Confusion in the field due to rapid production increase, increase in the number of parts, and production changes
Bottom-up introduction of FLEXSCHE into the scheduler
Kyowa Seiki Co., Ltd. Equipment and Machinery
- Created in May 2007
- Download PDF for Display
- Download PDF for Printing
Kyowa Seiki Co., Ltd., which manufactures offset printing machines, has been experiencing steady growth with sales of 5 billion yen in fiscal 2005 and 7.5 billion yen in fiscal 2006. On the other hand, the rapid increase in production, increase in the number of parts, and production changes have made it difficult to grasp the overall situation in the manufacturing field, leading to makeshift responses and a significant amount of waste, highlighting serious challenges.
In an effort to overcome these challenges, the need for a scheduler was strongly felt in the field. After seeing a demo of FLEXSCHE conducted by the company, the person in charge was convinced, "This is it!" With strong support from the field, it was decided to introduce it in three locations: the head office processing section, Motoyama plant, and assembly. The company's new challenge to achieve total lead time reduction by realizing strong scheduling and process visualization has begun.
Manufacturing sites struggling to cope with rapid production increases
Fuchu City, located in the southeast of Hiroshima Prefecture, is surrounded by small mountains on three sides. It is home to many companies, including Ryobi Co., Ltd., a world-leading die-casting manufacturer, which originated in this area and still has its headquarters here. The city, rich in greenery, is alive with the spirit of challenge from unique companies.
Established in 1952, Kyowa Seiki started as a processing plant for Ryobi's die-cast products. Later, it cooperated in the launch of Ryobi's globally recognized offset printing machines, and now, the manufacturing of offset printing machines has become Kyowa Seiki's main business. The company's products include the medium-sized 78 series, the small 52 series (single-color, two-color, four-color, and more), and products with added optional functions. Ryobi handles design, production planning, and sales, while Kyowa Seiki supports the business with a consistent system from material procurement to manufacturing and assembly. Its high technology and quality are the sources of its competitiveness in the global market.
The company achieved its sales target of 5 billion yen in fiscal 2005, which was a management goal. Furthermore, it continued to grow rapidly, reaching 7.5 billion yen in fiscal 2006. However, three years ago, it was "at the bottom," says Executive Director Mr. Arita. "At that time, we were producing about 20 units per month, and the workforce was reduced by about 60 people to around 110. Now, we produce about 50 units per month, and the workforce, including temporary staff, has more than doubled to 234, and we have added one more line. It's as if the slump three years ago was a lie," says Mr. Arita.
However, this rapid increase in production also became a major cause of confusion in the manufacturing field. As the factory struggled to cope with daily demands, a lot of waste occurred, and various issues emerged.
Scheduling by human hands has reached its limit
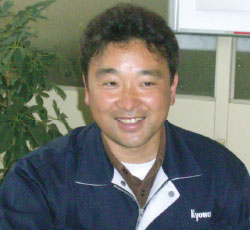
Executive Director Mitsunori Arita
Not only has the production volume increased, but the number of parts has also continued to grow due to the diversification into small-lot production, reaching 55,000 parts in total. Amidst this situation, production changes further complicate the problem. "We accept production changes even while the line is running. The issue is that a change in one part can affect other parts. For example, changing from 10 to 12 units may require reducing another part from 10 to 8 units, which happens quite often. Changes to the paper discharge stand, for instance, can alter the structure itself," says Mr. Arita.
The impact of production changes has brought a serious situation to the headquarters processing section, which handles many small items. "Small items are difficult to manage just because they are small, and when there are production changes, we completely lose track of how much work-in-progress there is in each process and which orders are currently being produced, leading to makeshift responses," explains Mr. Takahashi from the headquarters processing section.
Mr. Oda from the Motoyama factory also points out issues from a different perspective. "When you draw and erase lines on the diagram, thinking about the next setup, such as moving from this machine to the next and then back to the original machine, there is a tendency to overproduce," he notes.
In addition to the challenges faced by the factory, the pressure for shorter delivery times is increasing. "With the increase in production volume, number of parts, equipment, and personnel, we can no longer plan by drawing lines with a pencil as we used to. We don't have the time or mental capacity to manually re-plan when there are production changes. However, proper planning is essential for delivery management and progress tracking," says Mr. Oda.
