Introducing FLEXSCHE to the key Thai factory for mass production
Achieving line leveling in post-replenishment production through collaboration with SAP,
Improving production efficiency
KITZ Corporation Industrial Machinery
- Produced in July 2014
- Download PDF for Display
- Download PDF for Printing
Japan's leading comprehensive valve manufacturer, KITZ Corporation (hereinafter referred to as KITZ). The company, which is highly regarded not only in Japan but also worldwide, established a local presence by setting up regional headquarters in its long-term management plan "KITZ Global Vision 2020" formulated in 2010, aiming to be among the world's top three in the valve business.
One of the key pillars of "KITZ Global Vision 2020" is the introduction of SAP to overseas bases to strengthen the global management foundation. The introduction to the Thai factory, which serves as a model for considering the standard operations and systems of the KITZ Group, started in 2012. To address the two challenges faced by the factory, "leveling in post-replenishment production" and "accurate and prompt delivery date response," FLEXSCHE was adopted to aim for a solution.
By introducing FLEXSCHE and SAP, which can handle not only production planning but also delivery date response requirements, the new production planning system successfully went live in 2013. This not only standardized the delivery date response operations but also synchronized the execution plan results with the field as instructions, leading to line leveling, improved production efficiency, and reduced man-hours by eliminating parts shortages. Based on the success and know-how gained, the introduction and deployment of SAP and FLEXSCHE to other bases are being considered.
Introducing SAP to overseas bases to strengthen the global management foundation
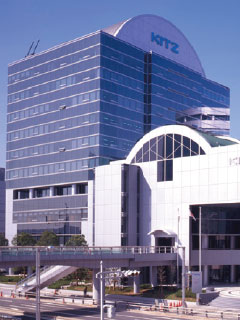
KITZ Corporation
Valves are one of the essential components for the stable supply of lifelines such as water, oil, and gas. Due to their function of controlling fluids, valves are used in a wide range of scenarios, including residential, office buildings, and oil and gas plants.
KITZ, a leading comprehensive valve manufacturer in Japan, has a product lineup of over 90,000 types with various materials, shapes, and diameters, such as bronze, brass, stainless steel, cast iron, and cast steel, responding timely to customer demands. The company's strength lies in its integrated production system, which handles all processes from casting, processing, assembly, inspection, to shipping in-house, forming the foundation to realize the corporate philosophy: "KITZ aims to continuously enhance corporate value with creative and high-quality products and services."
The company, highly regarded as "KITZ of Fluid Control" not only in Japan but also globally, is working on the long-term management plan "KITZ Global Vision 2020" to achieve further growth worldwide. It positions three regions (Europe, Americas, ASEAN) and two bases (China, India) as key global areas, establishing regional headquarters with composite functions such as sales, marketing, technology, and stock, aiming to be among the world's top three in the valve business under a regionally-focused system.
As the integration of management and IT progresses, the use of IT is indispensable in global management. As part of "KITZ Global Vision 2020," the company is implementing SAP introduction to overseas bases to strengthen the management foundation.
"The introduction of SAP began with the Chinese factory in 2009. In 2012, it was introduced to the Thai factory, the main factory for mass-produced products, and went live in 2013. The Thai factory should serve as a model for considering the standard operations and systems of the KITZ Group. Visualizing the sales/production status, sales/production results, cost results, and accounting information of the Thai factory was also an important objective to promote the creation of global common standards within the KITZ Group," says Toshio Ozawa, Director of the Information Systems Department.
Realizing leveling in post-replenishment production is an urgent issue
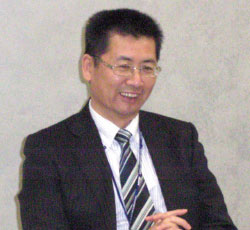
IT Management Center, Director of Information Systems Department
Toshio Ozawa
The challenge at the Thai factory was the "discrepancy in the timing of supply and replenishment" associated with post-replenishment production, which involves maintaining only the minimum necessary inventory and replenishing only what is used. To solve this issue, it is necessary to level the number of picks per day on each production line and plan to avoid overloading or underloading the lines.
