To tackle the most important issue in manufacturing, "increasing throughput,"
the entire company united to independently introduce FLEXSCHE and steadily achieve results
- Produced in March 2018
- Download PDF for Display
- Download PDF for Printing
Sheet Metal Processing Industry
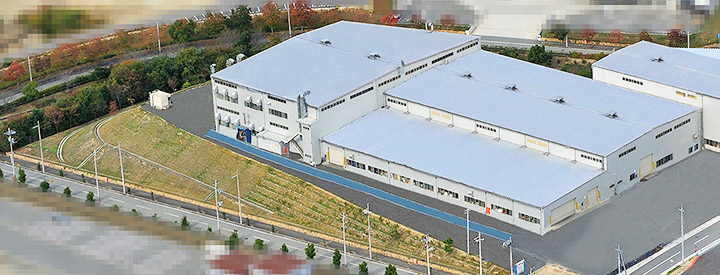
"Increasing Throughput"
It is always an important issue for all manufacturing industries, yet solving it is not easy. The company that chose FLEXSCHE as a solution is 'Nakahara Co., Ltd.,' which handles general sheet metal processing and directly exports overseas. Nakahara, which has enabled consistent in-house production from design to delivery, decided to introduce FLEXSCHE to aim for efficient factory operation and production management, thereby reducing outsourcing costs and enhancing productivity.
In introducing FLEXSCHE, the company tackled it as a united effort without relying on a system integrator, and they have successfully achieved results. We spoke with the team members involved in the introduction of FLEXSCHE at the company about the challenges they faced and overcame, and the effects they felt.
A major sheet metal manufacturer active globally
'Nakahara Co., Ltd.,' boasting a long history since its founding in 1940, is a manufacturer handling general sheet metal processing at its headquarters factory in Kasai City, Hyogo Prefecture, and the nearby Ono factory (Ono City). With 280 employees (as of March 2018), it is a considerably large-scale factory for a sheet metal processing manufacturer. Major clients include 'Caterpillar Japan LLC,' 'Heiwa Metal Industry Co., Ltd.,' and 'Okura Yusoki Co., Ltd.,' with whom they have had transactions since the early days of their founding, manufacturing items such as construction machinery covers.
Additionally, it is characterized by its well-equipped facilities, including two massive 2200-ton press machines and cationic electrodeposition coating, which set it apart from other sheet metal manufacturers, allowing for the production of a wide range of products. One of the highly evaluated equipment is the processing machine that can cut with nitrogen, which can cut metal without forming an oxide film that causes paint peeling. As the standards for product quality demanded each year become higher, they are achieving manufacturing that fully meets these standards and earns the trust of customers.
-
2200-ton press machine
-
Cationic electrodeposition coating
One of the reasons Nakahara is supported by customers is its consistent in-house production system, from processing, welding, and assembly to painting and delivery. They also focus on design, with the factory manager, Mr. Tanaka, introducing, "We also create drawings and design based on 3D models received from customers."
The starting point for Nakahara's growth to this extent was the introduction of TOC in 2000 and the establishment of the Kasai headquarters factory in 2008. Especially after the establishment of the headquarters factory, the range of orders expanded by strengthening equipment, and the number of customers increased. The number of employees also continued to grow. Currently, they are active not only domestically but also as a global company directly exporting to the United States, Mexico, Brazil, Indonesia, and other countries.
A comprehensive IT strategy aimed at improving throughput
Nakahara decided to introduce FLEXSCHE in 2010. Within the company, they were in the midst of continued growth using the TOC concept introduced in 2000. They decided to strengthen production management based on a comprehensive IT strategy aimed at further increasing throughput.
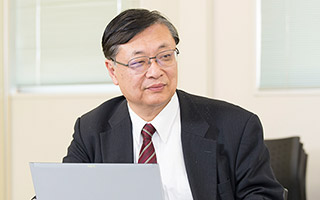
Mr. Mineichi Honma, Representative Director of 'Honma Co., Ltd.'
Mr. Mineichi Honma, a consultant advisor involved in the selection of the production scheduler (Representative Director of 'Honma Co., Ltd.'), says, "When I once consulted with FLEXSCHE, the sample data I saw and the explanation I received perfectly matched Nakahara's TOC concept. The fact that FLEXSCHE directly provided various consultations was also a positive factor for the subsequent introduction."
当時の生産計画の立案はMicrosoft Excel®to用いたものでした。短期間のうちにどんどんandFactoryisMajor規模化するナカハラでは、計画立案の範囲もDayごandに広くなっていきます。その当時launch現在に至るuntil計画立案toContactする同社生産管理チームManagerのKawahara合氏もMajor変な苦労to感じていたそう.「Systemto用いNo計画立案にはAfter all,限界to感じていました。実際のandIろそれほど厳密に計画to立てるIandはできていませんでした」and計画立案に改善の余地is多分にあったIandto明かしました。
As the load on some processes increased, there were inevitably processes that had to be outsourced. For Nakahara, which can produce consistently in-house, outsourcing costs are a hindrance to increasing throughput, and the main purpose of introducing FLEXSCHE is to promote further in-house production through production efficiency and to practice TOC.
The first step was to revamp the production management system. The system previously introduced was not functioning well and was only used for outsourcing orders. Enhancing the core system was a critical issue to maximize the use of FLEXSCHE. However, it took an enormous amount of time to address some special business processes, and the new production management system finally went into full operation in 2014. Four years after the decision, the introduction of FLEXSCHE finally began.
