Deploying FLEXSCHE as a standard scheduler to factories domestically and internationally
Highly evaluated for its excellent flexibility in meeting the business needs of various industries
Kaneka Corporation Chemicals and Food
- Created in October 2013
- Download PDF for Display
- Download PDF for Printing
Kaneka, a leading comprehensive chemical manufacturer in Japan, is a global company recognized worldwide for its achievements and technology. The company's products, utilizing its materials, span a wide range from automobiles to smartphones, medical devices, and food. As the company continues to expand its business globally and grow, it has set a long-term vision of achieving sales of 1 trillion yen and an overseas sales ratio of 70% by 2020. To realize this vision, the Factory System Development Group is working to innovate production operations at manufacturing sites by utilizing ICT.
To develop and deploy a full-scale MES (Manufacturing Execution System) across various factories and manufacturing sites, the group adopted FLEXSCHE, highly valuing its flexibility to meet the business needs of multiple industries as a standard scheduler. The first step was its introduction at the Osaka factory and Kaneka Malaysia. The aim is to eliminate personalization and improve operational efficiency, while also enhancing and optimizing the quality of planning through information sharing between sales and the field.
Towards achieving sales of 1 trillion yen and a 70% overseas sales ratio by 2020
Kaneka, a comprehensive chemical manufacturer familiar from its TV commercials as "The company that fulfills wishes with chemistry." Recently, it has been creating new value through a chemical approach in various industries, including the highly noted functional food ingredient "Coenzyme Q10," essential electronic materials for mobile devices like smartphones, solar cells, and catheters for intravascular treatment.
In 2009, the company celebrated its 60th anniversary and announced a new corporate philosophy: "We will co-create value that opens up the future through the creative fusion of people and technology, contributing to the global environment and a prosperous life," and set a long-term vision aiming for sales of 1 trillion yen and a 70% overseas sales ratio by 2020.
"Innovation in production operations is essential to realize our long-term vision. It is also necessary to accelerate the speed of new product development, expand overseas manufacturing bases, and further promote cost reduction and operational efficiency, which we have been working on traditionally. Utilizing ICT is a crucial point in promoting these reforms. Partial introduction of MES began at the Takasago Plant in 2001, and its importance has gradually been recognized company-wide, leading to the establishment of the Factory System Development Group in 2012," says Satoru Murakami, leader of the Factory System Development Group.
The group, which aims to improve efficiency and solve issues in manufacturing operations by utilizing ICT, began considering schedulers as part of the development and introduction of MES. Since the company’s management strategy is based on maximizing manpower without increasing personnel, it was difficult to realize the long-term vision without a scheduler to solve the challenges of highly personalized production planning tasks.
Planning is not about completing "tasks" but about pursuing the best plan
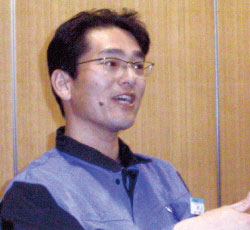
Production Technology Headquarters Production Technology Department
Factory System Development
Group Leader Satoru Murakami
The initial introduction of the scheduler was decided to be implemented at both the Osaka factory and Kaneka Malaysia.
Major阪FactoryManufacturing DX and Smart Factory導JoiningではFunction性樹脂の1つ、耐侯性MMA系Fィルム「サンデュレン⋚」の製造toTarget Audienceandしました。柔軟性に乏しいMMA系樹脂のFィルム化toDay本で初めて実現した同Productは、長期の耐久性is必要な屋根材のラミネートandAutomobiles加飾Fィルム、反射シートand moreに使用され高い評価to得ています。
Previously, the production plan for this product was created using Microsoft Excel, but personalization progressed, and challenges arose in standardizing operations and responding to changes.