Matched with what we envisioned, felt it during the demo
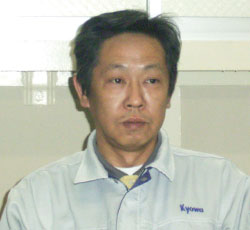
Processing Department, Motoyama Processing Section
Section Manager, Tsuyoshi Oda
To break through the current situation, Mr. Oda began creating a scheduling tool based on Excel management. Around that time, a demo of FLEXSCHE was conducted by the integrator ACT Corporation at the company.
"I was first surprised by the operability and flexibility of FLEXSCHE. It allows for flexible scheduling without having to intervene in production changes, everyone can see the schedule up to about three days ahead, and work instructions can be easily issued. It was exactly the product I had envisioned." Feeling this, Mr. Oda requested ACT to create a sample using actual data. A few days later, seeing the sample, Mr. Oda's feeling turned into conviction. Mr. Takahashi also had high expectations for the flexibility of FLEXSCHE from the explanation during the demo.
However, there was another hurdle to overcome for the introduction. The management's priority was to get the previously introduced production management system, which was at a standstill, up and running. One major reason for the halt was attempting to execute process management, which should be done by a scheduler, with the production management system.
"The production management system is used for parts procurement, but what the site really needs is a scheduler," was the earnest voice from the field that moved the management. As a result of this bottom-up approach, the introduction of FLEXSCHE was decided for three locations: the headquarters processing section, the Motoyama factory, and the assembly section.
The main goal is to shorten lead times
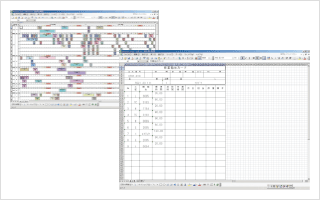
Processing Schedule and Work Instructions
Beyond solving current issues, the main goal of introducing FLEXSCHE is to shorten lead times. Mr. Oda from the Motoyama factory, who is leading the introduction of FLEXSCHE, identified the following three points to achieve lead time reduction.
- Visualization of Processes
- Efficiency Improvement
- Seamless Integration of Processing, Assembly, and Shipping
In the visualization of processes, not only the confirmation of work and setup aspects but also the sharing of information becomes important. "Not only my work but also what I should be doing now and what I need to do next within the overall process schedule becomes clear at a glance. We asked ACT to create a processing schedule that matches our company's format. This allows for information sharing and leads to a change in awareness by recognizing one's role," says Mr. Oda.
The work instructions presented along with the processing schedule come in two types: blue and white. The blue slip covers all processes, while the white slip details each process, including delivery dates, and the system is designed to input the results into FLEXSCHE once the work is completed. "By inputting the results, the difference between the plan and the actual results becomes visible. Why didn't it go according to plan? This awareness leads to identifying and addressing issues one by one, which contributes to efficiency improvement," says Mr. Oda.
One of the factors causing waste, overproduction, is addressed by basing it on the assembly order, and further achieving efficient scheduling by reducing machine downtime. However, there were cases where making everything follow the assembly order hindered efficiency. "Especially for small items, it is necessary to produce them in batches. Therefore, we have a two-stage structure where production is batched up to a certain process, and then follows the assembly order," says Mr. Oda.
The company aims to achieve seamless integration of processing, assembly, and shipping in the future, with a focus on total lead time reduction. "By making it possible to work backward from the delivery date, not only can delivery management be thoroughly enforced, but previously unseen issues such as work-in-progress stagnation can also be identified. This leads to further improvements in balancing the overall process," says Mr. Oda.
Realizing what we truly want to do
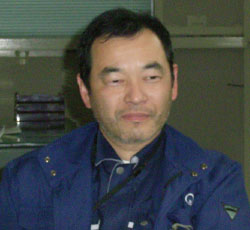
Processing Department, Processing Section, Processing Unit 1
Unit Leader, Takeshi Takahashi
The decision to introduce FLEXSCHE was made at the end of December 2006, and a test run simulating actual operations began at the Motoyama factory in February 2007, with some parts already in operation. Final adjustments are being made for full operation after the Golden Week holidays.
