Lead time reduction, small lot production,
Inventory reduction achieved through frequent planning
To handle vast and detailed data, sequential introduction to all 7 factories
KMEW Co., Ltd. Building Materials
- Created in January 2010
- Download PDF for Display
- Download PDF for Printing
KMEW Co., Ltd., a leading Japanese manufacturer specializing in residential exterior building materials.
The company's technical capabilities in specialized fields such as roofing and exterior wall materials are highly evaluated, and along with the total support capability of the entire exterior business, including the sale of rain gutters, it is a significant strength. The company's exterior wall materials account for nearly 40% of the national market share, with the Kitakyushu factory manufacturing about half of them. In addition to commercial products distributed through wholesalers and retailers, there are also many orders from major housing manufacturers, operating multiple lines to respond. Furthermore, to meet the short delivery times required by customers, it was necessary to keep a large inventory for the highly demanded metropolitan area.
However, in an increasingly challenging business environment, large inventories become a factor that pressures management. The company is working to achieve small lot production and aims to shorten lead times to reduce inventory while maintaining short delivery times that satisfy customers. In implementing these initiatives, it became necessary to speed up process planning from monthly to weekly and daily, making it difficult to respond with manual planning as before. Therefore, FLEXSCHE was adopted with the aim of systematizing process planning. After its introduction at the Kitakyushu factory, it was expanded to all of the company's factories.
In an increasingly challenging business environment, solving inventory problems is an urgent task.
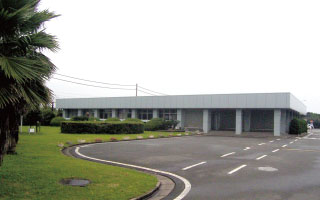
KMEW Co., Ltd.
KMEW Co., Ltd., a top brand manufacturer of residential exterior building materials. The company was established in December 2003 through the business integration of the housing materials businesses of Kubota Corporation and Panasonic Electric Works Co., Ltd. (formerly Matsushita Electric Works). It provides indispensable total solutions for home exteriors, from the development, manufacturing, and sales of roofing and exterior wall materials to the sale of rain gutters, and its technical capabilities in each specialized field are highly evaluated.
As stated in the corporate slogan "Protecting life, showcasing homes," the company's strengths lie in its consideration for the environment and safety, as well as its design capabilities that richly color life.
For example, the seismic reduction tile "ROOGA," a new material that is thick yet light, beautiful yet strong, and the groundbreaking exterior wall material "Hikari Cera," which features "self-cleaning function" and "air purification function" through photocatalysis, are examples. As part of their environmental initiatives, they are also focusing on technology to render asbestos-containing building materials harmless. Additionally, they are making efforts to use recycled materials as much as possible in consumable materials and to collect their company's scrap materials generated at new construction sites nationwide. As responding to a resource-circulating society becomes increasingly important, the company's technological capabilities and high-value-added products are expanding their opportunities significantly.
The company, which has reached a sales scale of 100 billion yen and continues to grow steadily, faced an urgent need to solve inventory issues amid an increasingly challenging business environment.
A company-wide project was launched to establish a flexible production system.
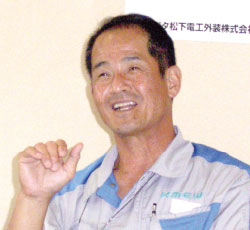
Deputy Manager of the Exterior Wall Material Business
Kitakyushu Plant Manager, Executive Officer
Toshifumi Tsubokura
Kitakyushu City, which has flourished in heavy chemical industries since ancient times, continues to attract companies from various fields. In this city, surrounded by abundant nature, is the Kitakyushu Plant responsible for KMEW's exterior wall material manufacturing. The Kitakyushu Plant has an exterior wall material production capacity of "500,000 tsubo/about 165,000 square meters," which accounts for about half of the company's exterior wall material production. The company currently holds nearly a 40% share in the exterior wall material field, indicating the significant scale of the Kitakyushu Plant.
The Kitakyushu Plant manufactures a product called "Excelage" in the exterior wall material category. "Excelage" comes in three types: organic coating, hydrophilic ceramic coat, and photocatalytic coating. The products handled by this plant include over 400 commercial items distributed through wholesalers and retailers, as well as custom orders from major housing manufacturers.
"To respond to customer orders with short delivery times, it was necessary to store a large inventory in the metropolitan area where demand is high. However, a large inventory significantly pressures management. While fulfilling our mission as a manufacturer, how can we reduce inventory? One ideal is a style of quickly replenishing and producing sold products," says Toshifumi Tsubokura, Deputy Manager of KMEW's Exterior Wall Material Business and Kitakyushu Plant Manager.
