Introduced FLEXSCHE to two factories in China
Achieved high compatibility with SAP and standardization of planning operations
Nidec Sankyo Corporation Electronic Components
- Created in June 2009
- Download PDF for Display
- Download PDF for Printing
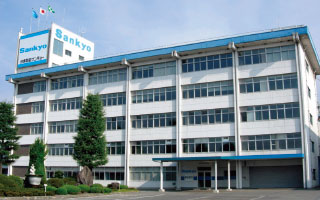
Nidec Sankyo Corporation
The town of Shimosuwa, a gateway town to Suwa Taisha, is also known as a town of precision machinery industry, called the Switzerland of the East.
One of the faces representing the industry of that town is Nidec Sankyo Corporation (hereinafter referred to as Nidec Sankyo), which is active globally in the business of electronic components and system equipment. To respond quickly to changes and strengthen international competitiveness, the company has achieved integration of technical information and integration of core systems with SAP, and the next step was the systemization of parts processing planning.
The production scheduler FLEXSCHE played a significant role in this systemization. First, FLEXSCHE was introduced to two factories in China. It has enabled parts processing planning without relying on manual labor, achieving not only efficiency but also centralized management and standardization of planning operations.
Promoting the integration of information to respond quickly to changes
To enhance international competitiveness, many Japanese manufacturing companies are expanding their production bases overseas. In the context of responding to changes and speed, such as multi-variety small-lot production and globalization, the important theme is how to improve quality while enhancing efficiency from a global perspective. The key to solving this difficult problem is the integration of information and standardization of operations through the use of IT.
Nidec Sankyo, a global player in the electronic components and system equipment business, is actively promoting the integration of technical information, the integration of core systems, and the standardization of parts processing plans, as well as the integration of information and standardization of operations through the use of IT.
The company's origins date back to 1948, with the completion of the first prototype music box. Today, it holds a world-class share in various product fields, including micromotors, motor drive units, lens drive units, magnetic card readers for ATMs, and robots for transporting LCD glass substrates. The core of the company's international competitiveness lies in its unique technology, which combines proprietary technologies such as material development and precision processing, based on magnetic and optical technologies.
In 2003, it became a member of the Nidec Group, a global manufacturer of comprehensive drive technology, and is aiming for further growth by leveraging the synergy effects of the group. Currently, the company is establishing a rapid response system to meet customer demands with thorough speed, adhering to the principle that "technology only becomes valuable when it meets customer needs," and maintaining a competitive advantage in productivity and a customer-first policy.
The risk of relying on manual planning operations is immeasurable overseas.
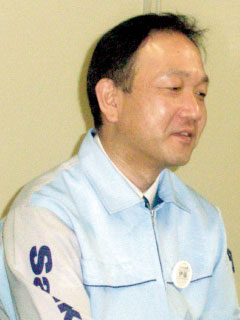
Management Headquarters System Department Chief Examiner
Koji Ito
"With a product range that extends from nearly one million electronic components produced monthly to unique robots, we started implementing SAP in 2001 to achieve overall system optimization while considering the characteristics of each business. We completed the integration of core systems such as production management and sales management at all 20 locations, including overseas, by 2007. The next challenge was the systemization of the parts processing plan, which had been a pending issue," says Eike Maruyama, General Manager of the System Department at Nidec Sankyo.
The company has production bases mainly in Asia, including China, Taiwan, Indonesia, and Vietnam, but faced significant challenges regarding parts processing plans, which are crucial for productivity.
- Due to reliance on manual planning operations, uniformity in planning operations could not be achieved.
- Staff were working overtime to cope, and there were requests from the field for additional personnel.
- Since the parts processing plan was not systematized, it was impossible to pass on know-how locally.
- It was difficult to quickly and accurately grasp what was being done locally.
- It was challenging to respond quickly to the resignation of planning staff.
- While there were voices of machine shortages, inventory reduction had not been achieved.
"Parts processing planning is extremely difficult. You need to know the characteristics of molds and machines, and elements such as people and processes are intricately involved. Moreover, overseas, cultures and customs differ. The risk of relying on manual planning operations is immeasurable overseas. Standardizing planning operations through systemization was urgent. It was also essential in terms of responding to fluid personnel," says Maruyama.
The company had previously attempted to systematize parts processing plans several times but was unsuccessful. Koji Ito, Chief Examiner of the System Department, explains, "The first problem was that it took hours to simulate and confirm. Creating a plan would take an entire day. Also, while SAP has planning functions, it is not suitable for timely changes. We were looking for something that could respond lightly and flexibly to requests such as wanting to simulate the plan I created."
Therefore, in 2007, they began a full-scale examination of production schedulers, considering global expansion and emphasizing smooth integration with SAP.
The key points for adopting FLEXSCHE were its flexibility and high compatibility with SAP.
