Using FLEXSCHE for over 10 years
Leading in high-mix low-volume production
- Produced in September 2019
- Download PDF for Display
- Download PDF for Printing
Chemistry
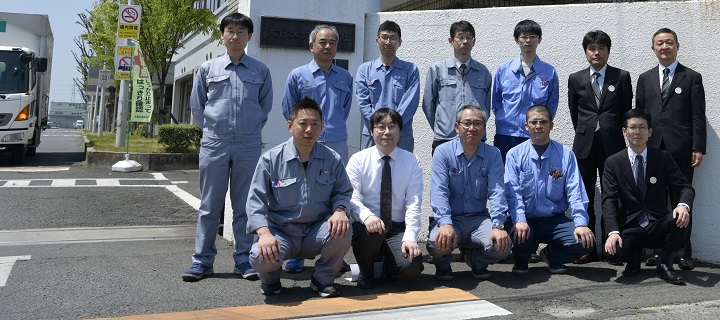
With the cooperation of the Okura Industrial Synthetic Resin Division and Okura Industrial Products Co., Ltd.,
and everyone at Mitsubishi Electric Information Systems Corporation (FLEXSCHE Business Partner)
"Responding to high-mix low-volume production"
To meet the diversifying needs of consumers in recent years, the trend towards high-mix low-volume production is strengthening in many products. The challenges that come with such changes are a common concern in any manufacturing site. At Okura Industrial Co., Ltd., which has been supplying functional film products across a wide range of industries by leveraging the technology cultivated over many years, there is a demand for flexible production capabilities. The company, which had been using a production scheduler as a measure to quickly streamline production, introduced FLEXSCHE in 2008 to achieve smoother factory operations that can reliably meet client demands.
This time, we spoke with everyone currently using FLEXSCHE about the operations from the introduction 11 years ago to the present.
A major film manufacturer catering to a wide range of industries
Okura Industrial Co., Ltd., headquartered in Marugame City, Kagawa Prefecture, was founded in 1947 and is a leading chemical manufacturer at the forefront of the industry with synthetic resin films. Although simply referred to as films, the industries and applications for these products are truly diverse. As client needs diversify and product cycles shorten, Okura Industrial, which releases numerous products with functional strengths in various fields, is highly regarded in the market.
Okura Industrial has three sections: the "Building Materials Division," which manufactures construction materials; the "New Materials Division," which provides products for the electronic information field, such as optical films used in smartphones and televisions, and the medical field; and the "Synthetic Resin Division," which we are discussing this time. The Synthetic Resin Division conducts particularly wide-ranging production, including essential daily items like plastic bags and food films, agricultural materials, and films with special functions for industrial use, and has been operating FLEXSCHE since 2008.
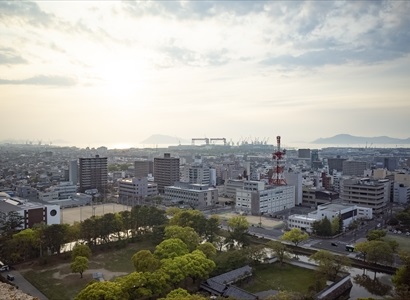
The headquarters and three factories are located in Marugame City, the second-largest city in Kagawa Prefecture.
In recent years, efforts have also been made to address environmental issues as a film manufacturer. The environmental challenges posed by plastic products, including films, are a global concern, and Okura Industrial is working on initiatives such as producing products using biomass materials, manufacturing biodegradable films, recycling used films as raw materials, and exploring new processing forms to minimize the environmental impact of film products, thereby responding to the demands of society and clients and continuously increasing the number of functional products.
Leading the way in introducing production schedulers
Okura Industrial first introduced a production scheduler 20 years ago. Before the introduction of the production scheduler, planners manually created plans. At that time, as was the case in many manufacturing sites, the planning work depended on the knowledge and skills of specific planners, leading to 'personalization of planning work,' which made it difficult to share know-how.