Since exterior wall materials have large packaging sizes and high storage costs, the effect of shortening lead times is immeasurable from that perspective as well. In 2005, a company-wide project was launched to establish a flexible production system. The project promoted on-site reforms aimed at shortening lead times for manufacturing, procurement, and planning, and advanced the transition to multi-product small-lot production.
Planning to respond to a flexible production system is impossible by hand.
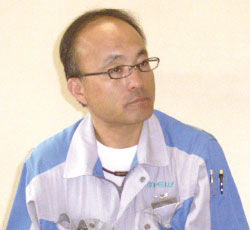
Kitakyushu Plant (currently Kashima Plant)
Business Group Leader
Yoshifumi Yamaguchi
The company also implemented on-site improvements to shorten changeover times and provided training for creating process charts tailored to a flexible production system. The goal was to shorten the planning cycle from once a month to weekly and daily, making manual planning creation no longer feasible. For example, the Kitakyushu Plant faced various challenges regarding planning.
- Once a month, three staff members manually created process charts over three days.
- There was a strong dependency on individuals, making it difficult to pass on know-how.
- Complex conditions increased the burden on staff.
- They were constantly dealing with repeated process changes, leaving no room to consider operational efficiency.
- Since people were gathering necessary information for planning by looking at various documents and screens, there was a lot of wasted time.
- Since it was handwritten, making corrections was difficult.
Yoshifumi Yamaguchi, the Business Group Leader at the Kitakyushu Plant, talks about the challenges of planning operations at the plant. "We have to create plans while keeping in mind various constraints in product manufacturing, such as the vast number of products, the time it takes for cement to set, and slight differences in thickness, as well as the current state of inventory and sales trends. Additionally, to respond to repeated process changes, we fully utilized multiple lines, and it was a significant burden for planners to combine them while timing them, such as making these colors together to reduce losses. Therefore, the number of members who could create process plans was limited."
To solve various planning-related issues, FLEXSCHE was introduced.
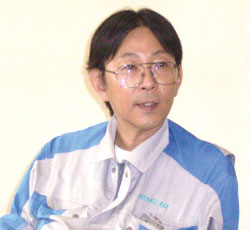
Kitakyushu Plant Business Group
Section Manager Yasuhiko Komi
As mentioned earlier, systematizing process planning was essential. In 2005, Kazuo Tomita, who was the contact for system-related matters at the time (currently Section Manager of the Strategic Planning Office for the Exterior Wall Material Business), consulted with Kubota System Development Co., Ltd. (hereinafter referred to as KSI), a group company. The proposal received was FLEXSCHE.
"I had previously been involved in creating a prototype using FLEXSCHE and had the impression that it could be used for our operations. Additionally, I had high expectations for KSI's support and decided to adopt FLEXSCHE."
KSI, with its experience in system construction and operation within the Kubota Group, provides manufacturing solutions to a wide range of customers and is also a business partner of FLEXSCHE.
The company first introduced FLEXSCHE at the Kitakyushu Plant. "The point emphasized at that time was the ease of use for on-site personnel. We built a unique user interface so that anyone could use it without specialized knowledge and to respond meticulously to on-site needs. For example, to avoid major troubles such as stockouts or inventory imbalances when handing over to a new person in charge, we included functions such as ranking products close to stockout on the screen. In terms of usability, we made it easy for staff to filter by sales trends and mold types," explains Tomita.
To plan with fewer changeovers, information such as pattern grouping and series grouping can also be included. "I talked with the site, gathered needs, and asked KSI if we could do this and that. I am truly grateful for their meticulous support," Tomita appreciates KSI's support capabilities.
Two years ago, with the reconstruction of the order-receiving system, inventory data was automatically linked to FLEXSCHE in real-time, and the process plans created with FLEXSCHE were automatically sent to the order-receiving system. As a result, reports were output as process charts on-site, leading to delivery date responses.
Both the efficiency and quality of planning operations have significantly improved.
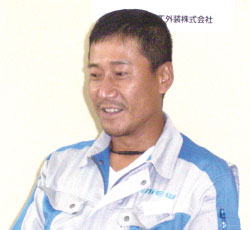
Kitakyushu Plant Business Group
Masami Ishikawa
The introduction of FLEXSCHE dramatically changed the planning work of the production process. Regarding the differences from the past, Yasuhiko Komi, Section Manager of the Kitakyushu Plant Business Group, says, "Even when there are troubles or changes, we manage to cope by fully utilizing multiple lines and adjusting what can be commonly processed. At that time, we had to adjust all related lines, which was difficult to do in our heads and carried the risk of oversight. Now, we can see the overall situation on the screen, allowing for instant decision-making."
