Introduced FLEXSCHE along with the renewal of the core system of the factory
Utilizing FLEXSCHE in three domestic factories
Sekisui Kasei Co., Ltd. Materials
- Produced in September 2014
- Download PDF for Display
- Download PDF for Printing
Sekisui Kasei Co., Ltd., a leading plastics solution company in Japan, is pursuing various initiatives under the "Sekisui Chemical Group 100-Year Vision" to achieve further growth and become a truly global company. As part of this, they decided to renew the core system of the factory and introduce a production scheduler to strengthen the management foundation and improve operational efficiency. By introducing the production scheduler, they aimed to solve issues in the process planning of each factory and link process planning information to the core system.
Previously, process planning was created using Excel, and incorporating it into the core system involved significant effort, resulting in the separation of process planning information and the production management system. The production scheduler was required to have "flexibility to meet business requirements," "ease of data integration with the new core system," and "usability surpassing Excel." After thorough consideration, the company highly evaluated FLEXSCHE for its excellent user interface, such as Gantt charts, ease of data integration, abundant standard features, and flexibility for free add-in development. They introduced FLEXSCHE to Sekisui Chemical Tenri, the company's Okayama manufacturing department, and Sekisui Chemical Kanto, aiming to introduce and expand it to overseas production bases based on the success know-how.
Trusted by customers globally
Aiming to become a plastics solution company
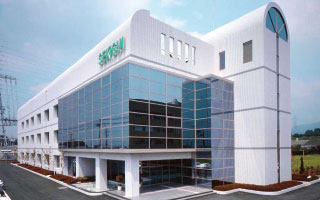
Sekisui Kasei Co., Ltd.
Expanded polystyrene, which contains a large amount of air and has low environmental impact, also features insulation and cushioning properties, making it widely used in fields such as food trays, cup noodle containers, fruit packs, packaging materials, and more. Founded in 1959, Sekisui Kasei Co., Ltd. is creating new added value by integrating advanced technologies based on world-class foamed plastics technology as a leading plastics solution company in Japan.
For example, Pioseran, born from the use of proprietary technology, is an excellent lightweight and cushioning automotive component, while Techpolymer, a spherical microparticle polymer, suppresses blue light by up to 60% and is used as an indispensable component in LCD displays. They are also actively developing products that contribute to environmental improvement, such as the reuse of used expanded polystyrene and plant-derived resin foams.
In 2009, marking its 50th anniversary, Sekisui Kasei Co., Ltd. formulated the "Sekisui Chemical Group 100-Year Vision" as a guide for further development. It presented a future vision of "aiming to become a plastics solution company trusted by customers globally," focusing on the human life (living) field, industry (industrial) field, and environment and energy field. They also set a goal to double the consolidated sales achieved in 2009 of 100 billion yen to 200 billion yen by 2019.
"Our company is implementing various measures to realize the '100-Year Vision,' such as accelerating global expansion and strengthening the management foundation. As part of this, the renewal of the core system of the factory, which had been in use for over 20 years and was becoming obsolete, became an important theme in the ICT strategy supporting business activities. Since it was the first renewal in 20 years, there were many business requirements to be systematized, resulting in a long-term project from 2006 to 2013," says Kazuo Yamashita, Chief of the Business System Group, Information Systems Department.
Integration with core systems, ease of use, and flexibility were key points for adopting FLEXSCHE
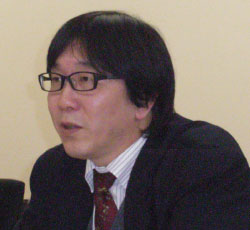
Management Strategy Headquarters Information Systems Department
Business System Group Chief
Kazuo Yamashita
The core system at Sekisui Chemical Group's factories is developed to support various operations (inventory management, warehousing management, cost management, etc.) of the factory. The traditional core system operated on a mainframe, but due to system obsolescence, it was decided to open up and completely renew the system. Additionally, automatically incorporating process planning information into the core system, which had been a challenge, was positioned as an important theme.
"Previously, each person in charge created process plans using Excel. There were various issues with systematically incorporating Excel data into the core system, and due to the vast amount of information, it was not possible to incorporate process planning information into the core system through manual input. As a result, process planning information could not be utilized in the production management system, and production results information was manually input into the core system for use in the production management system. To improve operational efficiency and effectively utilize the production management system, a mechanism to incorporate process planning information into the core system was required," says Mr. Yamashita.
Changes to process planning using Excel allowed each person in charge to freely adjust plans, but it inevitably took time and effort. As a result, it was not possible to quickly feedback plan change information to the field. Plan changes were communicated to the field by phone, leading to the risk of information not being accurately conveyed and mistakes occurring. Some factories independently built process planning systems, but they inevitably compared them to Excel, leading to complaints about "poor usability." Therefore, the company began considering the introduction of a production scheduler along with the renewal of the core system.
The company evaluated the production scheduler based on three points: 1. Flexibility to meet business requirements, 2. Ease of data integration with the new core system, and 3. Usability surpassing Excel. As a result, they adopted FLEXSCHE for the following reasons.
1. Flexibility to meet business requirements
The significant difference between FLEXSCHE and other products was its flexibility. "The flexibility inherent in FLEXSCHE minimizes customization and facilitates easy add-in development. Relying entirely on the developer for our unique business needs would be costly and time-consuming. We found no other product as flexible as FLEXSCHE for add-in development. With FLEXSCHE, we can quickly respond to requests from the field even after implementation. An example of an add-in developed by us is an input screen for entering instructions into the process chart used by the field," says Mr. Yamashita.
