Aiming to halve manufacturing lead time by implementing FLEXSCHE
Eliminate discrepancies between plans formulated with FLEXSCHE and the actual site to achieve goals
Eastern Co., Ltd. Electronic equipment
- Created in October 2013
- Download PDF for Display
- Download PDF for Printing
Eastern, an electronic component manufacturer highly evaluated for its technological capabilities by semiconductor manufacturers worldwide. Under the management policy of prioritizing customers, the company strives to respond quickly to customer requests, and at the end of 2009, the president's policy of halving the manufacturing lead time (from 3 weeks to 1.5 weeks for the company's standard model) was presented. At that time, planning was done manually using Microsoft Excel, but only about 30% of the products could be planned, and the introduction of a scheduler was essential to halve the manufacturing lead time.
We decided to implement a two-phase introduction, with the first phase focusing on NC processes and the second phase expanding to all processes. After evaluating multiple production schedulers, at that time, only FLEXSCHE was able to meet the complex constraints of NC processes. After implementation, the planning work time was significantly reduced from a total of 840 hours per month to 20 hours per month. We also installed work instruction monitors at each process to share information such as progress status. By visualizing the site, we are also working to reduce work-in-process inventory. Currently, we are working on business improvements to strengthen analysis functions for actual data and to eliminate discrepancies between planning and the site using FLEXSCHE.
At the end of 2009, the company aimed to halve the manufacturing lead time as per the president's policy.
Located less than 10 km southeast of Lake Suwa, at the foot of the Yatsugatake Mountains, is the headquarters and factory of Eastern, an electronic component manufacturer highly regarded for its technological prowess by semiconductor manufacturers worldwide. The company is engaged in the package substrate business and the power systems business, including power supply devices.
The semiconductor package printed circuit boards manufactured by the company are used in globally renowned smartphones and tablets. As products become thinner and more functional, the demand for the company's high-density, high-precision semiconductor technology, which is its strength, is increasing even more.
Since its establishment in 1961, the company's history has been one of challenging pioneering technologies of the time, such as solder plating through-hole technology, chip-on-board technology, multi-chip module technology, and the thinning of rigid substrates. In February 2013, the company entered into a capital and business alliance with NGK Spark Plug Co., Ltd. to strengthen its package substrate business.
Currently, with 80% of sales coming from overseas, the company, which is committed to manufacturing in Japan to win in global competition, strives to improve customer satisfaction under a customer-first management policy. In the semiconductor-related industry, responding quickly to customer requests is essential for building trust with customers and continuing to receive stable orders.
"In the increasingly competitive semiconductor industry, development speed leads to competitiveness. As part of supporting our customers' development, we established the Blue Commando, an express prototype manufacturing team, 10 years ago to achieve ultra-short delivery times for prototypes. Additionally, at the end of 2009, the president's policy to halve the manufacturing lead time was presented. Given the increasing demand for short delivery times, I think it was a very foresighted management decision," says Mr. Fukumoto, Manager of the Production Management Department, Production Management Center, Package Substrate Division.
Only FLEXSCHE was able to meet the constraints of NC processes.
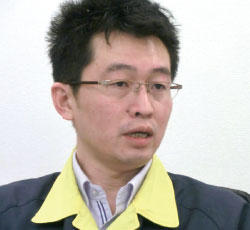
Package Substrate Division
Production Management Center
Manager of Production Management Department, Mr. Fukumoto
Before 2009, all production planning at the company was done manually using Microsoft Excel, one process at a time. However, with approximately 2,000 lots constantly flowing as 100 workpieces per lot, it was difficult to plan for all lots, and only about 30% of the schedules could be created. Moreover, the plans made did not consider process load and simply indicated completion times, often resulting in cases where work could not be completed at the scheduled time if there were conflicts. Plan changes also required a tremendous amount of effort and time, as progress management was done by filling in Microsoft Excel.
"At that time, the goal of halving the manufacturing lead time was to reduce it from about 3 weeks to 1.5 weeks. It was an impossible goal to achieve manually," recalls Mr. Fukumoto.