In systematizing planning operations, Ito revisited the company's domestic factories to confirm "how parts processing planning is carried out." "The capabilities of each machine are in the heads of the staff, and they fill in the gaps while looking at orders. Such methods can be utilized with the intuitive operation capabilities of FLEXSCHE, and I thought that with FLEXSCHE, we could do what we were trying to do," reveals Ito as one reason for adoption.
The flexibility of FLEXSCHE was also a key point for adoption. "FLEXSCHE can be set to derive the desired schedule results, but it can also be set to leave room for human judgment, allowing for manual adjustments. This flexibility was also attractive. Additionally, FLEXSCHE's interface is flexible regarding integration with SAP, allowing us to quickly grasp the integration image with SAP."
In early 2008, FLEXSCHE was first introduced at the Pinghu and Shilong factories in China. MPS (Master Production Schedule) is created in SAP to generate orders, and that data is sent to FLEXSCHE. The base planning data is created by the headquarters' system department and provided to the Chinese factories, with the Chinese planning staff handling any changes. Instructions are output from the FLEXSCHE screen, and the results planned in FLEXSCHE are stored on the server, enabling centralized management at the headquarters with daily and hourly Excel outputs.
Additionally, some results are incorporated into FLEXSCHE. "By incorporating results into FLEXSCHE in multi-process cases, we are improving the accuracy of planning for subsequent processes," says Ito.
At the Pinghu factory, which handles motor drive units for home appliances, planning operations using FLEXSCHE have become established, and the effects of its introduction are already evident.
Achieved significant efficiency and standardization of planning operations.
The parts processing plan at the Pinghu factory takes the form of creating periodic plans and continuing them if there are no major changes. "One planning staff member used to work late into the night for about two days for each planning session, and there was a request for additional staff, but after the introduction of FLEXSCHE, one staff member can create a plan in less than a day. We also planned to assign another planning staff member to a different process, but with the introduction of FLEXSCHE, one staff member is handling both processes with ease," says Ito.
On the other hand, there were some challenges with the introduction at the Shilong factory. The factory handles a wide variety of motors used in audio-visual equipment, digital cameras, and industrial robots, and also involves multi-process work such as race (cutting threads on a round bar shaft). Additionally, the artisanal mindset of the planning staff was a barrier.
"At the Shilong factory, five planning staff members are handling the operations. The leader among them was sent for training to the Pinghu factory. By seeing the automation of planning operations with their own eyes and talking to the staff at the Pinghu factory, their mindset seems to have changed significantly. The change in the mindset of the staff is a major step forward," says Ito with a bright voice.
Considering the introduction of FLEXSCHE to other factories as well.
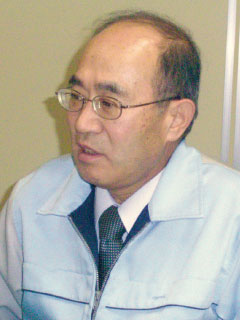
Management Headquarters System Department General Manager
Eike Maruyama
Maruyama says that the benefits of realizing the systematization of parts processing planning without relying on manual labor through the introduction of FLEXSCHE are significant. "Since parts processing planning was not systematized in Japan, we could not pass on know-how locally, but with the introduction of FLEXSCHE, planning operations have been standardized, and know-how can be passed on. Even if a planning staff member resigns, the next person does not need to memorize all the capabilities of molds and machines, allowing for quick responses."
Mr. Ito emphasizes that the approach to planning operations has significantly changed. "Previously, we based our planning on a daily schedule, but now we have shifted from 'day management' to 'time management,' determining what time to start setup and what time to start operations. Additionally, the Pinghu factory, which used to claim a shortage of machines, now has about 20% of its operations planned to stop, reducing inventory as well."
Regarding his impressions of actually using FLEXSCHE, Mr. Ito says, "I was very surprised that the results were displayed on the screen in about a minute when scheduling. If we were to systematize it ourselves, it would take one or two hours to process."
At the company, the system department handles all system implementations. "If we had to contact the manufacturer or system integrator every time a user had an inquiry, our response would be delayed. By implementing it ourselves, we can respond quickly to inquiries," says Mr. Maruyama. Currently, the company's system department consists of 41 members, supporting the foundation of its globally expanding business.
Regarding future developments, Mr. Maruyama states, "We upgraded SAP in the summer of 2008. Moving forward, stable operation and utilizing information for management indicators are important themes. We also want to actively participate in study sessions on FLEXSCHE to further enhance our skills. We are considering introducing FLEXSCHE to other factories, such as those in Singapore and Vietnam."
Overview of the implementing company
Nidec Sankyo Corporation
Head Office | 5329 Shimosuwa Town, Suwa District, Nagano Prefecture |
---|---|
Established | June 18, 1946 (Showa 21) |
Capital | 35,270,101,264 yen (as of the end of March 2008) |
Business Description | Electronic components-related business (micromotors, motor drive units, precision plastic molded products, mechanical units, etc.), system equipment-related business: industrial robots, card readers, others (music boxes, etc.) |
URL |