Additionally, Okura Industrial's production style is primarily make-to-order, and they rarely hold product inventory. Therefore, if there is a change in the client's order, the manufacturing site's plan must be changed each time. However, it was difficult to meticulously revise the plan manually each time, and as a result, additional orders were accepted without accurately assessing production capacity, leading to frequent issues such as delivery delays. Intense exchanges between the factory and sales were also commonplace. To overcome this situation and 'visualize' production status and plans, the introduction of a production scheduler was promoted.
The initial scheduling system employed a production scheduler different from FLEXSCHE. Its introduction enabled visualization of planning, enhancing the ability to respond to client demands and improving information sharing between production sites and sales, which indeed reduced troubles. However, challenges remained in terms of scheduling logic, operability, and stability. As the diversity of production items increased, the system replacement was considered to improve the efficiency of planning operations and the accuracy of plans.
In 2008, after carefully comparing multiple production schedulers, the decision was made to replace the system with FLEXSCHE.
"The new system was required to inherit all the functions of the existing system, including Okura Industries' unique features. It was confirmed that FLEXSCHE could cover all of these. Its flexibility to withstand future expansions was also attractive, and its excellent operability led to its adoption. I heard that employees accustomed to software with smooth operations like Microsoft Excel® also found it easy to use,"
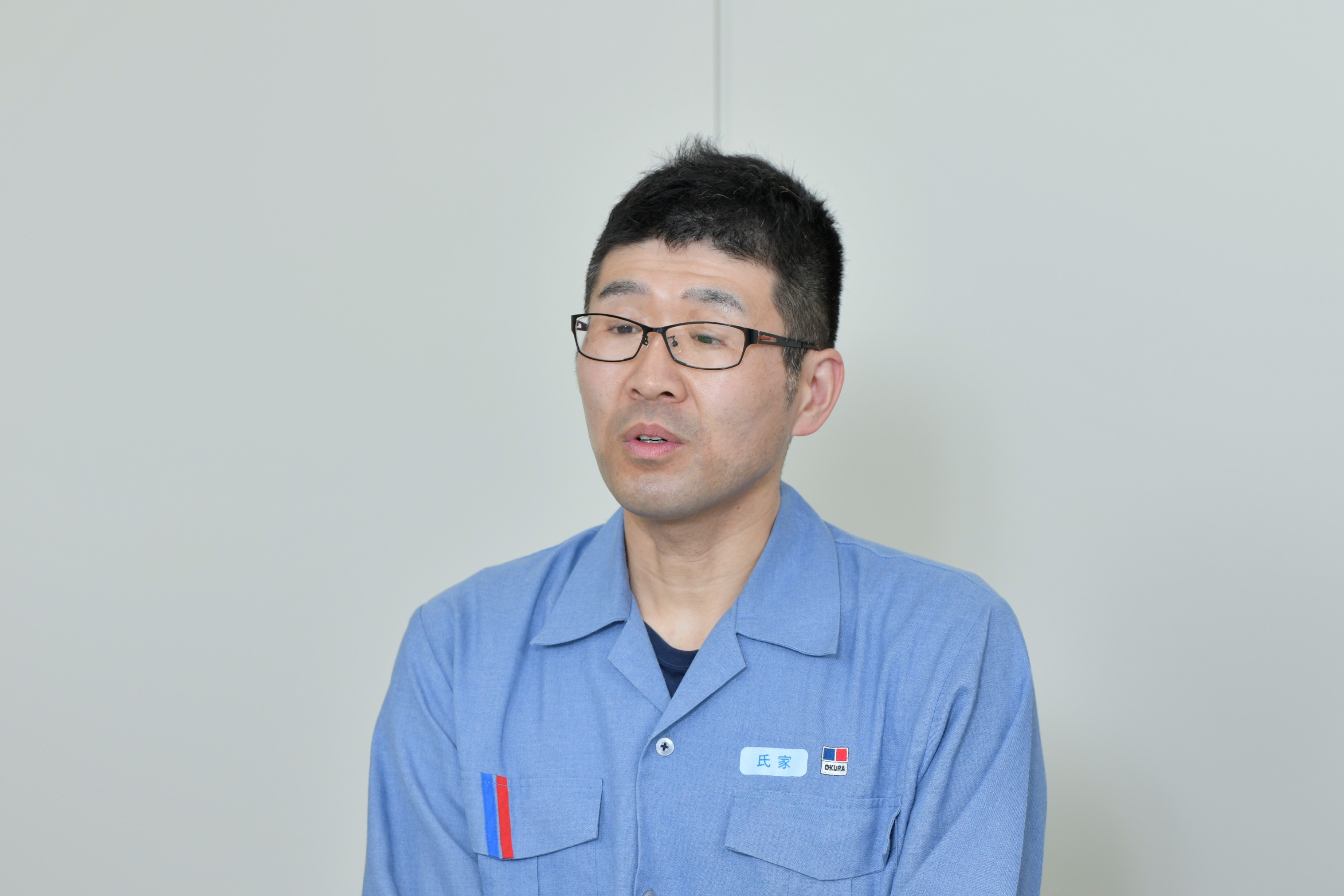
Marugame Fourth Factory Production Management Section Ujiie
Hiroshi Ujiie, the leader of the Production Management Section at Marugame Fourth Factory, who was involved in gathering opinions and designing specifications from each factory during the introduction of FLEXSCHE, shares this. At the time of introduction, since the resource information of the factory was somewhat prepared, there was an advantage in collecting basic data compared to introducing it from a state with no foundation for using a production scheduler. However, there was significant difficulty in deciding the 'Okura Industries Common Specification' that would be easy to use in any factory, given the presence of multiple factories with different production items.