「サンデュレン⋚の製造では、ペレットtoつくり、そのペレットto材料にしてFィルムtoつくります。1つのProductにNakata間品is存在するため、管理する品種数は300種類くらいになります。多品種であるIandに加え、あるProducttoつくった後にはIのProductはつくれNoand moreConstraintsも複雑.また、お客様の急なオーダーに対してFレキシブルに対応できるIandによって優位性は確保できますis、MicrosoftExcelto使ってPeopleの頭のNakataで計画to試行錯誤していては迅速な対応も難しい。その計画is本当に良いのかどうか考える時間的な余裕もありません」andFactory System Development GroupTakashi Yamaguchiは話.
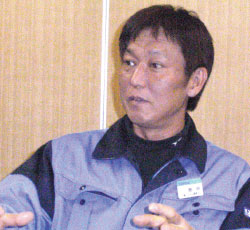
Production Technology Headquarters Production Technology Department
Factory System Development Group
Chief Shoji Shimabara
Regarding the challenges in the quality of planning in traditional planning, Shima Shouji, Chief of the Factory System Development Group, points out, "The current planning has become 'work.' Once the plan is made, the 'work' is over. The important thing is to pursue better planning. How can production be organized to achieve the most efficiency and cost reduction? That is where the significance of planning lies. Also, planning requires a medium- to long-term perspective. If the planning period is about a week, it might be possible to plan with Microsoft Excel. However, when it comes to a monthly basis, it is difficult to plan manually."
一方、カネカマレーシアManufacturing DX and Smart Factory導Joiningでは様々なProductManufacturing DX and Smart Factory展開to視野に、まず塩ビ強化用樹脂のカネエース®Bの製造toTarget Audienceandしました。Building Materials、パイプ、ボトルand包材and moreに活用されるカネエース®Bは、カネカis世界シェアのおよそ半分to獲得している主力Productの1つ.
The introduction of the scheduler to Kaneka Malaysia had different objectives than for domestic use. "Kaneka Malaysia is looking to expand its business, and the goal is for one person to plan for multiple manufacturing sections. The scheduler is the tool for that. Also, by introducing it from the perspective of the entire factory, maximizing the return on investment was sought," says Shima.
Choosing FLEXSCHE from the perspective of standardizing and expanding the scheduler
In selecting the scheduler, the perspective of standardizing and expanding was emphasized. The key point was the "two flexibilities."
The first point is the flexibility to respond to the constraints of various departments with standard functions. "Around 2007, when I was in the research department, it was decided to introduce a scheduler to a related company of the Kaneka Group. I could develop add-ins for the constraints of the introduction site, but I cannot support it forever. The important thing is that the person in charge of production planning at the introduction site can make various changes with the standard functions of the package. At that time, I investigated many schedulers, but only FLEXSCHE could meet the complex constraints of the introduction site without developing add-ins," says Hideki Niina, Chief of the Factory System Development Group.
The second point is the flexibility to easily add custom functions if the standard functions cannot handle it. The company manufactures a wide variety of products, and the constraints differ by department. Therefore, there are inevitably parts that cannot be handled by standard functions alone. FLEXSCHE provides a wealth of mechanisms to achieve what you want to do, such as the ease of developing custom functions because the functions for accessing the internals are openly available.
"The important points are the richness of standard functions that minimize the need for add-in development and the ease of developing add-ins for individual constraints of each department, these two flexibilities. Cost is also important, but it is meaningless if you cannot do what you want. By minimizing add-in development and keeping costs down, while being able to properly develop add-ins where necessary, FLEXSCHE was found to be very cost-effective compared to other products," says Shimabara.
Furthermore, Shimabara emphasizes the importance of the speed at which user feedback is reflected, continuing, "Five years ago, there was a period when we investigated FLEXSCHE. This time, during the process of considering the scheduler for company-wide deployment, we received a presentation of FLEXSCHE again and were surprised by its evolution. It is also important to respond to environmental changes through package version upgrades in terms of cost and workload. I felt that FLEXSCHE reflects user feedback faster than other companies."
