Addressing the issue of reverse phenomena, significantly reducing planning time
Realizing planning by multiple people with FLEXSCHE Communicator
Yamagata 3M Co., Ltd. Materials
- Created in June 2008
- Download PDF for Display
- Download PDF for Printing
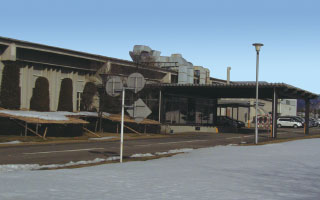
Yamagata 3M Co., Ltd.
Surrounded by mountains on all sides, Higashine City in Yamagata Prefecture. From the tranquil cherry-producing region to the world, Yamagata 3M, a part of the Sumitomo 3M Group, serves as one of the largest manufacturing bases of the global company 3M, delivering a diverse range of products that add value to life and business.
The Graphics Products Manufacturing Department at Yamagata 3M handles approximately 10,000 items, and due to the premise of inventory, changes to the production schedule based on demand forecasts are frequent. As a result, temporal reverse phenomena of orders and processes often occur, and there were limitations with simple scheduling using Excel and other tools.
The department considered multiple schedulers and conducted benchmark tests. As a result, FLEXSCHE was adopted. With the adoption of FLEXSCHE, reverse phenomena and scheduling time were significantly reduced, and due to the ease of management on the screen, it has become an "indispensable presence" for the department.
Challenging the efficiency of production planning in the era of high-mix low-volume
As the era of high-mix low-volume progresses, production planning is becoming increasingly complex. Improving its efficiency is closely related to the growth of companies. 3M, a world-leading multinational company (USA) that advocates "developing products that do not exist in the world," handles over 50,000 types of products. For Yamagata 3M, a manufacturing base in 3M's global network, improving the efficiency of production planning in the era of high-mix low-volume is one of the important management challenges.
1970Year、3MProductのDay本国内での販売、製造to行っている住友スリーエムグループにおける国内製造拠点andして山形スリーエムはスタート。徹底した品質管理、Latest製造ライン、高度に標準化された作業のもand、3MProductの国産化はもandより、海外3M各社へProductto供給I do.3Mではポスト・イット®Productandスコッチ®粘着テープandいった身近なProductのほか、電力、通信、建築、Automobiles、交通Yas全、ヘルスケアand、様々な産業分野に対し革新的なProductto提供I do.
Numerical targets are set for the introduction of new products, and innovation is the driving force behind 3M's growth. On the other hand, the manufacturing sites that support innovation are increasingly demanding short delivery times and high-mix low-volume production.
"Around 1995, we felt the limitations of human-based schedule creation and searched for a scheduling system, but at that time, there was nothing that could cover thousands of types of products," recalls Takeshi Watanabe, manager of the Graphics Products Manufacturing Department.
The products handled by the Graphics Products Manufacturing Department are diverse, including sign and display-related films (Scotchcal™), decorative films (wall materials) used as interior materials for buildings, hotels, and apartments, glass films for sunlight adjustment and shatter prevention, films replacing black paint for automobiles, and reflective sheets for traffic signs.
"At that time, we responded by creating schedules with Excel and standardizing operations, but as high-mix low-volume production accelerated, there were limitations with human-centered scheduling," says Watanabe. It took nearly ten years for the era to catch up with the scheduling system sought by the department.
Ultimately choosing FLEXSCHE based on benchmark test results
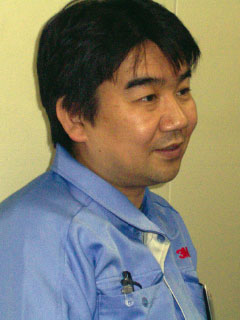
Graphics Products Manufacturing Department
Manager
(Manufacturing Planning Group Leader)
Takeshi Watanabe
"There are over 500 types of decorative films (wall materials) alone. Our department handles thousands of products and up to 10,000 items, with inventory as a basic premise. For example, if the wall material desired by the customer is out of stock, the customer's attention will shift to other companies, resulting in a missed business opportunity. Production is based on demand forecasts, but changes are frequent due to changes in the business environment," explains Watanabe about the background of the introduction.
The most troubling issue was the reverse phenomena. Kenji Takahashi from the department explains, "We produce products in layers with machines that support high-mix low-volume production, but even with the same machine, conditions such as temperature and pressure vary depending on the product. Since it operates 24/7 without stopping, even a slight mistake can cause the schedule to reverse."
For example, changes are made to the schedule due to various requirements such as "did not meet the specified quality," "material delivery is delayed," or "sudden change in demand." "Due to frequent changes and the large number of items, omissions in responding to changes inevitably occur. When reverse phenomena occur, it is difficult to keep up with human-based schedule management," says Takahashi.
In June 2004, the department once again began considering the introduction of a scheduling system. "At the stage of requesting materials, we narrowed it down to about 18 companies, and finally asked three companies to make presentations," says Takahashi. Regarding the points of adoption, Takahashi reveals, "At the stage of listening to reviews, other companies were rated higher, but when we conducted benchmark tests with the same data, FLEXSCHE produced satisfactory results. It also matched our company's needs, which were only seeking the scheduling part."