"At that time, not long after joining the company, I was still lacking basic knowledge of factory operations. I felt pressure in listening to and summarizing the opinions of the field staff, who had far more knowledge and experience than I did, within a limited period."
The strategy was to implement company-wide common scheduling rules and various functions, then proceed with sequential introduction to each factory, and subsequently make changes tailored to individual circumstances, aiming to achieve operation in a short period.
"We started the introduction with the factory of 'Kansai Okura Corporation' (a group company), as the factory manager was eager to quickly reduce the burden on the planning staff. It went smoothly to operation there, but at another factory, new requests emerged at the introduction stage, requiring adjustments, and we couldn't meet the initially targeted deadline."
Although it was not an easy project, eight months after starting the introduction at Kansai Okura, the planned introduction to all factories was finally completed. Some factories have not been introduced due to their scale and production items, but currently, FLEXSCHE is operated in seven factories.
The Operation Sequence Chart is a function that expresses the Gantt chart in a list format, allowing operations such as swapping tasks, enabling smooth plan adjustments even in factories with small-lot, multi-variety production like in this case.
Additionally, at Okura Industries, where there are many small-lot orders, there were voices saying, "The processes are displayed in detail, making it difficult to swap tasks on the Gantt chart." This realization led to the development of the 'Operation Sequence Chart' as a new standard feature of FLEXSCHE. This is a list-format chart for adjusting the order of operations on each resource, allowing easy changes to the order of operations and the resources used by dragging the rows representing operations with a mouse. This feature has been well-received for making it easy to rearrange operations and change plans, and it continues to be a beloved feature at Okura Industries.
Smooth Factory Operation Brought by FLEXSCHE
Eleven years after its introduction, planners unanimously say, "We can't imagine a situation without this," and FLEXSCHE has become an indispensable system for Okura Industries.
"FLEXSCHE has made the flow of factory operations clear. It reveals obstacles to smooth production planning, such as equipment status, insufficient production capacity for orders, and labor shortages."