Masami Ishikawa of the Kitakyushu Plant Business Group talks about the difficulties of handwriting. "When there were changes, there was a limit to issuing instructions, and we had to erase and rewrite with tears in our eyes."
The approach to planning operations has also changed. "Previously, we would mentally calculate and adjust time, wondering what would happen if we moved things forward because there were a few hours free, or if we should revert to the original plan. Now, we can easily swap and check using the simulation function with drag and drop. We used to fix conditions to some extent, but now we have shifted to an approach where we explore more optimal methods before making plans," says Mr. Ishikawa.
The efficiency of planning operations has also significantly improved. Previously, planning was divided into three processes: pre-process 1, pre-process 2, and finishing, with three people involved. Now, two people are consistently responsible from the pre-process to the finishing. "The first thing I do when I come to the company is launch FLEXSCHE. I use it every day for checking the current status and daily adjustments. We conduct planning based on new information twice a week," says Mr. Komi.
The quality of time spent on planning has also changed. "Previously, we would first obtain information from the screen for each product number and transfer inventory and sales data to Excel. This process took time. Additionally, calculating time when swapping required using a calculator, which added a significant workload during the planning preparation stage. Now, we can allocate time to consider what should be prioritized, such as the most efficient production order. Even when we need to reconsider due to changes in order conditions or situations, we can easily change plans," says Mr. Ishikawa.
After its introduction at the Kitakyushu plant, it was deployed to all seven of the company's plants.
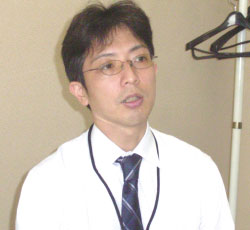
Exterior Wall Material Business Strategy Planning Office
Section Manager Kazuo Tomita
After FLEXSCHE was introduced at the Kitakyushu plant, it was deployed to all of the company's plants. Each plant has different products, manufacturing methods, and processes, and new functions and interface improvements have been made to suit the characteristics of each plant.
"After the introduction, the planning personnel changed at five plants, but the transition was smooth, and there were no major issues. The process charts are ingrained at each site, so we asked KSI to tailor the interface to the actual conditions of the plants. From the perspective of the plant sites, there should be no impression that the system has changed," says Mr. Tomita.
There are also expectations for effects in terms of inventory reduction. Kitakyushu Plant Manager Mr. Tsubokura states, "If the quality of planning improves, production efficiency will also improve. Additionally, if plans can be formulated quickly, materials can be ordered earlier, leading to an overall reduction in lead time. By changing the planning from once a month to twice a week, it has become possible to incorporate changes in the situation more timely while scrutinizing sold products. We expect that by further improving accuracy, we will contribute even more to inventory reduction in the future."
For the company, which is working on lead time reduction and small-lot production to reduce inventory, FLEXSCHE has become an indispensable presence.
Partner's Voice
For me, the project with FLEXSCHE at the KMEW Kitakyushu plant was the first. Initially, I struggled to meet the on-site requests as my knowledge of FLEXSCHE was not very deep. I believe there were areas where I fell short for the staff at the Kitakyushu plant, but I am grateful for their patience and cooperation.
In addition to the introduction of the package, we also assisted with the development of interfaces and reports, as well as the operation manuals for the business, allowing us to accumulate know-how to establish FLEXSCHE on-site. Taking the first step at the Kitakyushu plant made it possible to expand to other KMEW plants. I believe that the reason FLEXSCHE has been used continuously for a long time since its introduction is that we were able to realize Mr. Tomita's concept of making it usable by anyone without specialized knowledge. Four years have passed since its introduction in 2005, and the version of FLEXSCHE has been upgraded, and there are also functions added at other plants. We hope to make new proposals to the Kitakyushu plant and contribute to further efficiency improvements.
Overview of the implementing company
KMEW Co., Ltd.
Head Office | Crystal Tower 13F, 1-2-27 Shiromi, Chuo-ku, Osaka |
---|---|
Established | December 1, 2003 |
Capital | 8 billion yen |
Number of Employees | 1,786 employees (as of April 1, 2010) |
Business Description | Manufacture and sale of roofing and exterior wall materials. Sale of rain gutters and construction and management through subsidiaries. |
Factory | Manufacturing of exterior wall and roofing materials at seven locations in Japan, including the Kitakyushu plant. |
URL |
Partner DATA
Kubota System Development Co., Ltd.
Head Office | 1-2-47 Shikitsuhigashi, Naniwa-ku, Osaka |
---|---|
URL |