"As we progressed with the test run, we thought, 'We can do this too.' We are consulting with ACT on various matters. The ability to realize what we truly want to do is also an attraction of FLEXSCHE. We are currently working on linking parts with parts, and once this is completed, we will finally move to full operation," says Mr. Oda confidently.
The efficiency of scheduling creation has also improved. "Tasks that used to take a whole day can now be done with the push of a button with FLEXSCHE. Once you get used to the operation, there is nothing particularly difficult," says Mr. Goto from the Motoyama factory with a smile. By exporting the required number of parts for the month from the sales management system running on the office computer to Excel and importing it, orders can be created in FLEXSCHE. The ability to automatically create orders due to the large number of parts significantly reduces time.
Regarding orders, the headquarters processing section is also making efforts to adapt to the current situation. "Especially for small items, responding to production changes is very complex, involving machines, people, delivery dates, and the relationship with material linkage. Considering the current response, we are testing a system where order quantities, delivery dates, and minimum stock of materials are variable. We will also proceed with pattern analysis in the future to pursue scheduling efficiency. FLEXSCHE's performance is excellent, so it's easy to try various changes to orders," says Mr. Takahashi.
Expectations for contributions to profitability through efficiency improvement
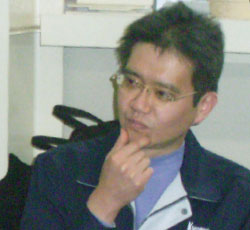
Processing Department, Motoyama Processing Section
Chief, Hiromitsu Goto
Since the introduction was driven by a bottom-up approach, results are more demanded from the field. Therefore, getting it running is the top priority. "We are very grateful for ACT's support, not only in responding to phone calls but also in visiting us multiple times. I think the progress towards full operation is going very smoothly," says Mr. Oda, highly appreciating the support aspect.
Regarding one of the future challenges, the penetration among workers, "We would like to gradually achieve this while operating" (Mr. Goto). Additionally, the introduction of barcodes is being considered to improve the efficiency of inputting results.
In the company, there are 20 processes in the factory and 50 in assembly, with an average lead time of about 5 months. Of this lead time, the Motoyama factory accounts for about 2.5 months, and the factory aims to shorten this by half a month. "Eliminating small wastes leads to significant improvements. Our company actively engages in improvement proposal activities, and visualization through the processing schedule is also expected to invigorate these activities" (Mr. Oda).
As a future development, we are considering utilizing the production management system for parts procurement and strengthening production management by linking it with FLEXSCHE. The introduction of FLEXSCHE has also provided a direction for future efficiency improvements.
"Overall, there is a trend towards increased production, and improving efficiency will also increase profits. We have high expectations for the introduction of FLEXSCHE, not only for thorough due date management but also for contributing to profits. Additionally, to respond to market changes and achieve continuous corporate growth, the high flexibility of FLEXSCHE is extremely important for solving future challenges" (Mr. Arita).
Voices of Integrators
I remember feeling pleased when a person in charge at Kyowa Seiki said, "This is exactly the kind of scheduler we were looking for," when we showed them a demo of FLEXSCHE. I felt that they highly appreciated the operability and flexibility of FLEXSCHE.
We introduced FLEXSCHE to three departments: the Motoyama factory, the processing section, and the assembly section. Since the work content differs significantly even within the same company, we allocated sufficient meeting time for the introduction of FLEXSCHE. Seeing that the operation has started smoothly, I truly feel grateful to have been involved in this work. We made efforts to create forms familiar to our customers to ensure the smooth penetration of FLEXSCHE.
There are still challenges, but we would like to continue cooperating with the person in charge at Kyowa Seiki to build better systems and structures and contribute to improving business efficiency.
Overview of the implementing company
Kyowa Seiki Co., Ltd.
Head Office | 755, Mezakicho, Fuchu City, Hiroshima Prefecture |
---|---|
Motoyama Factory | 530-85, Motoyamacho, Fuchu City, Hiroshima Prefecture |
URL | |
Established | 1952 (Showa 33) |
Business Description | Manufacturing industry centered on offset printing machines |
Sales | 7.5 billion yen (Fiscal Year 2006) |
Number of Employees | 179 employees |