The consideration of the scheduler began in the summer of 2011, and the decision to adopt FLEXSCHE was made in the fall. At the beginning of 2012, FLEXSCHE was introduced to Kaneka Malaysia and the Osaka factory. Both factories are still in the stage of establishing it on-site, but the elimination of personalization is progressing.
"It takes a certain amount of time to change the traditional way and establish it on-site, but with the introduction of FLEXSCHE, anyone can now create plans that incorporate constraints. In the future, even if the person in charge changes, it will be possible to immediately create plans at a certain level. There are also significant benefits in terms of human resource utilization, such as being able to organize rotations," says Yamaguchi.
"Even if the plans made are not perfect, being able to create plans that adhere to constraints with the scheduler is a very significant achievement," says Shima.
Creating evaluation criteria for plans and utilizing data for optimization are future themes
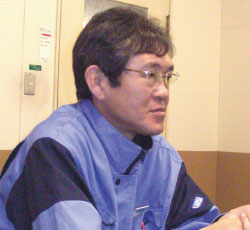
Production Technology Headquarters Production Technology Department
Factory System Development Group
Chief Hideki Niina
The Factory System Development Group has identified two points for utilizing FLEXSCHE in the future. The first is the evaluation of plans. In the midst of complex constraints, how to set criteria for judging the quality of plans created using FLEXSCHE. "It was a personal judgment, and it was difficult for others to refer to it even if they wanted to. By using FLEXSCHE, the fact that the plan was created by a system based on data becomes one criterion. However, in the process of simulating to find the best plan, what to use as a criterion for judgment. We would like to create evaluation criteria for plans while referring to FLEXSCHE's evaluation charts," says Niina.
The second is the optimization of the production system. The goal is to effectively utilize information related to manufacturing, such as sales information, manufacturing information, and production progress information, centered on production management, to enhance the contribution to management. "Is the 'due date' presented by the sales department to the production department the 'due date' that the customer really needs, or is it a 'due date' based on the sales department's sense? For example, if production efficiency decreases for this due date, and this much loss occurs from a management perspective, if we can feedback such analysis results to sales, it will lead to efforts towards optimization as a company. Realizing a system that increases efficiency and generates profits while responding to customer trust is an important challenge for the future," says Murakami.
"At Kaneka Malaysia, we are creating a system centered around the production management department, where all manufacturing information is gathered, allowing sales and manufacturing site personnel to share information. Sales can also view the progress of production," says Mr. Shimabara.
Regarding future developments, "One of the benefits of introducing FLEXSCHE is the after-sales support provided by FLEXSCHE Corporation. They have been quick to respond to our needs, such as the 'global date support' requested by Kaneka Malaysia. We ask for further cooperation in addressing various demands and challenges that arise as we proceed with the standardization of production planning. We also hope to expand the deployment of FLEXSCHE to overseas factories, and we expect strengthening of global support, including support," says Mr. Murakami.
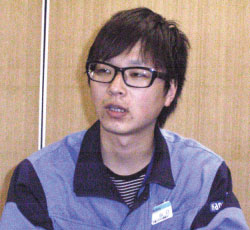
Production Technology Headquarters Production Technology Department
Factory System Development Group
Mr. Takashi Yamaguchi
Kaneka is advancing production innovation to realize its long-term vision. Together with the factory system development group, which serves as the driving force, FLEXSCHE continues to evolve as the company's standard scheduler.
Overview of the implementing company
Kaneka Corporation
Established | September 1, 1949 |
---|---|
Osaka Headquarters | 2-3-18 Nakanoshima, Kita-ku, Osaka City |
Tokyo Headquarters | 1-12-32 Akasaka, Minato-ku, Tokyo |
Capital | 33,046 million yen (as of March 31, 2013) |
Number of Employees | (Consolidated) 8,600 employees (Non-consolidated) 3,289 employees (as of March 31, 2013) |
Business Description | Chemicals, functional resins, foam resin products, food, life sciences, electronics, synthetic fibers, etc. |