Adopted successively for production and transportation in two districts
Utilized open FLEXSCHE instead of complete in-house development
Nippon Steel Corporation Steel
- Created in April 2006
- Download PDF for Display
- Download PDF for Printing
Nippon Steel Corporation's Yawata Steel Works, which always appears in history textbooks. The first blast furnace was lit in 1901 (Meiji 34). Over the course of more than 100 years, Nippon Steel Corporation has not only become the industry leader domestically but also ranks in the top three in the world in terms of crude steel production.
Behind such growth, the annual production innovations play a significant role, and as part of that, the company has introduced FLEXSCHE. Since last year, they have been advancing the introduction of FLEXSCHE for the transportation schedule in the Tobata area of the Yawata Steel Works and are close to operation. However, in fact, the company had already introduced FLEXSCHE to the production line in the Yawata area of the same steel works a year prior.
Why was FLEXSCHE introduced in quick succession within a short period? This time, Mikio Urano, the representative of FLEXSCHE Corporation, accompanied the interview, and we spoke with four people involved in the introduction of FLEXSCHE.
Considering the introduction of a scheduler for transportation planning
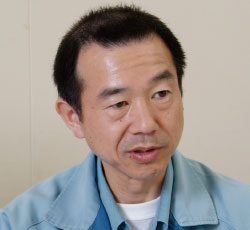
Nippon Steel Corporation Yawata Steel Works
Production Operations Department Logistics Planning Group
Manager Terumitsu Koga
As you head west by bus from New Kitakyushu Airport, you will eventually see a group of factories within a vast site and a large blast furnace in the back. That is Nippon Steel Corporation's Yawata Steel Works.
Nippon Steel Yawata Steel Works originally started as a government-run operation but was later privatized, and now it has steelworks not only in Yawata but also in Muroran, Kimitsu, Nagoya, Oita, and other production bases. Among them, Yawata Steel Works boasts the longest history of over 100 years.
The vast premises of the Yawata Steel Works are divided into the Yawata and Tobata districts, connected by the approximately 6 km long "Kurogane Line" dedicated railway for transportation. In the Yawata district, electromagnetic steel sheets, civil engineering steel sheet piles, and rails are manufactured, while in the Tobata district, steel sheets for automobiles, steel sheets for containers such as beverage cans, stainless steel sheets, and spiral steel pipes are produced. The introduction of FLEXSCHE is being promoted for the transportation planning system within the Tobata district.
"In the Tobata district, when raw materials such as iron ore and coal enter from the port, they are sent to the blast furnace via the coke plant and other facilities. After going through several processes, they are distributed to the tinplate factory if it's tinplate, or to the stainless steel sheet factory if it's stainless steel sheets, and eventually stored in the product warehouse. The application of FLEXSCHE this time targets the transportation part from when the finished products are loaded from the product warehouse onto ships or trucks." Generally, it is uncommon for a production scheduler to be adopted for transportation scheduling. However, due to the complexity of the problem in this system, what was needed was precisely a production scheduler.
The key to efficiency is the coordination of three schedules
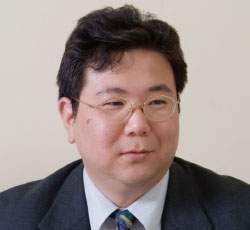
Nippon Steel Solutions Corporation
Steel Solutions Division
Kitakyushu System Center
Steel 3 Group
Senior Manager
Mr. Hideaki Kudo
"Meetings for scheduling were held every shift. We would discuss how to plan the transportation for the next shift." Once the products are completed, they are packed and transported to the product warehouse, which alone has 20 locations. Moreover, the destinations include "export ship berths," "domestic ship berths," and there is also direct land transportation by truck from the product warehouse, as well as movement between warehouses called "horizontal transfer." There are numerous factors complicating the creation of schedules, such as the constraints associated with the cranes placed at each location and the limited number of pallets available.