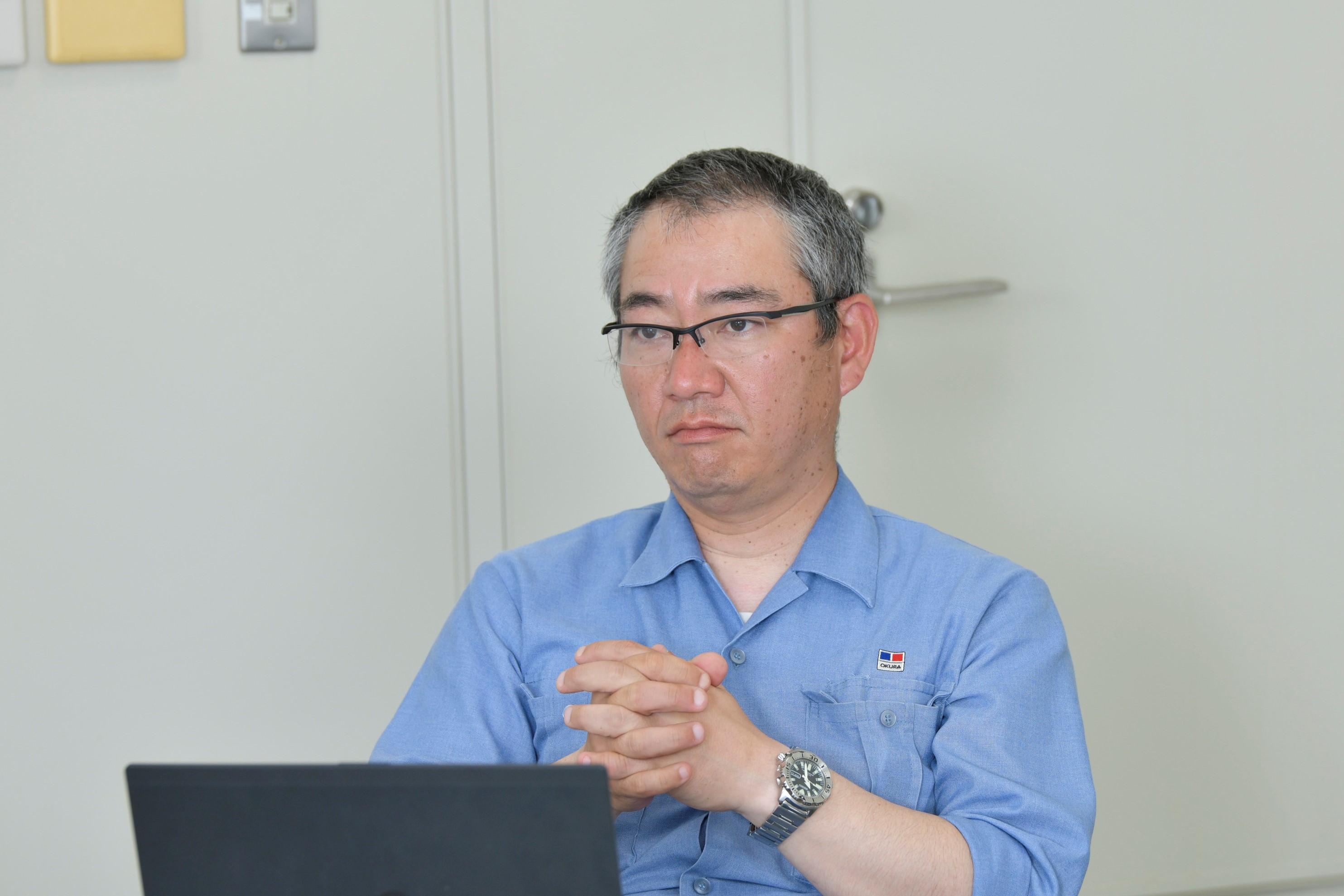
Synthetic Resin Division Production Management Group Ogita
These are the words of Hiroki Ogita, the manager of the Production Management Group in the Synthetic Resin Division. Understanding the various issues that hinder factory operations is not straightforward, but the clear visualization of these issues is one of the major benefits of a production scheduler.
"The information provided by FLEXSCHE is now used for various discussions, such as identifying the causes of troubles, finding solutions, and responding to imminent deliveries."
The scheduling results from FLEXSCHE are reflected in the core system as needed, and the sales department also checks them, utilizing them for delivery date responses and adjustments to clients.
