway vehicle business with over a century of history
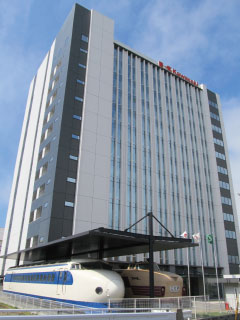
Kawasaki Heavy Industries, Ltd.
Hyogo Plant Vehicle Main Building
Kawasaki Heavy Industries, a leading comprehensive engineering company in Japan, started with the shipbuilding business in 1896 (Meiji 29). Currently, under the group mission "Global Kawasaki," which contributes to the rich lives of people worldwide and the future of the global environment, the company contributes to the development of Japan and countries around the world in a wide range of business areas, from shipbuilding, railway vehicles, aircraft, motorcycles to energy and environmental plants, and industrial robots.
Among the company's products, the railway vehicle business, which started in 1906 (Meiji 39), has a history of over a century along with the shipbuilding business. The company has manufactured many famous vehicles that remain in railway history, such as the first domestically produced steam locomotive and Japan's first aluminum vehicle, solidifying its position as the top manufacturer of vehicle manufacturing in Japan.
Furthermore, from participation in the development and design of Shinkansen vehicles to express trains, subway trains, freight cars, locomotives, monorails, and new urban transportation, the company's vehicle manufacturing is the very progress of railway transportation development. Currently, in addition to the Hyogo Plant (Kobe City), which is the mother factory, the company has two full-scale factories in the United States and operates businesses in countries around the world, including the UK, China, Southeast Asia, and Latin American countries.
The company's railway vehicle business continues to advance, but it is not easy to win in the increasingly competitive environment. The company's strengths lie in the advanced technological capabilities and development capabilities cultivated through a wealth of achievements. Another strength is the ability to comprehensively deliver the basic components of railway vehicles, the body, and the bogie. The bogie is a mechanism that holds the wheelset assembled with wheels and axles, transmits the weight of the body to the axles, and is equipped with running and control functions, supporting the safety and comfort of railway vehicles. The company's bogies also utilize the know-how and technology cultivated over many years.
Excessive inventory due to early material delivery for pre-manufacturing is a challenge
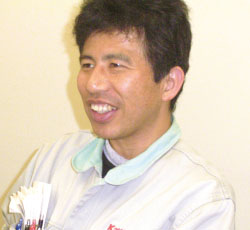
Vehicle Company Production Headquarters
Manufacturing Department Bogie Section Manager
(Currently Core Position in Production Headquarters Production Technology Department)
Mr. Akihiko Nishihara
From a competitiveness perspective, cost reduction and production efficiency are important challenges. In the company's bogie manufacturing, efforts are being made to reduce material costs and improve production efficiency, but the manufacturing of bogies is close to made-to-order, and the production of many varieties in small quantities is a major factor hindering efficiency improvement.
"Bogie can be broadly classified into four types: conventional lines, Shinkansen, locomotives, and vehicles using rubber tires for new urban transportation. For example, the required braking force differs between Shinkansen and conventional lines, so the bogie parts also differ. It also changes according to overseas standards, and even for the same conventional line, the specifications and requirements differ slightly depending on the customer's maintenance work methods. When planning production, the difficulty is that in addition to many varieties in small quantities, it is made-to-order, so forecast production is not possible," says Mr. Akihiko Nishihara.
Since forecast production is not possible, pre-manufacturing is used to respond when orders overlap during timetable revision periods. "In bogie manufacturing, axles have a long lead time, so they are ordered a year in advance. If the delivery date is not strictly observed, it will also affect the timetable, so when orders overlap, we enter pre-manufacturing," says Mr. Hiroshi Yamamoto.
The company's bogie manufacturing is managed entirely in-house, from purchasing steel plates to completing the bogie, taking about four months. The process includes three weeks of cutting and bending steel plates, 1.5 months of welding, two weeks of parts installation and machining, and two weeks of assembly. Usually, mixed production of about four to five types of vehicles is carried out, as the workload differs depending on Shinkansen, conventional lines, etc.
"Due to the long lead time and pre-manufacturing, materials tend to be ordered early, leading to excessive inventory. Since the materials are large, there are also space constraints. To prevent excessive inventory, it was necessary to shorten the lead time and reduce the volume of early delivered materials," says Mr. Nishihara.
Rescheduling and flexibility are key points for adopting FLEXSCHE
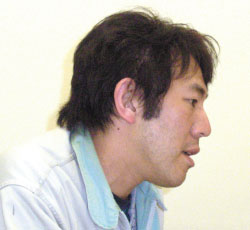
Vehicle Company Production Headquarters
Manufacturing Department Bogie Section Core Position
(Currently Project Headquarters
Asia Project Department
Core Position)
Mr. Hiroshi Yamamoto
Lead time reduction cannot be achieved unless it is considered at the time of production planning. Traditionally, site leaders such as foremen have been creating production plans based on intuition and experience, using spreadsheet software, but there was a habit of purchasing materials early and working with inventory.
"The number of parts for one cart is about 350 types, with approximately 1,000 processes per cart excluding the final assembly process, and about 300 staff members. Scheduling such a complex and vast amount of work accurately is beyond human management capabilities. Therefore, we began considering the introduction of a scheduler," said Mr. Nishihara.
After considering multiple schedulers, FLEXSCHE was adopted. Mr. Yamamoto explains the reason as follows: "In the case of the cart section, due to the production of many varieties in small quantities, various things happen on the actual manufacturing floor, and the situation changes moment by moment. For example, responding to staff who suddenly take a day off or rescheduling unfinished work for the next day. We emphasized whether it could flexibly respond to our company's actual conditions. Also, in our case, the volume of work data is enormous, and there are many changes in work, so the ability to quickly reschedule was a major point for adoption."