"By achieving leveling in the final assembly process, it becomes possible to level the parts in the preceding processes, enabling stable production from parts processing to raw materials. How to realize the product leveling plan became an important theme," reflects Kenta Yonekura of the Production Planning Group. Additionally, since most production lines manufacture both post-replenishment and make-to-order products (mixed lines), leveling in mixed lines also became a point of focus.
The planning system necessary to realize the leveling plan was developed in-house, but there were many challenges with the conventional planning system. "The conventional planning system had many points that deviated from the actual production, requiring time and effort for manual adjustments, making it difficult to provide prompt delivery date responses to customers.
Moreover, although it was called a planning system, it only performed load accumulation simulations, and the results were not linked to production instructions, so production activities were based on the plans in the planners' minds. The know-how related to planning was dependent on individuals, and there was also the issue of know-how not being inherited," says Yonekura. Furthermore, at the Thai factory, improving production efficiency through leveling and realizing prompt delivery date responses were urgent issues. Therefore, the company decided to introduce a planning system along with SAP. The following three points were emphasized in the selection of the planning system.
1. Delivery Date Response
Realize delivery date responses backed by the factory's capabilities to customer inquiries about delivery dates. Also, by linking reservation information of delivery date responses/undecided orders with actual orders and managing the load, ensure production is carried out according to the answered delivery dates.
2. Execution Plan
Based on the orders for make-to-order items, execute production that ensures reliable parts supply and efficient setup. Also, communicate the make-to-order production plan devised in the execution plan as production instructions to the production site.
3. Picking Plan
Based on the orders for post-replenishment items, carry out withdrawals from the finished goods store to level the production of parts supplied to the product assembly and assembly processes without bias. Also, communicate the withdrawal plan devised in the picking plan as shipping picking instructions to the production site and warehouse.
Among the above three points, it was imagined that the execution plan and picking plan could be realized by renewing the planning system, but they were constantly considering what kind of system should be constructed to realize "delivery date response." "We received proposals from several companies regarding the planning system. However, regarding our requirements and demands for delivery date response, all the proposing companies responded with 'cannot do it.' Only FLEXSCHE's proposal responded with 'can do it,' which honestly surprised us. Upon investigating FLEXSCHE, which responded with 'can do it,' we realized its excellent flexibility in meeting our unique business requirements associated with post-replenishment production.
We also came to highly evaluate FLEXSCHE for its ability to be customized. The appropriate proposals from Ube Information Systems, which supports the introduction of FLEXSCHE, also encouraged its adoption," says Yonekura about the reasons for adopting FLEXSCHE. Based on his experience in developing a planning system in-house, Ozawa talks about the ease of use of FLEXSCHE: "We remember struggling to achieve intuitive operation in our in-house development, but we were greatly surprised by the high level of completion of FLEXSCHE's operability, such as the Gantt chart that allows smooth manual corrections by dragging operations to any time or resource."
To realize leveling, planning is divided into two parts: "Load Planning" and "Execution Planning."
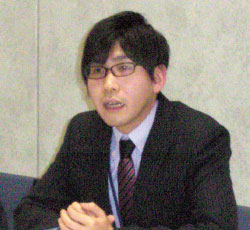
Production Planning Group
Kenta Yonekura
In this instance, the significant themes in the formulation of a leveling plan were "maximizing line capacity utilization" and "creating a feasible plan considering constraints." To address these two challenges, we decided to separate the "load planning," which realizes a delivery date response mechanism at the inquiry stage, from the "execution plan," which is developed after receiving orders. "By considering constraint conditions such as the ratio of make-to-stock and make-to-order production, daily production volume, and lead time, we formulate a load plan to prevent line overload or underload and respond to customer delivery date inquiries. After the order is confirmed, we formulate an execution plan and connect the results to shipping picking and manufacturing instructions," says Mr. Iide Seihou from the System Development Group.