Reducing work-in-process inventory also became a challenge in shortening manufacturing lead time. "We anticipated situations where lots would not come in due to troubles in upstream processes, and at that time, we accumulated work-in-process inventory in many processes, including those with delivery times exceeding 6 weeks. While work-in-process is necessary from the perspective of effective use of manpower and prioritizing delivery times, there was no information to determine appropriate work-in-process, and it was difficult to grasp the status of processes, such as machine availability," says Mr. Koji Ito, Manager of the Production Management Section, Production Management Department, Production Management Center, Package Substrate Division.
To solve these issues, we decided to consider a production scheduler that automatically plans while considering process load. The System Management Department and Kissei Comtec, which supports the company's system development and operation, took the lead in this consideration. Kissei Comtec, a system integrator based in Nagano and Tokyo, has been providing various technical support to the company for over 10 years, including the introduction of a production management system, under a strong trust relationship.
This introduction was decided to be carried out in two phases, with the first phase targeting NC processes and the second phase expanding to all processes. There was also an aim to enhance NC processes first, as they have high work costs and expensive materials.
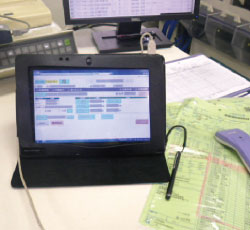
Regarding the background of adopting the scheduler, Mr. Michihiko Higuchi, Senior Manager of the System Management Department, Management Headquarters, says, "We participated in a FLEXSCHE seminar with Kissei Comtec. We had previously introduced a simple scheduler from another company, but compared to that, FLEXSCHE left a strong impression with its high operability and functionality. The first phase, the NC process, involves drilling holes to conduct patterns on printed circuit boards. The processing time varies greatly depending on the product, with some products requiring 400,000 holes to be drilled in 12 hours, while others are completed in 20 minutes. Only FLEXSCHE was able to meet the complex constraints of NC processes."
Work instruction monitors were installed at each process to share progress status.
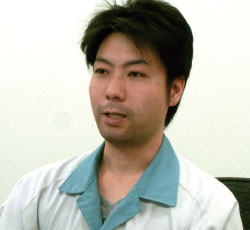
Package Substrate Division
Production Management Center
Manager of Production Management Section, Mr. Koji Ito
We started considering the scheduler in April 2010 and decided to adopt FLEXSCHE in August 2010. We took time to prepare until the full operation in October 2011.
"With a 50-year history, it took time to explain and gain understanding from the site. While explaining the company's policy, we also made theoretical explanations, saying, 'Until now, plans have been made based on the experience of the production management department's staff, but from now on, the system called the scheduler will automatically calculate plans based on what needs to be done to meet delivery times,' and we worked to gain their understanding," says Mr. Ito.
There were also system-related challenges in introducing the scheduler. "The master was not yet organized, so we worked to convert operations into data with the cooperation of the site. Also, when explaining the necessity of the scheduler to the site, they perceived that everything would be okay if FLEXSCHE was introduced, but we couldn't reduce daily production just because it was a transitional period for system introduction. It was difficult to gain understanding on that point," says Mr. Hirokazu Ushiyama, Chief of the System Management Department, Management Headquarters. Regarding operational challenges at the start, Mr. Ito says, "There were delays in upstream processes, and there were times when products did not come in as planned with FLEXSCHE. We adjusted operational rules to ensure that plans could proceed without confusion on the site."
Planning is done by incorporating master information and lot information from the production management system, as well as actual data from the operation result collection system into FLEXSCHE. Previously, work instructions were given once a day on paper, but now work instruction monitors are installed at each process to display the planned work and its progress status planned by FLEXSCHE. Information is updated every two and a half minutes, and progress status is shared by displaying delays in red. In the NC process, a large monitor is suspended from the ceiling, making delays in upstream processes immediately apparent.
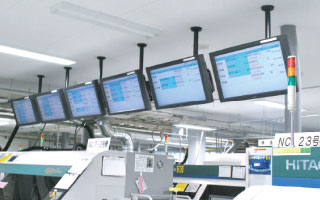
"Kissei Comtec provided invaluable support not only in development and construction but also in adjusting rules at the start, helping us greatly when we faced difficulties. They also implemented our production management system and operation result collection system, which facilitated smooth integration with FLEXSCHE," said Mr. Ushiyama.
