In the commercial printing process, it is essential to respond to incoming orders one after another.
Achieving a departure from personalization and realizing efficient operation of rotary presses
Mainichi Shimbun Chugoku Shikoku Printing Co., Ltd. Printing
- Created in January 2008
- Download PDF for Display
- Download PDF for Printing
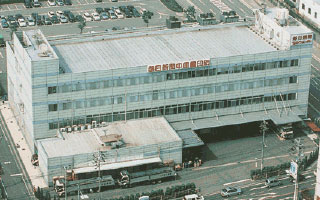
Mainichi Shimbun Chugoku Shikoku Printing Co., Ltd.
We want to provide fresher news. Mainichi Shimbun Chugoku Shikoku Printing Co., Ltd. (hereinafter referred to as Mainichi Shimbun Chugoku Shikoku Printing) was established to cover newspaper printing in the Chugoku and Shikoku regions to improve time efficiency.
The company is also focusing on commercial printing, which accounts for about half of its sales.
As a newspaper printing company, we emphasize "accurate delivery dates and quality," which are the basis of trust in commercial printing as well.
The keyword for the printing process support system with FLEXSCHE is "tag," and flexibility to respond to instant decisions was also required.
Challenges in creating process charts, which are the basis of commercial printing
In 1988, the Seto Ohashi Bridge, connecting Honshu (Kurashiki City, Okayama Prefecture) and Shikoku (Sakaide City, Kagawa Prefecture) across the Seto Inland Sea, opened. As a new era transportation network, it significantly changed the flow of tourism, logistics, and distribution. In the same year as the opening of the Seto Ohashi Bridge, Mainichi Shimbun Chugoku Shikoku Printing was also established in Kurashiki City, Okayama Prefecture.
Before the opening of the Seto Ohashi Bridge, Mainichi Shimbun transported the Mainichi Shimbun and Sports Nippon newspapers printed at the Osaka headquarters to the Chugoku and Shikoku regions. However, the company was established with the mission of the newspaper company to shorten transportation time and deliver fresher news to readers in the Chugoku and Shikoku regions.
"Newspaper readers eagerly await the arrival of the newspaper every day. We are keenly aware that meeting the process time is a way to respond to readers, sales outlets, transportation companies, and others who cooperate with us," says Mr. Makino, Director and General Manager of the Sales Headquarters.
This corporate culture is also utilized in the company's commercial printing. The company's commercial printing covers a wide range, including flyers, booklets, and form printing, accounting for about half of the company's sales. Amidst the increasingly severe environment surrounding commercial printing, such as the use of the internet as an advertising medium, intensified cost competition, and the expansion of overseas printing, the company is striving to build a solid trust relationship with about 50 customers, emphasizing "accurate delivery dates and good quality" as sales points, and is working on business continuity and development.
Strict adherence to delivery dates is essential in building trust relationships. On the other hand, it is also required to efficiently and fully utilize commercial offset rotary presses for commercial printing. The company faced significant challenges in creating process charts, which play an important role in meeting both of these needs.
The core of systemization is the concept of "tag."
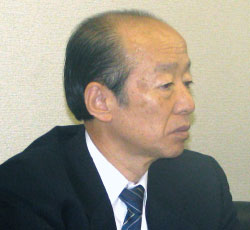
Director and General Manager of the Sales Headquarters
Osaka Sales Office Manager, Mr. Takehiko Makino
Whether or not a job can be received in commercial printing depends on whether it is possible to insert new work into the already scheduled work. Since the printing process is modified in real-time to accommodate incoming orders, it is necessary for all parties involved to always share the latest information. The basis for this is the process chart.
Traditionally, the production department manually entered the necessary data to create process charts and manually rearranged the order of processes. This series of tasks was performed by a single person using word processing functions and unique know-how, resulting in a situation where no one could substitute in case of illness, etc.
"The newspaper printing process hardly changes daily, so there is no need for systemization. On the other hand, commercial printing changes daily. The process chart is the basis of commercial printing. It was urgent to systemize it so that anyone could easily create and modify it" (Mr. Makino).