In the new production planning system, delivery date inquiry data from SAP is linked to FLEXSCHE, where automatic scheduling is performed, and the results are returned to SAP. When the customer confirms the delivery date response and places a confirmed order, the order entry data from SAP is linked to FLEXSCHE, where automatic scheduling is performed, and after fine-tuning by the person in charge, production instructions are issued to SAP. (Reference: Overview of the New Production Planning System)
Since the maintenance of the new production planning system is to be carried out by the headquarters, the FLEXSCHE server is installed at the Japan headquarters, and the staff at the Thai factory operate FLEXSCHE using terminal services. The planning at the Thai factory using FLEXSCHE is done by Thai staff. They use the English manual and translate only the important parts into Thai for operation. "We took the time to thoroughly explain to the Thai staff that 'data backing is necessary even for delivery date responses.' It took a long time for them to understand due to the need for a change in mindset," says Mr. Iide.
Production efficiency improved within a few months after the new production planning system went live.
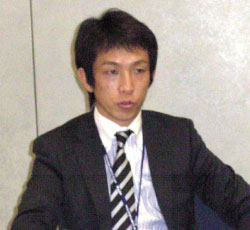
IT Management Center, Information Systems Department
System Development Group
Mr. Iide Seihou
In 2013, after the full operation of the new production planning system using FLEXSCHE at the Thai factory, the effects of the introduction became apparent. "First, the standardization of delivery date response operations. Previously, delivery date responses were made by the planning staff after considering the results of load accumulation, the extensive product lineup, various components constituting the products, and other order constraints in their minds. Currently, FLEXSCHE calculates the production completion date considering various constraints, eliminating the need for personal know-how and enabling accurate and prompt delivery date responses. By establishing rules with customers, such as defining a cancellation period for delivery date responses, we have been able to systematize scheduling, which previously relied on manpower, achieving significant operational efficiency," says Mr. Iide.
Moreover, production efficiency improved through leveling. "Three months after the new production planning system started, there was a report from the Thai factory that production volume had increased. This is due to the effect of achieving line leveling at the execution plan stage, issuing instructions from the execution plan, and being able to produce based on those instructions. The man-hours for handling abnormalities such as parts shortages have also been reduced," says Mr. Yonekura. Furthermore, the man-hours for planning operations have also been reduced. Before the introduction, four production planning staff were formulating plans, but after the introduction, one person is formulating plans for more than 30 lines and responding to delivery dates.
Regarding future developments, "Currently, delivery date responses are made twice a day for each plan, but we aim to achieve real-time linkage so that responses are displayed on the screen immediately when there is an inquiry from the sales department. Reconstructing planning operations, including special specification products, is also a future challenge. We are also considering expanding FLEXSCHE in conjunction with the introduction of SAP at other locations, based on the successful know-how at the Thai factory," says Mr. Ozawa. As a professional in fluid control, the KITZ Group is active on the global stage. The role of FLEXSCHE in supporting the group's global management from the perspective of production planning will become even more significant as the company grows.
Voices of Integrators
Due to the very tight delivery schedule for this project, we divided the work into three phases, conducting tests and verifications with KITZ after the completion of the first development, while proceeding with the second development during that time. We are grateful that we were able to meet the delivery schedule thanks to KITZ's cooperation.
To achieve system operation in an ultra-short term, we adopted a policy of minimizing customization and utilized the abundant features of FLEXSCHE, which allowed us to realize most of the customer's requests. Regarding the delivery date response function, we conducted various examinations and made various proposals to meet the requests, and we devised a plan together with the customer. This time, we believe that by cooperating with KITZ and receiving various teachings, we were able to realize a new production planning system that meets the requests.
We will continue to cherish the trust relationship built this time and strive to contribute to the further development of KITZ.
Overview of the implementing company
KITZ Corporation
Established | January 26, 1951 (Showa 26) |
---|---|
Capital | 21,207,084,670 yen |
Sales | Consolidated: 117,355 million yen, Non-consolidated: 64,438 million yen (Fiscal year ending March 2014) |
Business Description | Manufacture and sale of fluid control equipment (valves, system equipment, etc.) |
URL | http://www.kitz.co.jp/ |