The entire company is committed to collecting vast amounts of working time information
"When we first started moving towards implementation, I remember feeling that there was a huge barrier to getting FLEXSCHE up and running when we consulted with FLEXSCHE at 'OpenDay'.
These are the words of Mr. Asami, the assistant to the company's operations (system in charge). For this implementation, Nakahara did not rely on a system integrator and carried it out entirely in-house. He was the person responsible for most of the actual work. The challenge was 'collecting operation time information for processes'. For scheduling, operation time information is, of course, indispensable. Until then, we had set a guideline for operation time for cost estimation, but there was a discrepancy with the actual operation time, and the data was insufficient to provide to FLEXSCHE.
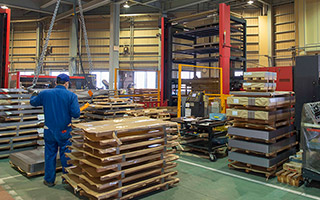
Some of the operation time information for machines such as 2D laser cutters and turret punch presses was obtained through CAD/CAM, but for other processes, we had no choice but to measure the actual operation time. Collecting operation time information for all processes in a factory of this scale naturally requires a lot of time and cost. Moreover, the cooperation of the factory workers is essential for the measurements, which imposes a burden. However, the management of Nakahara had the determination that 'it must be done to realize TOC', and led the company-wide implementation effort.
"We recorded the originally set guideline times on the work instructions and received feedback from the field on the differences with the actual operation times. In some cases, the guideline time was as much as 300% longer than the actual time, which was surprising. Thanks to the president himself instructing during morning meetings to 'make sure to do it properly', feedback was steadily gathered. I believe that the operation of FLEXSCHE could not have been realized without the cooperation of all employees."
This data collection not only advanced the implementation of FLEXSCHE. Accurate operation time information led to the renewal of work management indicators, reassessment of workers, and leveling, and the updated operation times were also reflected in the cost estimates.
The period required to gather most of the data was about one year. It was in September 2016 that we began test operations in conjunction with the production management system.
"At this stage, we finally began to see new information that had not been clear before, and I strongly felt 'this can work'."
It was in November of the same year that full-scale operation was achieved. The work of obtaining feedback on operation times and updating the master data continues even now, improving data accuracy and leading to more precise scheduling.
Of course, the implementation work does not end with just collecting master data. Mr. Asami, who was in charge of the implementation work, said, "Understanding FLEXSCHE itself was also very challenging. I was prepared for the fact that it wasn't something simple that could be understood just by reading the manual... As part of my studies to advance the implementation work, I made great use of the mailing list. When I first started working, even when I asked questions that were off the mark, the representatives from FLEXSCHE Corporation responded very politely, which was very helpful. The exchanges of questions from other users are also made public, which I also utilize in my FLEXSCHE-related work," he said, appreciating the support from FLEXSCHE Corporation.
Overcoming challenges and further expanding the FLEXSCHE implementation process
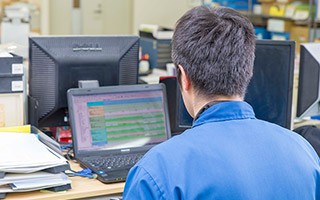
Since its operation, the load chart of FLEXSCHE has been unexpectedly utilized at Nakahara. It is a function that visually represents the load rate of each process during the relevant period based on the scheduling results. This load information is shared with each team manager on the site and is used for production management. Mr. Kawai, who is in charge of production planning, said, "On FLEXSCHE, the future load status of each process has become visible. When the load is high, we can quickly make decisions such as advancing production or outsourcing orders, making it easier to adjust lead times," and he feels the effect.
In Nakahara, the processes that tend to become bottlenecks are the initial processes in production, such as cutting and bending. Naturally, if there is a backlog there, it affects all processes. Although Nakahara has not yet reached the level of in-house production they are aiming for, thanks to the ability to quickly make decisions to reduce the load on cutting and bending processes, it is contributing to improving throughput.
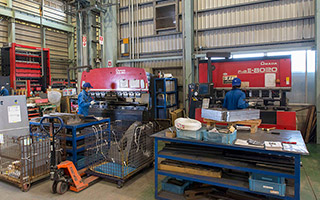
As of the time of the interview (March 2018), the scheduling targets were limited to machine processes, including welding and cutting/bending. In the future, they are considering expanding the targets to include sub-assembly processes and painting processes, and are making preparations.
"The sub-assembly process is difficult to coordinate with customers, and the painting process is complex to model, so it won't be straightforward. However, we consider these to be important future challenges that cannot be avoided for the practice of TOC," said Mr. Asami.
The goals that Nakahara sets as a company are 'to unite all employees under the management policy based on the practice of TOC, customer-first principle, and social contribution', and 'to more than double the current labor productivity'.
Mr. Asami added at the end of the interview, "I feel that FLEXSCHE will continue to be indispensable for achieving these goals."
Overview of the implementing company
Nakahara Co., Ltd.
Location | 2001-56 Maruyama, Amibiki-cho, Kasai City, Hyogo Prefecture |
---|---|
Established | 1940 |
Capital | 95 million yen |
Number of Employees | 280 employees (including 36 indirect workers) |
Factory and Research Institute | Kasai Headquarters Factory, Ono Factory |
Business Overview | General sheet metal processing, mainly steel plates (plate thickness 0.8 to 6 mm), but specializing in thin plates |
URL | http://www.nakaharagp.co.jp/ |