"Until then, the scheduling was done manually, with each person responsible for 'product warehouse planning,' 'carrier planning,' and 'berth loading planning' thinking about their respective plans every day. Additionally, there was one person responsible for overseeing the overall schedule, and since the steelworks operates 24 hours a day with three shifts, a total of 12 people were involved in planning. Therefore, the cost of creating the plans was enormous."
The major challenge in transportation scheduling was to formulate a consistent schedule through the coordination of these three schedules. To create an efficient schedule, it is necessary to load and dispatch products from the product warehouse in accordance with the arrival time of the ships, and the three plans of "product warehouse," "carrier," and "berth" must be smoothly coordinated to achieve a high-precision schedule overall.
"We aimed for smooth coordination by having four people discuss every shift, but in reality, there were fluctuations in operations, making it very challenging. It is true that a great deal of time and effort was spent on formulating highly accurate plans. Reducing such inefficiencies was a major challenge." Additionally, there was a sense of limitation in relying on manual scheduling when considering future prospects.
"It was only because of the accumulated know-how of each planning person that we were able to somehow manage daily scheduling, even if not perfectly. However, they will eventually leave, and before that happens, we must ensure that such know-how is passed on to the next generation and the one after that. It is unrealistic to repeat this endlessly, so we decided that it would be better to objectify the know-how at an early stage."
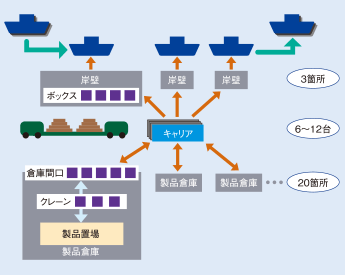
Thus, the decision was made to build a scheduling system. Initially, Nippon Steel Solutions, responsible for constructing the transportation planning system in the Tobata district, intended to develop a completely original system without using package software. However, around that time, there was an opportunity to see the production scheduler FLEXSCHE, which was already being introduced to replace the existing system in another district of the Yawata Steel Works, the Yawata district, and the policy changed.
The deciding factors for adoption were FLEXSCHE's open stance and GUI
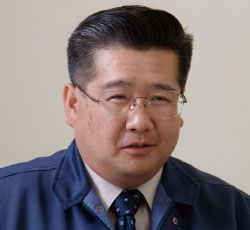
Nippon Steel Solutions Corporation
Steel Solutions Division
Kitakyushu System Center
Steel 3 Group
Mr. Satoshi Miyamoto
In fact, the Yawata district also had a high level of technical capability, having "built most of the systems in-house" until then, and had developed the conventional production scheduling system in-house. However, developing a user-friendly scheduler entirely in-house was inefficient, and after careful consideration over time, it was decided to develop based on package software. After careful selection based on extensive experience in developing scheduling systems, FLEXSCHE was chosen.
Since the situation of the transportation scheduling system in the Tobata district was similar to that in the Yawata district, the use of package software was considered a realistic option. Of course, at that point, FLEXSCHE was merely one of the candidates. Other schedulers from different companies were thoroughly investigated, materials were obtained, and inquiries were made. After further consideration, the final choice of FLEXSCHE, like in the Yawata district, was due to two major reasons, both of which were fundamentally common with the Yawata district.
"Creating a user interface in-house is a very labor-intensive task. It takes months of time, and even if it is completed, achieving sufficient operability is extremely difficult. In such a situation, FLEXSCHE already has an excellent GUI prepared, and we can also extend it. This alone saves a considerable amount of effort and time and matches our needs. This was a very significant point in choosing it."
Another reason was that FLEXSCHE is a flexible package software. "When creating from scratch, there is too much freedom, leading to a flood of individual opinions, making it difficult to move forward. However, when using package software, there is already something that works in front of you, so you try to do what you can within it, allowing for grounded discussions. The existing functions provide moderate restrictions, encouraging the generation of unified ideas. The reason for choosing FLEXSCHE among many package software options is because the content of the software is open. Other companies' schedulers are black-boxed and not shown. However, FLEXSCHE Corporation opens up the models and logic, and programming is possible. It was possible to judge whether the scheduler we desired could be realized."