Lead time shortened by about 40 days, and early delivery material inventory reduced to about one-sixth
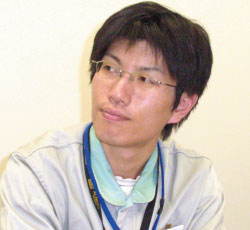
Vehicle Company Production Headquarters
Machining Department Cart Section
Hiroyuki Fujii
Around spring 2008, FLEXSCHE was introduced, and work instructions were issued based on the scheduling results, incorporating actual results to adjust the schedule. As an effect of the introduction, Mr. Yamamoto first mentioned the leveling of work load. "Using FLEXSCHE, we automatically create appropriate plans centered on bottleneck processes while leveling the work load among various facilities. The bottleneck differs for each part. Previously, it was difficult to manage bottleneck processes, leading to early starts in preceding processes and idle time in subsequent processes. With up to 300,000 operations a year after introducing FLEXSCHE, it was impossible to handle manually."
When tasks that take 10 or 20 minutes are continuous, managing bottlenecks inevitably becomes difficult. By scheduling with FLEXSCHE, it became clear at a glance when equipment was fully operational, revealing bottlenecks that were previously hard to see. "By optimally assigning with FLEXSCHE, we eliminate inefficiencies such as starting preceding processes too early or idle time in subsequent processes, achieving overall efficiency in work processes. As a result, we were able to shorten the lead time by about 40 days," says Mr. Yamamoto.
By shortening the lead time, the inventory of early delivery materials, which was a pending issue, was reduced to about one-sixth, and more than 100 square meters of space was effectively utilized. With the ability to accurately judge the situation months in advance, it became possible to request bids from subcontractors, achieving cost reduction. Moreover, unnecessary outsourcing was eliminated, and the in-house production rate improved.
Managing the production status of parts with FLEXSCHE, achieving information sharing
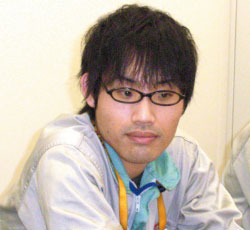
Vehicle Company Production Headquarters
Machining Department Cart Section
Hiroshi Takeshita
It took a year for the new way of working based on the scheduling with FLEXSCHE to become established on the floor. "We are scheduling down to the details that were previously left to the floor, so after the introduction, we gathered the floor staff every week for explanations and advice. We also had various discussions in response to requests from the floor. We spent a lot of time on opinion exchanges and adjustment work with the floor," says Hiroyuki Fujii.
The most common requests from the floor are the visibility and clarity of documents such as work instructions. "We extract the information needed on the floor from FLEXSCHE. Not only work instructions but also documents for follow-up in process meetings for parts that could not be completed, slips exchanged between processes, delivery instructions and management tables for material delivery, and various others," says Hiroshi Takeshita. Regarding progress management, "Just looking at a single task doesn't tell you if the process is on time. Now, we collect information from the floor and make progress management information visible on a single sheet, allowing us to accurately grasp the situation. The fact that all stakeholders can share this information is also a significant advantage," points out Mr. Fujii.
Mr. Takeshita says that as they became more proficient with FLEXSCHE, operations gradually improved.
"As the master data and work results created in the past accumulate, we have become able to efficiently create new data using them. Also, by gradually improving the scheduling rules, we have shortened the rescheduling time to one-fifth. We will continue to strive for various innovations and look forward to further performance improvements of FLEXSCHE.
Operating with mutual understanding between planners and the floor
Currently, FLEXSCHE has become established on the floor and is an indispensable presence. "The mindset has changed from feeling 'forced to do it' to 'let's use it well ourselves.' There is also an aspect of progressing with improvements on the floor," says Mr. Fujii.
Regarding the success points of introducing FLEXSCHE, Mr. Yamamoto explains, "Generally, the introduction of a production scheduler often involves the management department, but this time, I believe it was successful because the cart section introduced it themselves. The person scheduling is also in charge of the manufacturing floor and communicates with the floor staff daily. It is operated based on mutual understanding between the planner and the executor."
Regarding future prospects, Mr. Yamamoto says, "Currently, delivery instructions based on FLEXSCHE's scheduling results are only for materials, but we would like to expand the target to purchased parts such as motors through the collaboration of our production system and FLEXSCHE. This will make it possible to deliver purchased parts at the appropriate timing. Also, we are currently only collecting data on work completion, but by adding start data, we aim to improve the accuracy of scheduling."
Furthermore, Mr. Nishihara states the following about future challenges: "In the operation of the scheduler, data maintenance is important. Currently, only specific people operate FLEXSCHE, but we would like to increase the number of people proficient in FLEXSCHE in the future."
Railways play a central role in the transportation network of countries around the world. Kawasaki Heavy Industries Rolling Stock Company responds to the needs of the times and society by leveraging the abundant achievements and know-how accumulated over more than a century. FLEXSCHE plays a part in its production planning.
Overview of the implementing company
Kawasaki Heavy Industries, Ltd.
Established | 1896 (Meiji 29) |
---|---|
Capital | 104.3 billion yen |
Business Description | Manufacture and sale of ships, railway vehicles, aircraft, space equipment, jet engines, various energy facilities, various marine machinery, steel structures, various plants, motorcycles, leisure-related equipment, various hydraulic equipment, industrial robots, etc. |
Rolling Stock Company | As a top manufacturer of railway vehicles in Japan, it delivers various vehicles such as Shinkansen, trains, passenger cars, freight cars, locomotives, diesel locomotives, and new transportation systems to the world. In addition to the Hyogo Plant (Kobe City), which is the mother factory, it also has two factories in the United States. |
URL |