An indispensable scheduler even for companies in the materials and raw materials sector
Achieving detailed scheduling in multiple stages
Emulsion Technology Co., Ltd.Chemistry
- Created in September 2005
- Download PDF for Display
- Download PDF for Printing
Emulsion Technology Co., Ltd., a group company of JSR Corporation, focuses on the emulsion business, including adhesives and sealants, and the fine business as its two main pillars. Although it is a so-called "materials and raw materials" company, it introduced a scheduler eight years ago and aimed to implement FLEXSCHE when reconstructing the system a year and a half ago.
Compared to "assembly manufacturing" with many processes, companies in the "materials and raw materials" sector are said to have fewer processes. Why did they quickly introduce a scheduler, and why did they choose FLEXSCHE? We asked Mr. Fujieda Hisashi and Mr. Sato Katsuhiko.
Vast amounts of time spent on handwritten scheduling
JSR Corporation, which has over 30 group companies, has Emulsion Technology Co., Ltd. responsible for the emulsion business within the group. Founded in 1963, it manufactures petrochemical materials such as adhesives, sealants, coating materials, and cement admixtures, used in construction and civil engineering materials, carpet backing, and tile and flooring adhesives. Since its founding, it has been engaged in the emulsion business, but recently it has also entered the fine business, aiming for business expansion.
The business locations are in Yokkaichi, Tokyo, Osaka, and Nagoya, but FLEXSCHE was introduced at the "Head Office/Yokkaichi Plant" in Yokkaichi City, Mie Prefecture. Of the 181 employees in ETEC as a whole, 148 work at this business location, which forms the core of the company.
"Our company has been actively working on systematizing production management operations from an early stage, and when we built a production management system using PCs eight years ago, we considered introducing a scheduler as part of that effort. The planning was quite primitive, with site leaders writing schedules on paper calendars and copying them for raw material orders. Despite not having many processes, a vast amount of time was spent on planning because of the numerous complex conditions beyond the processes."
Scheduler introduced eight years ago
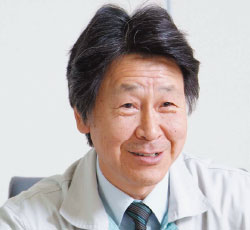
Deputy General Manager of the Management Department
Management Group Leader
Mr. Fujieda Hisashi
Both the emulsion business and the fine business consist of two processes: "manufacturing" and "filling." The "filling" process involves filling containers such as cans and drums with products made in the "manufacturing" process.
"There are two types of processes, but within them, there are various factors that complicate the constraints. One is that despite the company's size, there are many businesses, with six major product types such as 'textile processing materials,' 'chemical products,' and 'waterproof materials,' and six factories on the same premises. It would be straightforward if each factory produced one product, but sometimes a single factory manufactures multiple products. The second factor is the large number of tanks. There are 50 tanks, each with different production capacities and volumes, so there are various constraints, such as restrictions on which tanks can be used depending on the product being made, that must be considered when scheduling." In addition to these constraints, the delivery deadlines further complicated the scheduling.
"When it comes to materials and raw materials, there might be an image of having leeway in delivery deadlines, but in our case, the deadlines are short. For example, in the construction and civil engineering materials sector, there are cases where products are manufactured and delivered immediately, and sometimes there are orders like 'deliver immediately as it will be used in construction.' Moreover, many users plan production close to just-in-time, and to meet such needs, the average delivery time is 3 to 4 days, and in some cases, it can be the day after the order. Therefore, even after planning, the plan had to be revised multiple times, and manual scheduling was not feasible."
As a result, eight years ago, we introduced a scheduling package software (scheduler). With the ability to automate scheduling, the time required for planning was significantly reduced.
"However, if you ask whether we were satisfied with the functionality, in reality, we were not quite there. Initially, we planned to schedule in multiple stages, but as multi-stage scheduling made the master settings extremely complex, we ended up scheduling in a single stage. However, with a single stage, there were instances where 15 to 18 batches were assigned to a capacity meant for only 10 batches, necessitating frequent manual adjustments to make the schedule usable. This task consumed a lot of time, and reducing manual corrections has been a long-standing challenge." About two years ago, we decided to rebuild our core system, and as part of this, the scheduler was also reviewed.
A scheduler that can "achieve the seemingly impossible"
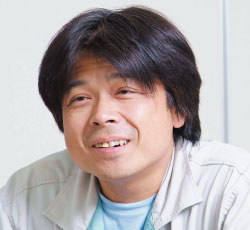
Management Group Manager, Management Department
Mr. Katsuhiko Sato
When constructing a full-scale production management system, we entrusted the selection of software to the company responsible for maintenance and asked them to build the system as an integrator.
"Even though we entrusted it, we had our own requests. The first was, of course, that it should have better functionality than the previous scheduler. The second was cost; if it fit within the budget, we were open to having a scheduler built from scratch. The third was the ability to perform multi-stage scheduling, which was a challenge, and to reduce manual corrections." The answer provided by the integrator was FLEXSCHE. It met the essential conditions, such as enabling multi-stage scheduling, but another major deciding factor was its flexibility and ease of customization.
"When I asked why FLEXSCHE, the response was 'it excels in flexibility and is easy to customize.' As I mentioned earlier, our company deals with materials and raw materials, yet we have many tanks and produce different products in the same factory, which involves many complex conditions. To incorporate these as functions, there are limits to ordinary package software. Even if we introduced a scheduler, it would be meaningless if it couldn't meet our demands. We needed a scheduler that could 'achieve the seemingly impossible,' and FLEXSCHE's flexibility and ease of customization became the deciding factors in software selection."