2. Ease of Data Integration with the New Core System
It was emphasized whether process planning information could be easily incorporated into the core system without using databases, and whether additional information could be easily integrated if needed. "FLEXSCHE provided a standard mechanism for data mapping with other systems. We appreciated the ability to easily incorporate process planning information into the core system without incurring labor costs," says Mr. Yamashita.
3. Usability Surpassing Excel
Since the introduction of the production scheduler meant discontinuing process planning using Excel, a level of freedom and operability surpassing Excel was required. "We highly valued FLEXSCHE's excellent user interface, which allows for smooth manual adjustments by dragging operations to any time or resource on the Gantt chart. It also enables flexible responses to process changes and quick feedback to the field," says Mr. Yamashita.
FLEXSCHE was introduced in three factories: Sekisui Plastics Tenri, the Okayama Manufacturing Department of the same company, and Sekisui Plastics Kanto.
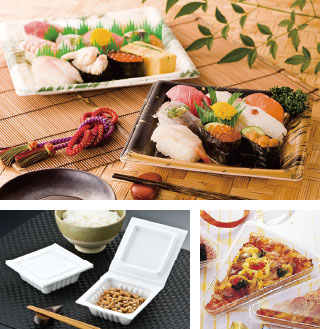
PSP Food Containers
The overhaul of the core system began in 2006 and was completed in 2013. FLEXSCHE was introduced to the PSP (Polystyrene Foam Sheet) production lines at Sekisui Plastics Tenri, the Okayama Manufacturing Department of the same company, and Sekisui Plastics Kanto.
Sekisui Plastics Industry has two main business pillars: PSP and EPS (Expandable Polystyrene Beads). PSP involves feeding polystyrene and a foaming agent into an extruder, extruding and foaming it into a cylindrical sheet using a mold, and creating cylindrical rolls over 100 meters long, with a thickness of 1mm to 3mm and a width of about 1 meter.
The PSP produced at the three factories where FLEXSCHE was introduced varies in size, color, and film application, with differences in the production process at each factory. "We are expanding to other factories using the FLEXSCHE introduced at Sekisui Plastics Tenri as a model. The basic stance is not to customize for each factory's unique requests, but in cases of 'absolutely necessary,' we develop add-ins for FLEXSCHE. Flexibility is crucial because 'absolutely necessary' situations inevitably arise when deploying a production scheduler across multiple factories."
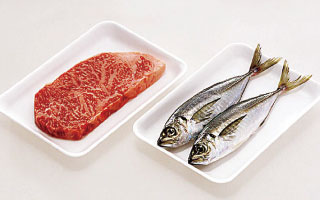
Eslen Sheet
Items to be produced, quantities, and dates are entered into FLEXSCHE as order data, which calculates process times based on quantities and allocates tasks to the production line. The process planning information created with FLEXSCHE is incorporated into the core system, and process charts and production instructions are printed and distributed to the production site. Even in cases of sudden plan changes, it is possible to quickly and accurately communicate the change results to the production site, helping to avoid risks such as errors.
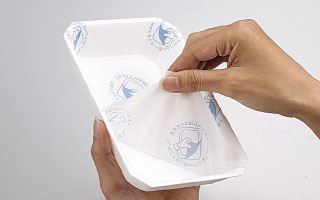
Removable Tray
Since process planning information can be automatically incorporated into the core system, it has become easier to effectively utilize process planning information in cost management. Regarding the ingenuity in linking with the core system, Mr. Yamashita says, "Due to our circumstances, unifying the product name master is not straightforward because of the large number of product types and the complex, company-wide involvement in operations. When introducing FLEXSCHE, we discussed various ways to use the product name master. Ultimately, we created a system that checks product names in both the core system and FLEXSCHE to prevent inconsistencies, and we are operating it."
Considering the Introduction of FLEXSCHE to Overseas Bases for Globalization
Regarding the future, "We cannot say that we are fully utilizing FLEXSCHE's inherent scheduling capabilities with our current use of FLEXSCHE. We plan to study FLEXSCHE more and broaden its application. Currently, we are not linking production performance information to FLEXSCHE, but we believe we must feed back production performance information to FLEXSCHE to improve production efficiency. In the future, we would like to conduct various simulations with FLEXSCHE based on various information and utilize it for raw material ordering," says Mr. Yamashita.
Having gained confidence from the introduction of FLEXSCHE, the company is also planning to introduce and expand it to overseas production bases. "Standardizing planning operations and moving away from reliance on individuals are important themes at overseas production bases as we advance globalization. Group company factories that mold intermediate materials like PSP and EPS into final products are also considering overhauling their core systems and are contemplating the introduction of FLEXSCHE."
Sekisui Plastics Industry, aiming for further leaps as a plastics solution company active on the global stage, will continue to contribute to improving the productivity of factories that support the company's challenges and growth.
Overview of the implementing company
Sekisui Kasei Co., Ltd.
Head Office | 2-4-4 Nishitenma, Kita-ku, Osaka City |
---|---|
Established | October 1, 1959 |
Capital | 16,533 million yen (as of March 31, 2014) |
Sales | 109,923 million yen (consolidated) (Fiscal Year 2014) |
Number of Employees | 456 employees (non-consolidated) 1,833 employees (consolidated) (as of March 31, 2014) |
Business Items | Eslen Beads, Eslen Sheet, Pioseran, Lightron, Serpet, Neomicrolen, and other foam resin products. Tech Polymer, Techno Gel, and other functional materials. Agricultural and marine materials, food containers, distribution materials, construction materials, civil engineering materials, automotive components, vehicle parts packaging materials, industrial packaging materials, and other related products and systems |