In the production of the Synthetic Division, there are two main processes: "raw material production" and "secondary processing" such as lamination and slitting. The benefits brought by FLEXSCHE were particularly significant in raw material production. The previously vague production site plans were clearly visualized as scheduling results, down to specific work instructions, making progress management easier. The site can easily grasp the plan, facilitating the setting of maintenance schedules and the procurement of raw materials and supplies, leading to inventory reduction. In one factory, the planning work, which used to take five hours a day, was improved by 50% in efficiency, and the planning accuracy was significantly improved compared to the previous system. On the other hand, in secondary processing, the processes are too detailed to flexibly reschedule one by one, so a flexible approach is taken by combining rough scheduling with FLEXSCHE and the judgment of planners to decide and adjust production plans according to the production style.
Additionally, there are planners for each factory and process, and multiple employees operate FLEXSCHE. Over the long period of ten years, there have been changes in planners. However, the introduction of FLEXSCHE has prevented the personalization of planning work and made it easier to hand over tasks. In one factory's process, by enabling multiple employees to operate FLEXSCHE, they have realized the significant secondary effect of not having to place a heavy burden on a specific planner.
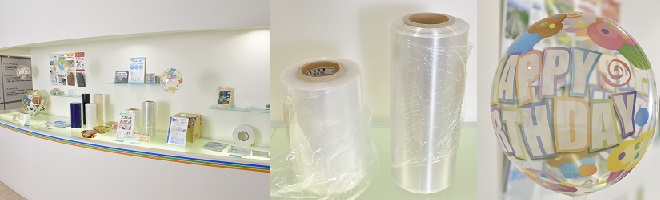
The company's product showroom displays a variety of products. They are responding to client demands and realizing functional and diverse manufacturing.
The Role of FLEXSCHE in Responding to Diverse Needs
Okura Industries updated FLEXSCHE in conjunction with the switch to Windows 7 and Windows 10. Each time, from Ver8 to Ver10, and then to Ver17, significant updates were made, but the system continued to operate stably without any noticeable changes in usability or compatibility issues between versions. Leveraging years of usage experience, new functions have been added to accommodate new production, and FLEXSCHE has grown into an indispensable system.
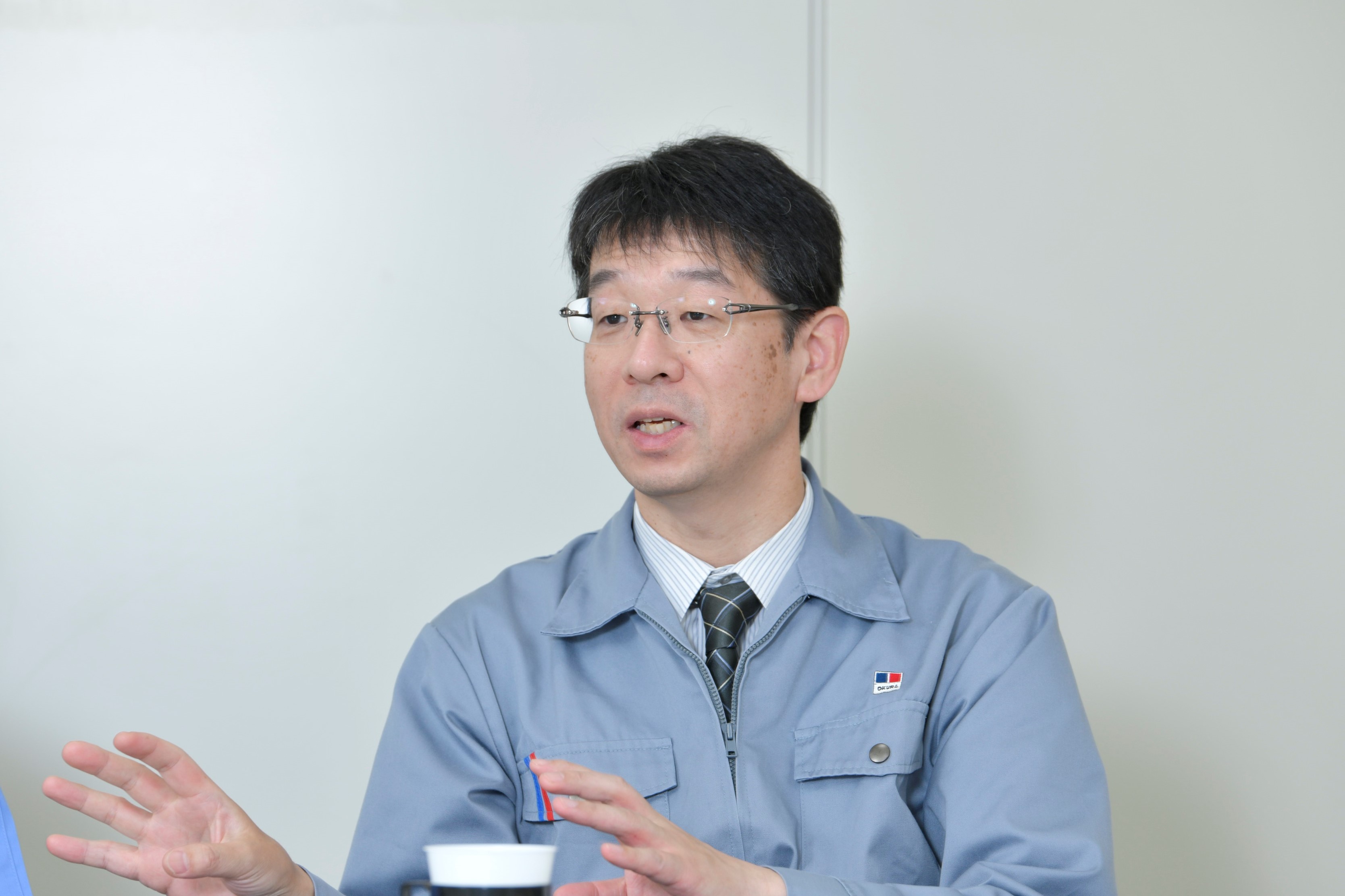
Synthetic Division Business Group Tanaka