Mr. Sato became the de facto leader, selecting system committee members from each department, and the examination of the production management system began. Mr. Sato gathered input from on-site managers to create a scheduler that was aligned with the field. Among the things he wanted to incorporate was reflecting the differences in filling time based on the type of container (packaging).
"There are three main types of containers: 'cans,' 'drums,' and 'lorries.' Cans have a small capacity, so the filling efficiency is poor, and the filling time per certain quantity is longer. On the other hand, lorries are large-capacity containers, so they can be filled efficiently. Thus, when filling a certain quantity, the filling time changes depending on the type of container. I wondered if this could be expressed in the scheduler." This was addressed using FLEXSCHE's standard functions by devising how to handle the master.
Another feature we aimed to implement with FLEXSCHE was the ability to select tanks based on the order quantity. "Some tanks have blades for stirring products, and the production capacity is determined by the position of these blades. For example, a 10-ton tank with blades positioned at the top cannot handle a 2-ton quantity because the blades are too high to stir. Orders vary, such as 3 tons or 10 tons, so it is necessary to select a tank suitable for the order. Additionally, some tanks have two blades positioned vertically, so it was also required to set two production capacities to accommodate this."
When this request was conveyed to the integrator, they collaborated with FLEXSCHE Corporation to fully utilize its flexibility and successfully incorporated it. "There were other issues that were difficult to resolve, but the president of FLEXSCHE Corporation personally visited our company twice and provided detailed and careful support, allowing us to resolve them quickly. I was amazed by their promptness."
The biggest issue, multi-stage scheduling, was also addressed by dividing it into two stages, "manufacturing" and "filling," and for some complex cases, into four stages, which could be handled with standard functions.
The high level of flexibility that allows for expression at a detailed level raises expectations for the future.
FLEXSCHE began operation in February 2005, marking a significant change in E-Tech's scheduling. "The most significant change was the ability to express at a very detailed level on the Gantt chart. Previously, the level of expression was limited, but with FLEXSCHE, it became possible to express the amount of raw materials to be put into tanks, the required time for each process such as manufacturing and filling. With the ability to set in minute increments, it became possible to move from rough planning to accurate and efficient scheduling." Additionally, there is something that was "more convenient than expected" when using it: the color coding on the chart.
"In addition to made-to-order products, our company also has forecast production products with standard inventory in the production plan, so we had the colors for 'made-to-order products' and 'forecast production products' differentiated on the Gantt chart for easy identification. As a result, the production plans for high-priority products became immediately apparent, reducing the need for adjustments during scheduling, which has been very helpful." The biggest challenge, the time spent on manual corrections, has "reduced by 10 to 20%," he says.
"I believe there is still room for improvement in this area. The staff has become accustomed to manually correcting plans, and there is some unfamiliarity with the new production management system, so it is not yet being operated efficiently. Since it has only been recently introduced, we plan to enhance the system's functionality with the help of the integrator and FLEXSCHE Corporation, while also improving operations within our company to make it even better."
Since eight years ago, E-Tech has been quick to adopt the latest systems, such as implementing a scheduler, and remains eager for future reforms. As a result, their expectations and demands from FLEXSCHE Corporation are significant.
"When scheduling doesn't go well, if the reason could be displayed on the screen, it would help us know what to do next. I hope this can be added as a new feature. What we expect is the potential of FLEXSCHE. As we continue to advance our business reforms, various demands and requests will naturally arise from our company. At that time, there may be cases where a regular scheduler cannot handle them. However, FLEXSCHE has a high level of flexibility that other schedulers do not have. In that sense, we expect that even our unreasonable requests that may arise in the future will surely be fulfilled."
Voices of Integrators
When we were fully entrusted by E-Tech with the selection of a scheduler, we spent a long time deliberating internally. E-Tech has been working on advanced production management systems from early on, and their requirements were very high, so we searched for a scheduler that could meet those demands. It was during this process that we encountered FLEXSCHE. Of course, fulfilling E-Tech's requests was a priority, but what we highly valued was the ease of customization and the ability to easily maintain and manage it in-house.
E-Tech's manufacturing process does not have many steps, but it has complex constraints, so we were deeply concerned about how to achieve this, making numerous detailed adjustments to enhance the completeness. When we faced major challenges during this process, we sought support from FLEXSCHE Corporation, and they responded promptly, which was very helpful.
In this development, we were able to realize almost all the initially planned features, but we believe there is still room for improvement in E-Tech's production planning system centered around FLEXSCHE. We hope to work together with E-Tech to further improve the system and contribute to the efficiency of E-Tech's operations.
Overview of the implementing company
Emulsion Technology Co., Ltd.
Head Office | 1-6-16 Ohirata, Yokkaichi City, Mie Prefecture |
---|---|
URL | http://www.etec.jsr.co.jp/ |
Established | Showa 38 (1963) |
Business Description | Manufacture and sale of construction and civil engineering materials, industrial materials using synthetic rubber latex and acrylic emulsion as main raw materials, and manufacture and sale of acrylic emulsion, fine products, etc. |
Sales | 9.7 billion yen (Fiscal Year ending March 2005) |
Number of Employees | 181 employees (as of June 2005) |
Features | 100% investment by JSR Corporation. Started the fine business in 2004, becoming a two-pillar business along with the emulsion business. |