A project for the printing process support system was created, centered around Mr. Makino, who has experience in the systemization project of newspaper editing at Mainichi Shimbun. The first task of this project was to create a specification document.
"Sales input order data into the order system, including client names, prices of ordered items, delivery dates and locations, product names, and print quantities. The order data contains elements that determine the process. The starting point of systemization was to incorporate this order data into the process chart online and realize automatic assembly" (Mr. Makino).
Mr. Makino investigated the trends of local competitors, but found no companies that had systemized process chart creation. During the investigation, he heard about a method of handwriting information on business card-sized paper and sticking it on a board with a time axis to create a process chart, and decided to incorporate the concept of "tag" into systemization, inspired by this.
"The concept of 'tags' was traditionally similar to the format of process charts created with word processors, which matched well in terms of continuity," said Mr. Makino. A 'tag' is created for each order, order information is collected online, printing time is automatically calculated, and the 'tags' are automatically arranged in printing order based on the due date. This concept was made the core of the printing process support system in the project, and system requirements were compiled, with development proposals requested from multiple manufacturers.
The deciding factor for adoption was flexibility in responding to instant decisions.
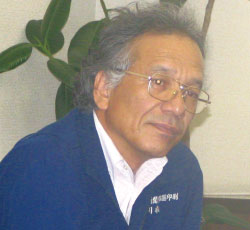
Production Group Manager and Editing Team Leader
Mr. Jodai Kawamoto
Mr. Kawamoto, who worked with Mr. Makino on creating the specifications, discusses the challenges of systematizing process chart creation: "During our review, we tried to create a simple program, but it didn't go well. This was due to the significant variability involved. We can't wait until all the items necessary for printing (such as printing conditions) are ready to create the process chart. Determining how much needs to be ready to create the chart was very challenging."
The significant variability became an important theme this time. "In the systematization of process chart creation, necessary order data is automatically calculated and arranged, but the specifications were compiled with the premise that the final adjustments would be made by the production department, without seeking perfection from the program. This decision was based on the difficulty of achieving perfection through programming and the need to retain human expertise in process chart work to prepare for unforeseen circumstances, drawing from past commercial printing experience," said Mr. Makino.
For example, even if the computer calculation shows a delay of one minute, it is important to leave room for human judgment to consider one minute as an acceptable range. Flexible responses to various changes, such as delays in data submission from clients, are also necessary.
"Basic information is handled by the process chart, while instantaneous decisions are made by humans. There are cases where 'tags' are rearranged later as records. Leaving room for human thought allows for better handling of system troubles and other issues," said Mr. Makino.
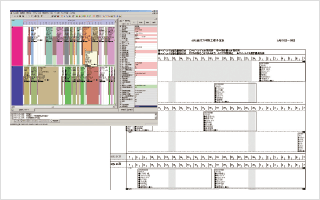
Process Chart Sample and Printing Image
Based on the specifications, each manufacturer conducted presentations. The product selection was smoothly decided on the day the presentations ended.
Regarding the reasons for adopting FLEXSCHE, Mr. Makino reflects, "Among the presentations and demos we received, FLEXSCHE was the most convincing. Its simplicity was attractive, but the deciding factor was its flexibility in smoothly accommodating human judgment. Having previously worked in computer-related jobs, I knew firsthand how challenging and costly it could be to add specifications, which also supported my decision. FLEXSCHE's ease of development and excellent flexibility were highly evaluated, and the comprehensive functionality that forms the basis of FLEXSCHE was also a key point. Of course, the cost performance was also satisfactory."
Short-term implementation based on solid specifications
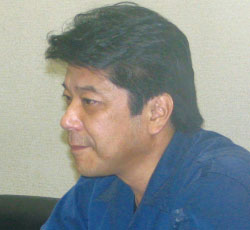
Production Group Section Manager
Mr. Yasumasa Shimizu
The features of the printing process support system using FLEXSCHE can be summarized in the following seven points.
- Online integration of data into the process chart
- Automatic calculation of printing time based on the content of the print job (paper size, number of copies, presence of folding, etc.)