"The trend towards small-lot, multi-variety production seems to be strengthening year by year. As product cycles have shortened, many are now produced on a made-to-order basis. For example, many items that were labeled at the customer's factory after delivery have switched to printing at our company, and it is expected that lot sizes will become even smaller and delivery times will shorten in the future," says Kenji Tanaka, Deputy General Manager of the Synthetic Division Business Group, about future prospects.
For over 10 years, FLEXSCHE has earned trust as an indispensable tool for responding to ever-changing needs. Its importance will continue to grow in preparation for increasingly complex production in the future. FLEXSCHE will always support advanced and functional manufacturing, leveraging the high technology of Okura Industrial Co., Ltd.
Voices of Integrators
Mitsubishi Electric Information Systems Corporation (FLEXSCHE Business Partner)
To achieve the purpose of replacing the scheduler, we proposed FLEXSCHE to Okura Industrial Co., Ltd., as it is highly likely to realize the required functions. During the implementation, to quickly and cost-effectively operate FLEXSCHE in multiple factories with different scheduling rule requirements, we started the project by designing a standard specification base common to each factory and proceeded by customizing that specification according to the requirements of each factory.
Since its operation, Okura Industrial Co., Ltd. has been a long-time user of FLEXSCHE. In 2018, we conducted a major version upgrade of FLEXSCHE to accommodate Windows 10. At that time, we responded to Okura Industrial Co., Ltd.'s improvement requests by adding features such as outputting operation sequence charts to reports, making it more convenient to use.
In development, we utilize add-ins to the fullest extent to maximize FLEXSCHE's capabilities, focusing on system design that emphasizes operability. We aim to continue to flexibly respond to our customers' evolving needs alongside changes in the production field.
Overview of the implementing company
Okura Industrial Co., Ltd.
Head Office Location | 1515 Nakatsu-cho, Marugame City, Kagawa Prefecture |
---|---|
Established | 1947 |
Capital | 8,619,616,017 yen |
Number of Employees | 1,164 employees (standalone), 2,053 employees (consolidated) (as of December 31, 2018) |
Business Overview | Manufacture and sale of various polyethylene and polypropylene products, manufacture and sale of optical functional films, manufacture and sale of particle boards and processed boards, etc. |
URL | https://www.okr-ind.co.jp/ |