Eliminating the gap between FLEXSCHE solutions and on-site operations is the next theme.
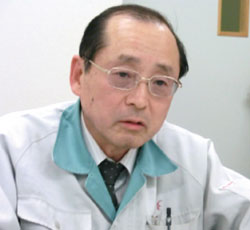
Management Division
System Management Department, Councilor Michihiko Higuchi
Currently, operations are running smoothly, and the rollout to all processes in the second phase is complete. The benefits of the implementation are steadily appearing. In terms of reducing work-in-process inventory, it is now possible to visually understand the processing time per lot and whether everything in progress will be completed today, leading to the suppression of unnecessary work-in-process.
Significant effects have been achieved in shortening planned working hours. "Previously, three people were responsible for production planning, which occupied most of the monthly working hours. Even after spending considerable time on planning, delays and changes occurred, and the volume of rescheduling work was enormous. Now, including rescheduling tasks, one person handles it in one hour a day, totaling 20 hours a month. The focus has shifted from creating plans to improving the accuracy of plans," said Mr. Ito.
Efforts to shorten manufacturing lead time have also progressed. "Our products go through an average of 70 processes before completion. To finish in 1.5 weeks, we need to move three processes a day. With FLEXSCHE, we can plan for all processes and lots, making it possible to achieve shorter manufacturing lead times by executing according to the plan. Additionally, the ability to quickly reschedule in response to delays or changes and display updated information on monitors at each process has greatly facilitated information sharing with the site," said Mr. Fukumoto.
However, the current situation is that delays occur in on-site operations, not following the plans made with FLEXSCHE. Factors causing delays, such as "lack of materials" and "consideration of changeovers," are being identified, and eliminating the gap between FLEXSCHE solutions and on-site operations is the theme of the third phase. To achieve this, we plan to enhance the analysis functions of various data, including actual performance data.
Additionally, during the second phase, simulation functions were added, allowing simulations other than the lots being processed to be conducted with FLEXSCHE.
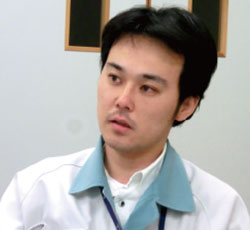
Management Division
System Management Department, Chief Hirokazu Ushiyama
"We aim to utilize simulations for optimizing personnel allocation and equipment investment. Providing information to support management decisions is also a crucial role of the production management department. We want to maximize the use of FLEXSCHE's functions to contribute to management. I would like to incorporate all the know-how I have accumulated over the years in production management. In the future, rather than using external packages, we want to evolve our system centered on FLEXSCHE by determining what and how to input to improve the accuracy of planning," said Mr. Fukumoto.
Eastern aims for further leaps with high technical capabilities and thorough production management in the global semiconductor market. Expectations for FLEXSCHE, which supports the company's growth, are rising daily.
Partner's Voice
Our company had previously introduced a simple scheduler software from another company, but it lacked functionality for use with Eastern. Therefore, we investigated market scheduler software with the customer and ultimately selected FLEXSCHE. One of the good points of FLEXSCHE is its operability. Tasks such as moving and checking planned operations, centered on mouse operations, are very easy. Also, the ability to define flexible scheduling rules using formulas makes it a product that can sufficiently meet the future needs of customers with many processes and short product life cycles.
Since it was our first introduction, we honestly faced many challenges, but thanks to the efforts of everyone involved in the Eastern project and the prompt support from FLEXSCHE Corporation, we were deeply moved when it successfully went live.
Currently, we have built a series of process management systems, including a work result collection system using tablet devices and handheld terminals centered on FLEXSCHE, and visualization of work instruction monitors on-site, but challenges remain. We will continue to work hard to build better systems that contribute to our customers' operations in cooperation with them.
Overview of the implementing company
Eastern Co., Ltd.
Established | February 1961 |
---|---|
Head Office | 1-8-37 Tsukahara, Chino City, Nagano Prefecture |
Capital | 4,636 million yen |
Number of Employees | 695 employees (non-consolidated), 1,095 employees (consolidated) *As of the end of March 2013 |
Business Description | Manufacture and sale of semiconductor package substrates/electronic devices such as power supplies |