- Automatic arrangement of 'tags' (printing order) based on the due date
- 'Tags' that do not meet the due date are visually represented with colors or markers for easy identification
- The number of rotary presses can be additionally registered from the initial setting (expandability)
- Process charts can be viewed online even at the sales office in Osaka
- Flexible response to final human judgment, including manual handling of 'tags' that overflow from automatic arrangement
From November 2005 to March 2006, the specifications were compiled, and the decision to adopt FLEXSCHE was made at the end of June 2006, with delivery at the end of July 2006. After debugging, full operation began in August 2006. The existence of solid specifications made it possible to implement the system in just two months from the decision to adopt to full operation.
Regarding the support from the system integrator ACT in the introduction of FLEXSCHE, Mr. Hiramatsu, who played a bridging role between the company and ACT on the system side and was responsible for subsequent debugging, highly evaluates, "We organized troubles and issues and asked ACT to resolve them, and they responded quickly and appropriately, which was very helpful."
Creating process charts without requiring personal skills
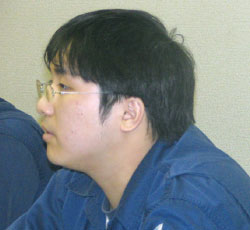
Production Group
Mr. Fumiya Hiramatsu
In the printing process support system, necessary data for the process chart is extracted online from the order system in CSV format and automatically input into 'tags', achieving automatic arrangement based on the due date. "The printing process support system has resulted in many benefits, such as the elimination of duplicate work, prevention of input errors during manual entry, prevention of data correction omissions, and simplification of process chart creation operations, eliminating the need for personal skills. We were also able to create a system where anyone can easily create or modify process charts, which was the initial goal," said Mr. Makino, discussing the effects of the introduction.
In the company's printing process, the basic unit is a day, with the outlook for printing until midnight and the next day decided by 8 PM. "It is important that the next day's printing process is efficiently filled by the previous day, and being able to grasp the schedule ahead is convenient not only for the printing site but also for sales," said Mr. Shimizu, who is responsible for operating the process chart.
Rules have also been established to smoothly operate the process chart. "We have established a rule that if the necessary items are not entered when sales input data, it will not be included in the process chart. However, if it is absolutely undecidable, it is possible to manually input directly into the system and place a dummy item on the process chart to tentatively reserve the printing process," said Mr. Shimizu.
Additionally, operation logs can be recorded to aid in analysis. "Initially, there were troubles due to unfamiliarity with the printing process support system, so we made it possible to record the minimum operation logs to investigate the causes. Improvements have emerged through use, but there have been no major troubles, and operations are running smoothly," said Mr. Makino.
The company's commercial printing, which is based on trust as a newspaper printing company, is supported by the printing process support system using FLEXSCHE.
Voices of Integrators
The initial request was from Mainichi Shimbun Chugoku Shikoku Printing, who provided us with the specifications and said, "We are considering developing a printing process support system, so please propose a good system."
Our company conducted a presentation on system construction using FLEXSCHE, and as a result, we received the order. The ease of operation and the excellent flexibility of customization offered by FLEXSCHE were highly evaluated.
All requests from Mainichi Shimbun Chugoku Shikoku Printing were provided as specifications. The specifications were solid, making system development easy, and we were able to build it in just two months, a short period until implementation. We are deeply grateful to Director Makino and the project members for their efforts in system construction.
A year has passed since the system started operating, and it is currently running smoothly. We are very pleased to hear that it has become an indispensable system for planning printing process schedules. We will continue to strive to maintain a good relationship with Mainichi Shimbun Chugoku Shikoku Printing by ensuring long-term operation and promptly addressing improvement points.
Overview of the implementing company
Mainichi Shimbun Chugoku Shikoku Printing Co., Ltd.
Head Office | 148 Shimojo, Kurashiki City, Okayama Prefecture |
---|---|
URL | |
Established | September 1988 (Showa 63) |
Capital | 160 million yen |
Number of Employees | 90 people |
Business Description | Printing of newspapers, promotional materials, text materials (commemorative magazines, company newsletters, bulletins, etc.), office printing materials, various forms, packaging materials, business cards, postcards, invitations, etc. |
Main Clients | Mainichi Shimbun, Sports Nippon Newspaper |