Thus, following the manufacturing scheduling system in the Yawata district, FLEXSCHE was also introduced to the transportation planning system in the Tobata district.
Utilizing high technology to continuously add functions in-house
Of course, since it was the first time using FLEXSCHE, it was actually difficult to determine the range of what could be done independently, and initially, the possibility of requesting part of the development from FLEXSCHE Corporation was also considered, and opportunities were arranged to consult with FLEXSCHE engineers about specific specifications.
However, as they became more familiar with FLEXSCHE, they became confident that they could freely construct the desired system by fully reflecting Nippon Steel Solutions' high technical capabilities and experience, and a development team of 5 to 6 members was formed to engage in full-scale development.
However, before that, several obstacles stood in the way. One of them was how to incorporate the accumulated scheduling know-how into the scheduler. "Employees with decades of experience each had their own know-how for scheduling, along with their own constraints and commitments. To incorporate this into the scheduler, we started by taking the time to interview each person and objectify their knowledge. However, incorporating all the know-how sometimes led to contradictions or lack of smooth integration, so we aimed for a certain level of standardization while incorporating it as logic. I think it would be difficult to incorporate this into a general package software, but thanks to the flexibility of FLEXSCHE, we were able to incorporate almost everything."
And the biggest challenge was the coordination of the three schedules: "Product Warehouse," "Carrier," and "Wharf." "Each of the three schedules had different resources, and even each product warehouse had its own individual constraints. We programmed to manage and coordinate these online. What helped us in this process was the functionality and data structure of FLEXSCHE. Because it had abundant features, we didn't have to spend much effort creating our own, and structurally, we only needed to process the outside while keeping the data inside as it was, which significantly reduced the time that would normally be required for such a task."
We also programmed to extend the user interface and logic of FLEXSCHE, which allowed us to faithfully meet user demands. "We tweaked everything we could ourselves."
Promoting online integration with the introduction of Communicator
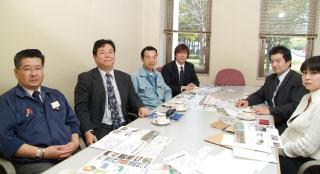
"In the past, when there were changes to the plan, we sent them by fax, but as plans change constantly, discrepancies inevitably stood out. With FLEXSCHE Viewer, the latest plans can be displayed in real-time, so we thought it would allow us to respond quickly to plan changes. Another important aspect is providing a sense of assurance to the field. Previously, even if scheduling instructions were given, the field often changed the order if they were not convinced. However, with the Viewer, we can now provide an objective reason for 'adhering to delivery dates,' so I believe those receiving instructions will accept them more readily. Of course, it will also undoubtedly make it easier for those scheduling to give instructions."
Currently, six FLEXSCHE Viewers have been introduced in the Tobata district's transportation line, further promoting real-time online integration, with the ultimate goal of bringing work instructions closer to automation.
"Since President Urano is here, I would like to make a request: as platforms continue to evolve, I hope we can always continue to use FLEXSCHE in the latest environments. I also have high expectations for FLEXSCHE Communicator, which allows real-time access to various scheduling data. I believe it will make it easier to build a dynamic scheduling system, which has been difficult to achieve until now. Please continue to develop software that benefits us in the future."
Overview of the implementing company
Nippon Steel Corporation
Head Office | 2-6-3 Otemachi, Chiyoda-ku, Tokyo |
---|---|
URL | |
Established | Showa 45 (1970) |
Business Description | Steelmaking, engineering, urban development, power, chemicals, new materials, and non-ferrous materials businesses, etc. |
Sales | 2.1478 trillion yen (standalone, fiscal year 2004) |
Listed | Listed on the First Section of the Tokyo Stock Exchange, Osaka Stock Exchange, Nagoya Stock Exchange, Sapporo, and Fukuoka |
Number of Employees | 20,454 employees |
Features | Ranked 3rd in the world for crude steel production. |