"Looking back now," Watanabe continues, "I think it was significant that I talked with the person in charge of FLEXSCHE when I first encountered it at an exhibition. We were looking for something advanced at the time, and as we talked, I got the impression that our ideas were aligned, which gave me a sense of reassurance."
The impression turned into conviction as we proceeded with the actual implementation. "If it takes tens of minutes to get an answer after making schedule changes, it's unusable. We received advice on making the product combination compact to enable instant change response, and also on speeding up the search logic," said Mr. Watanabe.
Innovative use of FLEXSCHE to accommodate frequent changes
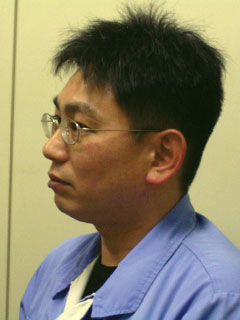
Graphics Products Manufacturing Department
Manufacturing Planning Group
Mr. Kenji Takahashi
In September 2004, the decision to adopt FLEXSCHE was made, and delivery was completed in November of the same year. Full operation began in May 2005. The most challenging aspect was the data migration work. "From January to April is our busy season. It was difficult to migrate data while keeping operations running. We managed to cope with the support of two members from the headquarters IT department," said Mr. Takahashi.
Mr. Watanabe evaluates the fact that full operation was achieved in about six months from introduction as follows: "The fact that we were able to operate in about six months with thorough preparation is thanks to the efforts of Takahashi and the support staff from the headquarters IT department, as well as the support from FLEXSCHE Corporation." The second phase of the required quantity calculation system went into full operation in 2000, and the organization of the master data, such as BOMs and routes necessary for scheduling, was completed, which also contributed to the rapid operation.
The scheduling system centered on FLEXSCHE is integrated with core systems such as the order management system and the required quantity calculation system. Necessary data is loaded into FLEXSCHE to create schedules and issue work instructions. Furthermore, the created schedule is batch processed into the core system. Completed manufacturing operations are entered into the core system once a day, and then imported into FLEXSCHE.
The schedule range is as long as one week and as short as three days. Management with FLEXSCHE is about one month. Even after presenting it to the site, the department is innovating the use of FLEXSCHE to accommodate schedule changes, which occur about 5 to 6 times a week.
"First, we avoid looking at inventory in FLEXSCHE. Necessary materials are arranged through the required quantity calculation system. In reality, there are cases where this is not the case, but if we put each of these into FLEXSCHE, it could cause confusion. We only put into FLEXSCHE what we are confident can be produced," said Mr. Watanabe.
Even when there is a loss during production, "For example, if only 50 can be made where 100 should be, the subsequent process continues to manufacture for 50, and a new order is placed for the missing 50. We created a system where the next process is aligned with the quantity of the previous process as a principle," said Mr. Watanabe.
The schedule presented to the site is frozen on FLEXSCHE, and in case of changes, "Currently, we make changes manually. At that time, we added a function that allows us to move in block units to make it easier to work," said Mr. Takahashi.
The reversal phenomenon has significantly decreased, and the effect is substantial in production management as well.
In 1995, most of what we wanted to achieve with the scheduling system was realized. Regarding the actual effects after implementation, Mr. Watanabe says, "The biggest effect is that the reversal phenomenon no longer occurs frequently as it used to. Nighttime calls have decreased, and calls on holidays have almost disappeared. Even though equipment increased right after the introduction, I can handle scheduling alone without any problems."
The time required for schedule creation has also been significantly reduced. "Previously, input for schedule creation was labor-intensive, but by utilizing FLEXSCHE, necessary data is automatically inputted in bulk, and with automatic scheduling, significant operational efficiency was achieved. If we can automate automatic scheduling as desired in the future, it will become the ideal scheduling system," said Mr. Takahashi.
There were also significant benefits in the management aspect of production planning. "If the production quantity is less than planned, a message is displayed, making it immediately clear on the Gantt chart which operation's order it is. It is very easy to understand and easy to take the next action. The operation viewer is also very convenient. It shows how many operations there are for one order. Especially for new products, there are cases where it is not a single sequence, making it difficult to understand, but the operation viewer allows for visual understanding. If we set the display ourselves, we can freely search by date, machine, etc. The ability to instantly check 'What is the next process?' and 'What is the previous process?' on the screen is a significant advantage," said Mr. Takahashi.
Regarding future developments, Mr. Watanabe says, "This time, we introduced FLEXSCHECommunicator, which allows multiple planning personnel to collaborate on planning and data maintenance. From April 2008, we will implement a system where management can be shared between one or two people besides Takahashi. We consider the scheduling system to be the pinnacle system within our manufacturing system. Therefore, as the surrounding systems are upgraded, the next form of the scheduling system will become apparent. In any case, it is an indispensable system now," he says emphatically.
Overview of the implementing company
Yamagata 3M Co., Ltd.
Headquarters and Factory | 5500 Wakagi, Higashine City, Yamagata Prefecture |
---|---|
Established | March 24, 1970 |
Capital | 360 million yen |
Business Description | Manufacture and research and development of reflective material products, adhesive films for interior and exterior decoration, adhesive films for stripes, non-woven fabrics, abrasive products, household nylon scrubs, connectors, electrical products, double-sided adhesive tapes, thermal insulation materials for clothing, optical films, and other products. |
URL |